Glass Melting Point: The Ultimate Guide You Need to Know!
The composition of glass significantly affects its glass melting point, an attribute crucial for various applications. Different types of glass, like soda-lime glass, possess unique melting points determined by their chemical makeup. Understanding viscosity, a key property of glass at high temperatures, is vital for controlling the manufacturing processes that involve specific glass melting points. Furthermore, the American Ceramic Society provides comprehensive resources and research related to the characteristics and behavior of glass materials, including detailed analyses of the glass melting point for diverse glass formulations.
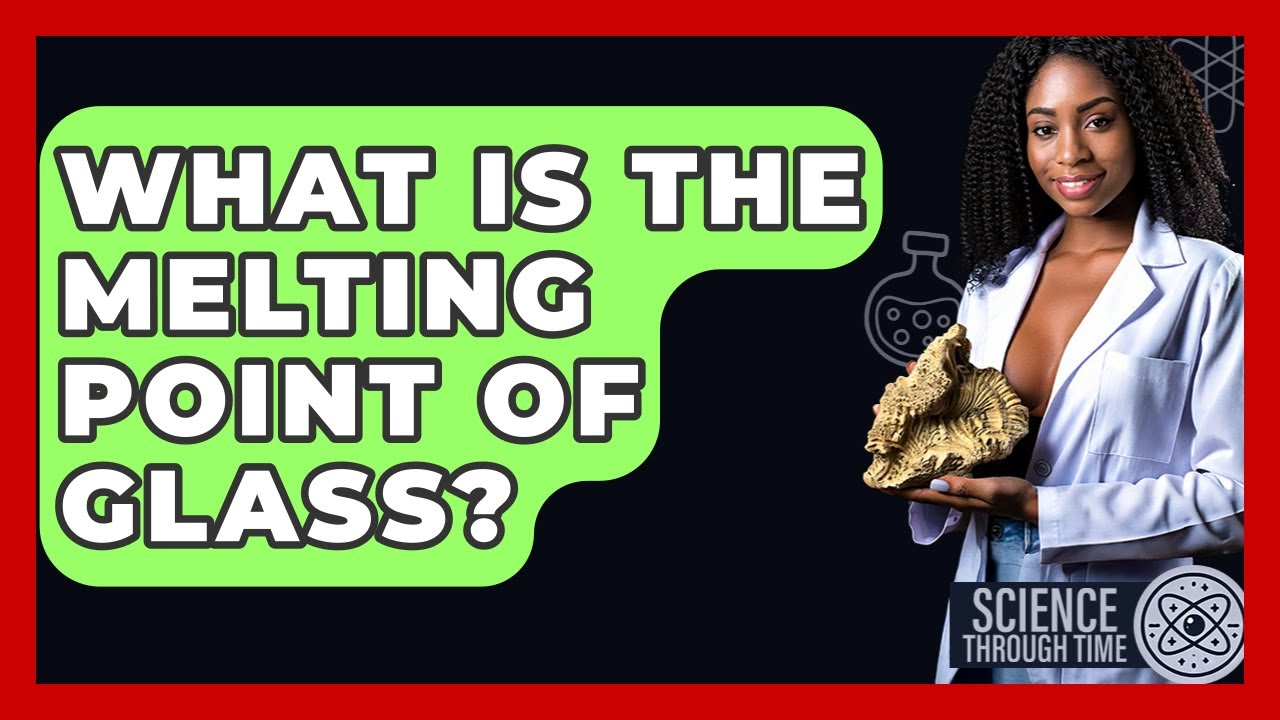
Image taken from the YouTube channel Science Through Time , from the video titled What Is The Melting Point Of Glass? - Science Through Time .
Glass, a ubiquitous material in our daily lives, often goes unnoticed despite its crucial role in countless applications. From the windows that frame our world to the screens we interact with daily, glass is indispensable. Understanding its properties, particularly its melting point, is paramount to unlocking its full potential and optimizing manufacturing processes.
Defining Glass: An Amorphous Solid
Unlike crystalline solids with their highly ordered atomic structures, glass possesses an amorphous structure.
This means that its atoms are arranged in a disordered, non-repeating pattern, similar to a frozen liquid. This unique atomic arrangement gives glass its characteristic properties, such as transparency, brittleness, and its gradual softening behavior upon heating, rather than a sharp, defined melting point like crystalline materials.
The Significance of Melting Point in Glass Manufacturing and Applications
The "melting point" of glass, more accurately described as its softening or working range, is a critical parameter in various manufacturing processes.
It dictates the temperature at which glass can be shaped, molded, and fused. Understanding this temperature range is crucial for:
- Efficient Production: Optimizing furnace temperatures for energy efficiency and minimizing defects.
- Shaping and Forming: Determining the appropriate techniques for creating desired shapes, whether blowing, casting, or pressing.
- Joining and Sealing: Ensuring proper fusion between different glass components or between glass and other materials.
- Application Suitability: Selecting the right type of glass for specific applications based on its thermal behavior and resistance to high temperatures.
A Spectrum of Glass Types: Properties and Applications
The world of glass is far more diverse than it appears. Different chemical compositions result in a wide array of glass types, each with its own unique properties and applications.
Here are some common examples:
-
Soda-Lime Glass: The most common and inexpensive type, used in windows, bottles, and everyday glassware.
-
Borosilicate Glass: Known for its exceptional thermal shock resistance, making it ideal for laboratory glassware, cookware (like Pyrex), and high-intensity lighting.
-
Lead Glass (Crystal): Characterized by its brilliance and clarity, often used in decorative items and optical components.
-
Fused Quartz: Composed almost entirely of silica, it boasts exceptional purity, high melting point, and excellent optical properties, suitable for high-temperature applications and specialized optics.
Each of these glass types exhibits a different melting point range due to variations in their chemical composition. Understanding these differences is essential for selecting the optimal material for a given application.
Glass, a ubiquitous material in our daily lives, often goes unnoticed despite its crucial role in countless applications. From the windows that frame our world to the screens we interact with daily, glass is indispensable. Understanding its properties, particularly its melting point, is paramount to unlocking its full potential and optimizing manufacturing processes.
Defining Glass: An Amorphous Solid
Unlike crystalline solids with their highly ordered atomic structures, glass possesses an amorphous structure.
This means that its atoms are arranged in a disordered, non-repeating pattern, similar to a frozen liquid. This unique atomic arrangement gives glass its characteristic properties, such as transparency, brittleness, and its gradual softening behavior upon heating, rather than a sharp, defined melting point like crystalline materials.
The Significance of Melting Point in Glass Manufacturing and Applications
The "melting point" of glass, more accurately described as its softening or working range, is a critical parameter in various manufacturing processes.
It dictates the temperature at which glass can be shaped, molded, and fused. Understanding this temperature range is crucial for:
Efficient Production: Optimizing furnace temperatures for energy efficiency and minimizing defects.
Shaping and Forming: Determining the appropriate techniques for creating desired shapes, whether blowing, casting, or pressing.
Joining and Sealing: Ensuring proper fusion between different glass components or between glass and other materials.
Application Suitability: Selecting the right type of glass for specific applications based on its thermal behavior and resistance to high temperatures.
A Spectrum of Glass Types: Properties and Applications
The world of glass is far more diverse than one might initially imagine. Before we delve deeper into the science of melting, it's important to remember the sheer variety of glass compositions and the influence this has on their thermal characteristics. This foundation sets the stage for understanding the nuances of glass transition and how it dictates workability.
The Science Behind Melting: A Deep Dive into Glass Transition
While we often use the term "melting point," understanding the behavior of glass at high temperatures requires a shift in perspective. Unlike crystalline substances that exhibit a sharp transition from solid to liquid at a specific temperature, glass undergoes a gradual softening process.
This is due to its amorphous nature, which results in a glass transition range rather than a distinct melting point. This section will delve deeper into the science behind this phenomenon.
Understanding the Glass Transition Range
The glass transition temperature (Tg) represents the point where glass transitions from a brittle, rigid solid to a more pliable, rubbery state.
However, it's not a precise temperature like the melting point of ice. Instead, it's a range where the viscosity of the glass gradually decreases as the temperature increases.
Above the glass transition temperature lies the working range, where the glass can be shaped and formed.
It is essential to understand that various methods are used to determine the glass transition temperature, and each can yield slightly different results for the same glass.
The Role of Chemical Composition
The chemical composition of glass plays a pivotal role in determining its glass transition temperature and overall thermal behavior.
Silica (SiO2) is the primary network former in most glasses, and its strong covalent bonds contribute to the high viscosity and relatively high softening temperatures.
However, pure silica glass has an exceptionally high melting point, making it difficult to work with.
To lower the softening temperature and improve workability, other oxides, known as network modifiers, are added.
These modifiers, such as sodium oxide (Na2O) or calcium oxide (CaO), disrupt the silica network, reducing the viscosity and lowering the glass transition temperature.
The type and concentration of these additives significantly influence the thermal properties of the resulting glass.
For example, adding boron oxide (B2O3) creates borosilicate glass, known for its superior thermal shock resistance due to its lower coefficient of thermal expansion.
Viscosity: The Key to Workability
Viscosity, a measure of a fluid's resistance to flow, is a crucial parameter in glass manufacturing. At room temperature, glass has an extremely high viscosity, behaving as a solid.
As the temperature increases, the viscosity decreases, allowing the glass to flow and be shaped.
The working range of glass is defined by the viscosity range suitable for different forming techniques.
For example, glass blowing requires a relatively low viscosity, while pressing or casting can be performed at higher viscosities.
The relationship between temperature and viscosity is not linear. Small changes in temperature can significantly impact viscosity, making precise temperature control essential during glass manufacturing.
Understanding the viscosity-temperature relationship allows manufacturers to select the appropriate temperature for each stage of the production process, ensuring optimal workability and minimizing defects.
A Spectrum of Glass Types provides a glimpse into the sheer diversity achievable by manipulating its composition. From the inexpensive windows in our homes to the specialized glassware in laboratories, each type boasts unique characteristics tailored to its specific application. Understanding these differences begins with examining some common examples and their distinct melting behaviors.
Exploring Common Glass Types and Their Melting Characteristics
Soda-Lime Glass: The Workhorse of the Glass World
Soda-lime glass reigns supreme as the most widely produced type of glass, accounting for approximately 90% of all manufactured glass. Its composition typically includes around 70% silica (SiO2), 15% soda (Na2O), and 9% lime (CaO), along with smaller amounts of other additives.
This composition makes it relatively inexpensive to produce and easy to work with, contributing to its widespread use.
Soda-lime glass exhibits good chemical durability and is suitable for a wide range of applications, but it is not particularly resistant to high temperatures or sudden temperature changes.
Properties and Applications
Soda-lime glass is known for its transparency, ease of shaping, and relatively low cost. These properties make it ideal for applications such as:
- Windows and Plate Glass: Its transparency and formability make it a primary choice for glazing.
- Bottles and Jars: Chemical durability and cost-effectiveness make it suitable for food and beverage containers.
- Light Bulbs: Transparency and electrical insulation properties make it useful for incandescent bulbs.
Melting Point Range
The melting point range of soda-lime glass typically falls between 1500°F (815°C) and 1650°F (900°C). This relatively lower melting point compared to other glass types contributes to its energy-efficient production.
Borosilicate Glass: High-Performance Thermal Resistance
Borosilicate glass is a type of glass that incorporates boron trioxide (B2O3) into its composition, typically ranging from 5% to 13%.
This addition of boron trioxide gives borosilicate glass superior thermal shock resistance and a higher melting point compared to soda-lime glass. It is more resistant to cracking when subjected to rapid temperature changes.
Properties and Applications
The enhanced thermal properties of borosilicate glass make it suitable for demanding applications where resistance to heat and thermal shock is crucial:
- Laboratory Glassware: Beakers, test tubes, and flasks benefit from its resistance to thermal stress and chemical corrosion.
- Ovenware and Cookware: Its ability to withstand high oven temperatures without shattering makes it a popular choice for bakeware.
- Pharmaceutical Packaging: Resistance to chemical leaching and thermal stability make it suitable for storing sensitive medications.
Melting Point
Borosilicate glass generally has a higher melting point than soda-lime glass, typically ranging from 1650°F (900°C) to 1830°F (1000°C). This higher melting point reflects the stronger network structure created by the addition of boron trioxide.
Comparing Melting Point Characteristics Across Different Glass Types
The table below highlights the differences in melting point ranges for common glass types:
Glass Type | Typical Melting Point Range (°F) | Typical Melting Point Range (°C) |
---|---|---|
Soda-Lime Glass | 1500 - 1650 | 815 - 900 |
Borosilicate Glass | 1650 - 1830 | 900 - 1000 |
Lead Glass | 1400 - 1600 | 760 - 870 |
Fused Quartz | Above 3000 | Above 1650 |
It's crucial to understand that these are ranges, not precise points, due to the amorphous nature of glass. The specific composition and manufacturing processes further influence the exact melting behavior.
Key Takeaways on Glass Types
Understanding the different types of glass and their associated melting characteristics is paramount for selecting the appropriate material for any given application. Soda-lime glass remains a versatile and cost-effective choice for everyday items. Borosilicate glass offers superior thermal performance in demanding environments. By carefully considering these factors, engineers and manufacturers can optimize their designs and processes for maximum performance and longevity.
A deeper understanding of individual glass types allows us to appreciate how precisely their compositions are formulated. The melting characteristics aren't arbitrary; they're carefully engineered. This begs the question: What exactly dictates whether a glass melts at a lower or higher temperature?
Decoding the Factors: What Influences Glass Melting Point?
The melting point of glass, while technically a softening range, is not a fixed property. It's a dynamic characteristic influenced by several interconnected factors. These factors provide levers that glass manufacturers can use to fine-tune the properties of their products.
The Crucial Role of Chemical Composition
Perhaps the most influential factor is the chemical composition of the glass itself. Glass is, at its heart, a mixture of various oxides, each contributing to its overall thermal behavior.
Modifying Glass Chemistry to Alter Melting Point
The primary network former in most glasses is silica (SiO2). Silica has a relatively high melting point. Introducing other oxides, known as network modifiers, disrupts the silica network.
This disruption lowers the melting point and improves workability. Soda (Na2O), for example, is a common network modifier.
However, adding too much soda can compromise the glass's chemical durability. Therefore, lime (CaO) is added as a stabilizer.
Other additives, such as alumina (Al2O3) or boron oxide (B2O3), can further influence the melting point.
Alumina generally increases the melting point and improves the glass's resistance to chemical attack. Boron oxide, as seen in borosilicate glass, lowers the melting point compared to pure silica glass, but it drastically improves thermal shock resistance.
The Impact of Individual Oxides
The specific types and proportions of these oxides will have a direct and predictable impact on the glass's melting behavior. By carefully adjusting the "recipe," manufacturers can tailor the melting point to suit the intended application.
Thermal Expansion and Its Connection to Melting Point
Thermal expansion refers to the tendency of a material to change in volume in response to temperature changes. There's a direct correlation between a glass's thermal expansion coefficient and its melting point.
Generally, glasses with lower thermal expansion coefficients tend to have higher melting points. This is because stronger bonds between the atoms are needed to resist expansion, which also requires more energy (higher temperatures) to break down during melting.
Borosilicate glass, again, serves as a prime example. Its low thermal expansion is a key reason for its excellent thermal shock resistance and also contributes to its higher melting point compared to soda-lime glass.
Softening Point, Annealing, and Their Relationship to Melting
While the melting point refers to the temperature range where the glass transitions from a solid to a molten state, the softening point is the temperature at which the glass becomes viscous enough to be easily shaped.
The softening point is always lower than the melting point. Understanding the softening point is critical for many glass forming processes.
The Importance of Annealing
Annealing is a crucial heat treatment process used to relieve internal stresses within the glass. It involves heating the glass to a temperature near its annealing point (which is also below the softening point) and then slowly cooling it down.
Rapid cooling can cause uneven contraction, leading to permanent stresses that weaken the glass and make it prone to cracking.
The annealing process does not directly change the melting point of the glass itself. However, it is integrally linked to the thermal history of the glass and ensures that the glass can withstand temperatures near its melting point without catastrophic failure in its intended application.
In summary, the melting point of glass is a complex property dictated by its chemical composition, thermal expansion, and the thermal processes it undergoes. Manipulating these factors allows for the creation of a wide range of glasses. Each tailored to specific applications with optimized thermal behaviors.
That careful manipulation of the chemical recipe is only half the story. Achieving the desired properties in the final glass product hinges critically on what happens after the melt. This is where the annealing process enters the picture, playing a vital role in determining the glass's strength, durability, and overall performance.
The Crucial Role of Annealing and Controlled Cooling
Annealing is a heat treatment process applied to glass after it has been formed. The process involves heating the glass to a specific temperature, holding it at that temperature for a set period, and then slowly cooling it down in a controlled manner.
This meticulous procedure is essential for relieving internal stresses that develop during the forming process. These stresses, if left unaddressed, can lead to catastrophic failure in the final product.
Understanding Stress in Glass Formation
As molten glass cools, different parts of the object cool at different rates. Thicker sections retain heat longer than thinner sections.
This uneven cooling leads to variations in contraction, with some areas solidifying and shrinking before others.
These differential contractions create internal stresses: some regions are in tension (being pulled apart), while others are in compression (being squeezed together).
Without intervention, these stresses can accumulate to a point where they exceed the glass's tensile strength. This then results in spontaneous cracking or shattering.
The Annealing Process: A Step-by-Step Explanation
The annealing process aims to mitigate these internal stresses through careful temperature management.
-
Heating: The glass object is heated to its annealing point. This is a temperature range just below the softening point, where the glass is still rigid enough to maintain its shape, but the viscosity is low enough to allow stress relaxation.
-
Soaking: The glass is held at the annealing point for a specific duration. This "soaking" period allows the atoms in the glass structure to rearrange themselves, relieving existing stresses. The duration depends on the glass type and the size/thickness of the object.
-
Controlled Cooling: This is the most critical stage. The glass is cooled very slowly and uniformly. The rate of cooling is precisely controlled to prevent the reintroduction of significant thermal gradients and, consequently, new stresses.
The cooling rate is often expressed in degrees per hour, and it can vary depending on the type of glass and the desired final properties.
Annealing's Relationship to the Glass Melting Point
While not directly defining the melting point itself, the annealing process is inextricably linked to it through the glass's characteristic temperatures.
The annealing point, softening point, and strain point are all related and dependent on the glass's chemical composition, which also governs its melting behavior.
-
Annealing Point: As previously discussed, the temperature at which stresses can be relieved within a reasonable timeframe (minutes).
-
Softening Point: The temperature at which the glass deforms readily under its own weight. This is higher than the annealing point.
-
Strain Point: The temperature below which stress relief is negligible. Below this temperature, any stresses introduced will be effectively "frozen" into the glass.
The closer these temperatures are to each other, the more challenging the annealing process becomes, demanding even more precise control over heating and cooling rates. Different types of glass have very different values and relationships between the numbers.
The Consequences of Improper Annealing
Failure to properly anneal glass can have severe consequences.
-
Reduced Strength: Internal stresses significantly weaken the glass, making it more susceptible to cracking and fracture under mechanical or thermal stress.
-
Increased Brittleness: Stressed glass is more brittle and less able to withstand impact.
-
Spontaneous Failure: In extreme cases, the internal stresses can be so high that the glass can shatter spontaneously, even without external forces.
Annealing Beyond Stress Relief: Enhancing Glass Properties
While stress relief is the primary goal, annealing can also be used to enhance other glass properties.
-
Improved Chemical Durability: In some cases, controlled cooling can lead to a more homogenous glass structure. This, in turn, improves its resistance to chemical attack.
-
Modified Optical Properties: Annealing can influence the refractive index and other optical properties of certain glasses.
In conclusion, annealing is an indispensable step in glass manufacturing. It ensures the structural integrity, durability, and overall performance of the final product. Understanding its relationship to the glass's melting characteristics is crucial for achieving optimal results.
That careful manipulation of the chemical recipe is only half the story. Achieving the desired properties in the final glass product hinges critically on what happens after the melt. This is where the annealing process enters the picture, playing a vital role in determining the glass's strength, durability, and overall performance.
Applications and Implications: From Production to Performance
The melting point of glass is not merely a scientific curiosity; it's a critical parameter that dictates the feasibility and efficiency of countless manufacturing processes and ultimately influences the performance of the final product. Understanding its profound implications allows for optimized production, informed material selection, and continued innovation within the glass industry.
The Manufacturing Process: A Symphony of Temperature
The melting point directly impacts several aspects of glass manufacturing, from energy consumption to shaping techniques.
High melting points generally translate to higher energy requirements during the melting and forming stages. This increase in energy consumption can lead to increased production costs and a larger environmental footprint.
Conversely, lower melting points may allow for more energy-efficient manufacturing processes, potentially reducing both cost and environmental impact.
The forming techniques employed are also heavily influenced by the glass's melting point. For instance, glasses with lower melting points and wider working ranges may be suitable for processes like blowing or pressing, while those with higher melting points might require more specialized techniques like casting or drawing.
The viscosity of the glass at various temperatures, which is related to its melting point, also dictates how easily it can be shaped and molded.
Selection Criteria: Matching Glass to Application
Choosing the right type of glass for a specific application requires careful consideration of its melting point alongside other properties like strength, thermal resistance, and chemical durability.
For applications involving high temperatures or sudden temperature changes, such as laboratory glassware or ovenware, borosilicate glass is often preferred due to its high melting point and excellent thermal shock resistance.
In contrast, soda-lime glass, with its lower melting point and cost-effectiveness, is widely used for windows, bottles, and other everyday applications where extreme temperature resistance is not a primary concern.
Selecting the appropriate glass based on its melting point is crucial for ensuring the product's performance, longevity, and safety. Mismatched materials can lead to premature failure, compromised performance, and even potential hazards.
R&D and Innovation: Pushing the Boundaries of Glass Technology
The melting point of glass plays a vital role in research, development, and innovation within the industry. Scientists and engineers are constantly exploring new glass compositions and processing techniques to achieve desired properties and expand the range of applications for glass materials.
By carefully manipulating the chemical composition of glass, researchers can tailor its melting point to suit specific needs. For example, efforts are underway to develop new types of low-melting-point glasses for use in advanced electronic devices and coatings.
Understanding the relationship between melting point, viscosity, and other properties is also crucial for developing novel glass processing techniques, such as 3D printing of glass and the creation of complex glass structures with tailored properties.
The ongoing research and development efforts focused on glass melting points are driving innovation and paving the way for new and exciting applications of this versatile material.
Video: Glass Melting Point: The Ultimate Guide You Need to Know!
FAQs About Glass Melting Point
Here are some frequently asked questions about glass melting point, designed to clarify key concepts from our guide.
What exactly does the "glass melting point" refer to?
The glass melting point isn't a single, precise temperature like water's freezing point. Instead, it refers to a range where the glass transitions from a solid to a viscous, moldable state. This softening point is crucial for glassworking.
Why do different types of glass have different melting points?
The glass melting point varies depending on its composition. Different additives, like boron or lead, alter the temperature at which the glass softens and becomes workable. Soda-lime glass, borosilicate glass, and lead crystal all have distinct melting points.
Is the glass melting point the same as its working point?
No, the glass melting point is a general range. The "working point" is a specific temperature within that range where the glass has the ideal viscosity for shaping and manipulation. It's a more precise temperature for practical glassblowing and forming.
How does understanding the glass melting point help me?
Knowing the glass melting point is crucial for any glass-related activity, whether you're recycling glass, casting, blowing, or experimenting with fusing. It ensures you can work with the material effectively and safely, preventing cracking or incomplete melting.
So, there you have it – a deep dive into the world of glass melting point! Hopefully, you now have a better grasp of this fascinating topic. If you ever find yourself wondering about the properties of glass, remember to consider its melting point. Until next time!