Delta Temperature: The Ultimate Guide You Need to Know
Understanding delta temperature is critical for optimizing efficiency across various applications. HVAC systems, for instance, rely heavily on accurate delta temperature measurements to ensure optimal performance and energy conservation. The American Society of Heating, Refrigerating and Air-Conditioning Engineers (ASHRAE) sets standards that often reference acceptable delta temperature ranges for different system types. Furthermore, instruments like infrared thermometers are often used to non-invasively measure delta temperature in industrial settings. This guide explores the concept of delta temperature, detailing its importance, calculation methods, and real-world applications.
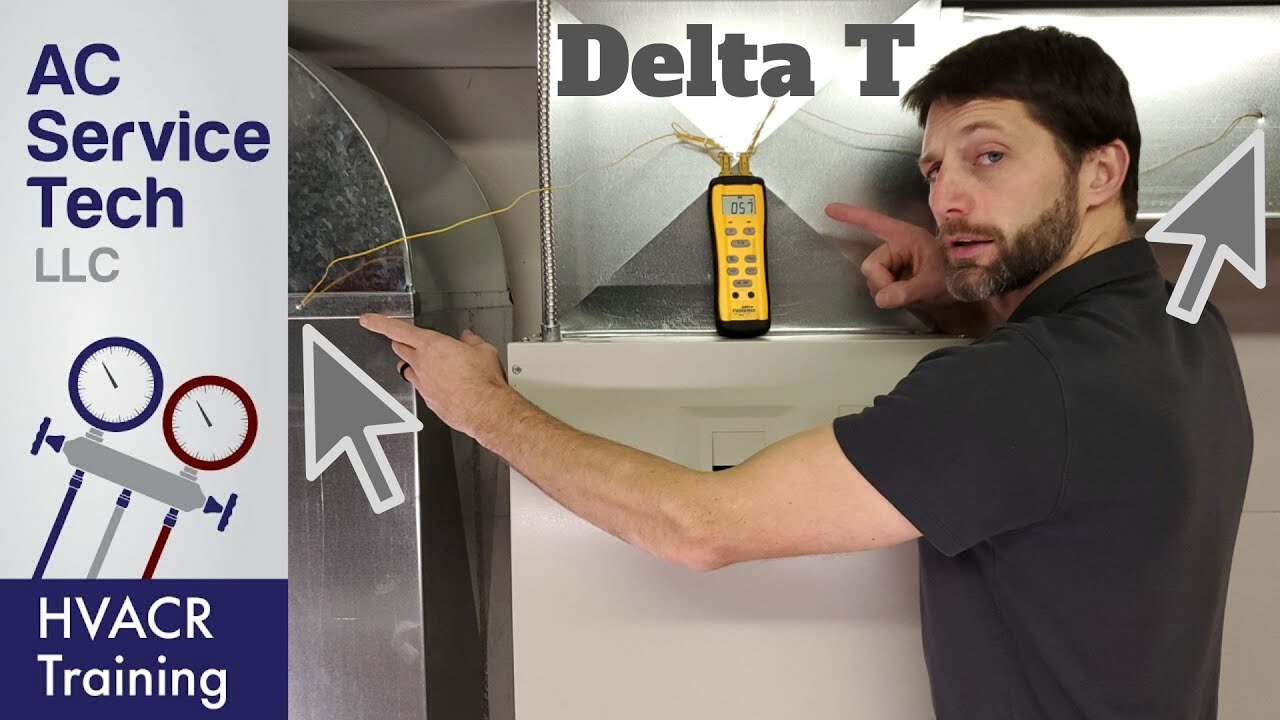
Image taken from the YouTube channel AC Service Tech LLC , from the video titled HVAC Delta T Explained! What Temperature Should it be? .
Understanding Delta Temperature: A Foundational Concept
Delta temperature, often represented as ΔT, is a deceptively simple concept with profound implications across a multitude of scientific and engineering disciplines. It fundamentally represents the difference between two temperature measurements.
While this definition seems straightforward, its significance stems from its ability to reveal critical information about processes, systems, and environments.
The Essence of ΔT: Difference and Change
At its core, delta temperature quantifies change. It's not merely about knowing the absolute temperature at a single point, but rather understanding how temperature varies across space or time. This difference provides insights into energy flow, system efficiency, and process stability.
The "delta" signifies this change, highlighting the dynamic nature of temperature rather than its static value.
Think of it like this: knowing the temperature of a room is useful, but knowing the difference between the supply air temperature and the room temperature tells you much more about the effectiveness of the HVAC system.
Significance Across Diverse Contexts
The power of delta temperature lies in its versatility. It's a crucial parameter in diverse fields, acting as a key indicator and control variable.
Heating, Ventilation, and Air Conditioning (HVAC)
In HVAC systems, ΔT is paramount for assessing performance. It helps optimize energy consumption, ensure comfortable indoor environments, and diagnose potential malfunctions.
Process Control
Chemical reactions, manufacturing processes, and food production all rely heavily on maintaining specific temperature ranges. Delta temperature helps control these processes and ensures quality and safety.
Fluid Dynamics and Heat Exchangers
The efficiency of heat exchangers and the behavior of fluids are deeply influenced by temperature gradients. Understanding and managing ΔT is crucial for optimizing performance in these applications.
Beyond the Common Applications
These are just a few examples. From electronics thermal management to climate science, delta temperature plays a vital role.
A Roadmap to Mastering ΔT
This discussion serves as a gateway to a comprehensive exploration of delta temperature. We aim to empower you with the knowledge and insights needed to effectively understand, measure, and utilize ΔT in your respective fields.
By the end of this guide, you will gain:
- A solid understanding of the fundamental principles behind temperature measurement and heat transfer.
- The ability to interpret delta temperature readings in various contexts.
- Knowledge of the tools and techniques used to monitor and analyze temperature data.
Ultimately, this guide will equip you to harness the power of delta temperature for enhanced performance, improved efficiency, and informed decision-making.
Core Concepts: Temperature Measurement and Heat Transfer
The power of delta temperature stems from its capacity to illuminate change, giving insights into system behavior. However, before delving into specific applications, it's crucial to establish a firm grasp of the foundational principles that make accurate ΔT calculations possible: temperature measurement techniques and the mechanisms of heat transfer.
Temperature Measurement: Accuracy and Methods
Accurate temperature measurement is the cornerstone of any meaningful delta temperature analysis. The reliability of ΔT values hinges directly on the precision and consistency of the individual temperature readings that comprise it. Various methods exist for measuring temperature, each with its own strengths, limitations, and inherent accuracy levels. Understanding these differences is vital for selecting the appropriate method for a given application and interpreting the resulting data.
Thermocouples: Versatile and Robust
Thermocouples are widely used temperature sensors known for their versatility and ruggedness. They operate based on the Seebeck effect, which generates a small voltage proportional to the temperature difference between two dissimilar metal junctions.
They are relatively inexpensive, can measure a wide range of temperatures, and are available in various configurations. However, thermocouples are less accurate than some other types of sensors, and their output voltage is nonlinear, requiring compensation. Moreover, they require cold-junction compensation to provide an accurate reading.
Resistance Temperature Detectors (RTDs): Precision and Stability
RTDs offer higher accuracy and stability compared to thermocouples. They rely on the principle that the electrical resistance of a metal changes predictably with temperature. Platinum is commonly used in RTDs due to its excellent temperature coefficient of resistance, stability, and chemical inertness.
RTDs provide a more linear output than thermocouples, simplifying signal conditioning. However, they are generally more expensive and have a slower response time. Also, they require an excitation current, which can cause self-heating and introduce errors if not properly managed.
Infrared Thermometers: Non-Contact Measurement
Infrared (IR) thermometers enable non-contact temperature measurement by detecting the infrared radiation emitted by an object. This is particularly useful for measuring the temperature of moving objects, hazardous materials, or surfaces that are difficult to access.
IR thermometers are convenient and provide rapid readings. However, their accuracy is affected by the emissivity of the target material, which is a measure of its ability to emit infrared radiation. Emissivity must be accurately known or compensated for to obtain reliable results. Ambient temperature, distance to the target, and atmospheric conditions can also influence the accuracy of IR thermometers.
Heat Transfer: The Mechanisms Behind ΔT
Delta temperature is intrinsically linked to the fundamental modes of heat transfer: conduction, convection, and radiation. These processes dictate how thermal energy moves between objects or systems, ultimately influencing the temperature differences that we observe and measure. Understanding these mechanisms is essential for interpreting ΔT values and drawing meaningful conclusions about system behavior.
Conduction: Heat Transfer Through Solids
Conduction is the transfer of heat through a material by direct contact. Heat flows from regions of higher temperature to regions of lower temperature. The rate of heat transfer depends on the material's thermal conductivity, the temperature gradient, and the cross-sectional area.
In the context of delta temperature, conduction plays a crucial role in determining the temperature distribution within solid objects, such as heat sinks or building materials. High thermal conductivity materials will minimize the temperature difference across them for a given heat flow.
Convection: Heat Transfer Through Fluids
Convection involves heat transfer through the movement of fluids (liquids or gases). There are two types of convection: natural convection, driven by density differences caused by temperature variations, and forced convection, where fluid movement is induced by external means (e.g., a fan or pump).
Delta temperature is critical in convective heat transfer, as it drives the fluid motion and influences the rate of heat exchange. For example, the ΔT between a heated surface and the surrounding air determines the rate of natural convection cooling.
Radiation: Heat Transfer Through Electromagnetic Waves
Radiation is the transfer of heat through electromagnetic waves, which can travel through a vacuum. All objects emit thermal radiation, and the amount of radiation emitted depends on their temperature and emissivity.
Delta temperature dictates the net radiative heat transfer between two objects. The larger the temperature difference, the greater the net heat transfer from the hotter object to the cooler one. This principle is fundamental to understanding heat loss from buildings, the operation of solar collectors, and many other thermal processes.
Reliable Temperature Measurement: The Key to Accurate ΔT
In conclusion, the value and accuracy of delta temperature calculations rest squarely on the foundation of reliable temperature measurement. Understanding the strengths and limitations of various temperature sensors, as well as the fundamental modes of heat transfer, allows for informed selection of appropriate measurement techniques and meaningful interpretation of results. Accurate determination of ΔT is not merely an academic exercise; it is a critical step in optimizing performance, ensuring safety, and achieving desired outcomes across a multitude of applications. Without this foundation, efforts to leverage ΔT for system understanding and control are fundamentally compromised.
Delta Temperature in HVAC Systems: Maintaining Comfort and Efficiency
Having established the critical importance of accurate temperature measurements and a foundational understanding of heat transfer principles, we can now explore a tangible application of delta temperature. HVAC (Heating, Ventilation, and Air Conditioning) systems offer a compelling example of how understanding and leveraging ΔT can lead to significant improvements in both energy efficiency and occupant comfort.
This section delves into the specific ways delta temperature is utilized within HVAC systems to monitor performance, diagnose problems, and optimize overall operation.
Monitoring HVAC Performance with ΔT
Delta temperature serves as a crucial indicator of HVAC system performance. By measuring the temperature difference between the supply and return air, operators can gain valuable insights into the system's ability to effectively heat or cool a space. A healthy ΔT indicates efficient heat exchange, while deviations from the norm often signal underlying issues.
Ideal ΔT Ranges: Cooling and Heating
The ideal delta temperature range varies depending on whether the system is in cooling or heating mode.
-
Cooling Mode: In a typical cooling system, the supply air temperature should be significantly lower than the return air temperature. Generally, a ΔT of 15-20°F (8-11°C) is considered optimal. This range indicates that the system is effectively removing heat from the space.
-
Heating Mode: Conversely, in heating mode, the supply air temperature should be higher than the return air temperature. An ideal ΔT in heating mode often falls within the 20-30°F (11-17°C) range. This signifies efficient heat delivery to the conditioned space.
It's important to note that these are just general guidelines, and the ideal ΔT can vary depending on factors such as system design, building characteristics, and environmental conditions.
Diagnosing Problems Through ΔT Deviations
Deviations from the ideal delta temperature range can indicate a variety of problems within the HVAC system. Analyzing these deviations allows for targeted troubleshooting and timely maintenance, preventing further inefficiencies and potential breakdowns.
-
Reduced Airflow: A low ΔT in either cooling or heating mode can be a sign of reduced airflow across the coil. This could be due to clogged air filters, blocked ducts, or a malfunctioning blower motor. Insufficient airflow diminishes the system's capacity to transfer heat effectively.
-
Refrigerant Leaks: In cooling systems, a higher than expected ΔT can suggest a refrigerant leak. The lack of refrigerant reduces the system's ability to absorb heat, leading to a smaller temperature difference.
-
Compressor Issues: Problems with the compressor, the heart of the cooling system, can also impact ΔT. An inefficient compressor may struggle to maintain the desired cooling capacity, resulting in a higher than normal ΔT.
-
Damper Problems: In zoned HVAC systems, improperly functioning dampers can cause imbalances in airflow and temperature, leading to inconsistent ΔT values across different zones.
Energy Consumption and Cost Savings
Maintaining an optimal delta temperature is crucial for minimizing energy consumption and maximizing cost savings in HVAC systems. An inefficient system, characterized by a suboptimal ΔT, will consume more energy to achieve the desired temperature, leading to higher utility bills.
By monitoring ΔT and addressing any issues that cause deviations from the ideal range, building owners and operators can significantly reduce their energy footprint and lower operating costs. Implementing regular maintenance schedules and utilizing advanced control systems to optimize ΔT are key strategies for achieving these benefits. Furthermore, the increased efficiency leads to a reduction in carbon emissions, contributing to a more sustainable environment.
Delta Temperature in Process Control: Ensuring Quality and Stability
Having explored the crucial role of delta temperature in HVAC systems, enabling efficient climate control and energy savings, it’s time to turn our attention to another domain where ΔT plays a pivotal role: process control. Here, the stakes are often even higher, with delta temperature directly impacting product quality, safety, and the overall efficiency of industrial operations.
This section will illuminate the diverse applications of delta temperature in maintaining optimal process conditions, ensuring consistent outcomes, and preventing potentially dangerous deviations.
Monitoring and Controlling Processes with ΔT
In numerous industrial settings, the rate and outcome of a process are intrinsically linked to temperature. Delta temperature serves as a key performance indicator (KPI), providing real-time insights into the progress and stability of these processes. By meticulously monitoring the temperature difference between critical points, operators can proactively adjust parameters to maintain optimal conditions.
This is particularly crucial in scenarios involving:
-
Chemical Reactions: Many chemical reactions are highly sensitive to temperature. Precise ΔT control ensures consistent reaction rates, prevents runaway reactions, and maximizes product yield.
-
Manufacturing Processes: From plastics molding to metal forming, maintaining specific temperature gradients is essential for achieving desired material properties and dimensional accuracy.
-
Heat Exchangers: Monitoring the ΔT across a heat exchanger allows operators to assess its efficiency and identify potential fouling or other issues that could compromise its performance.
The ability to effectively monitor and control these processes hinges on accurate and reliable temperature measurements at strategic locations.
Applications Across Industries
The applications of delta temperature in process control are vast and varied, spanning across numerous industries.
Let's examine a few specific examples:
-
Food Processing: In pasteurization and sterilization processes, maintaining a precise ΔT ensures the elimination of harmful microorganisms while preserving the nutritional value and flavor of the food product.
-
Pharmaceutical Manufacturing: Precise temperature control is paramount in drug synthesis and formulation. Delta temperature monitoring ensures the integrity of sensitive ingredients and prevents unwanted side reactions.
-
Semiconductor Fabrication: During chip manufacturing, extremely precise temperature control is critical for depositing thin films and etching intricate patterns. Variations in ΔT can lead to defects and reduced performance.
-
Wastewater Treatment: In anaerobic digestion, maintaining a consistent ΔT within the digester promotes the growth of beneficial bacteria and optimizes the breakdown of organic matter.
These examples illustrate the critical role that delta temperature plays in ensuring product quality, safety, and efficiency across diverse industries.
Role of Sensors and Control Systems
Achieving precise delta temperature control requires a sophisticated interplay of sensors, control systems, and actuators. Temperature sensors, strategically placed throughout the process, provide continuous feedback to the control system. This data is then used to make real-time adjustments to heating or cooling elements, flow rates, or other process parameters to maintain the desired ΔT range.
Advanced control algorithms, such as PID (proportional-integral-derivative) controllers, are often employed to optimize the control response and minimize deviations from the setpoint. The control system must also be designed to handle disturbances and unexpected variations in the process, ensuring that the ΔT remains within acceptable limits.
Sophisticated control systems often incorporate alarms and safety interlocks that trigger automatically if the delta temperature deviates beyond pre-defined thresholds. These safety mechanisms are critical for preventing equipment damage, protecting personnel, and ensuring environmental compliance.
Impact of ΔT Variations
Even slight variations in delta temperature can have significant consequences for product quality and process stability.
Consider these potential impacts:
-
Reduced Product Quality: Deviations from the optimal ΔT range can lead to inconsistent material properties, dimensional inaccuracies, or unwanted chemical reactions, ultimately impacting the quality and performance of the final product.
-
Process Instability: Uncontrolled temperature fluctuations can disrupt the equilibrium of the process, leading to oscillations, runaway reactions, or even catastrophic failures.
-
Increased Waste and Rework: Off-spec products resulting from ΔT variations may need to be scrapped or reworked, increasing waste and reducing overall efficiency.
-
Safety Hazards: In some cases, uncontrolled temperature excursions can create safety hazards, such as explosions, fires, or the release of hazardous materials.
Therefore, maintaining tight control over delta temperature is not only essential for optimizing process performance but also for ensuring the safety and sustainability of industrial operations.
Sensors and Data Analysis: Unlocking the Power of Delta Temperature
Successfully harnessing the power of delta temperature hinges on two critical elements: the selection of appropriate sensors for accurate measurement and the application of robust data analysis techniques to extract meaningful insights. Without these tools, the potential benefits of monitoring ΔT remain largely untapped.
This section delves into the intricacies of temperature sensors and data analysis, providing a comprehensive overview of the technologies and methodologies employed to transform raw temperature readings into actionable intelligence.
Understanding Temperature Sensor Technologies
The foundation of any delta temperature monitoring system lies in the accuracy and reliability of its temperature sensors. A diverse range of sensor types are available, each with its own unique characteristics, advantages, and limitations. Selecting the right sensor for a specific application is paramount to obtaining meaningful and dependable ΔT measurements.
Thermocouples: Versatility and Ruggedness
Thermocouples are among the most widely used temperature sensors in industrial applications. These devices operate based on the Seebeck effect, generating a voltage proportional to the temperature difference between two dissimilar metal junctions.
Their key advantages include a wide temperature range, robustness, and relatively low cost. However, thermocouples typically offer lower accuracy compared to other sensor types and require cold-junction compensation to mitigate errors.
Resistance Temperature Detectors (RTDs): Precision and Stability
RTDs are known for their high accuracy and stability. These sensors utilize a metal resistor, typically platinum, whose resistance changes predictably with temperature.
RTDs offer excellent linearity and repeatability, making them well-suited for applications requiring precise temperature measurements. However, they tend to be more expensive and have a slower response time than thermocouples.
Thermistors: Sensitivity and Responsiveness
Thermistors are semiconductor devices whose resistance is highly sensitive to temperature changes. They offer a high degree of sensitivity and a fast response time, making them ideal for applications where rapid temperature fluctuations need to be detected.
However, thermistors typically have a limited temperature range and can exhibit nonlinear behavior, requiring careful calibration.
Infrared (IR) Sensors: Non-Contact Measurement
Infrared sensors offer a unique advantage: the ability to measure temperature without direct contact with the target object. These sensors detect thermal radiation emitted by the object and convert it into a temperature reading.
IR sensors are particularly useful for measuring the temperature of moving objects, hazardous materials, or surfaces that are difficult to access. However, their accuracy can be affected by factors such as emissivity and ambient conditions.
Data Acquisition and Analytical Techniques
Once temperature data has been acquired, it must be effectively analyzed to extract meaningful insights and inform decision-making. A range of data acquisition systems and analytical techniques are available to facilitate this process.
Data Loggers: Autonomous Data Collection
Data loggers are standalone devices that automatically record temperature data over time. They are typically battery-powered and can store large amounts of data, making them ideal for long-term monitoring applications.
Data loggers are often used in remote locations or in situations where continuous monitoring is required.
SCADA Systems: Real-Time Monitoring and Control
Supervisory Control and Data Acquisition (SCADA) systems provide a comprehensive platform for real-time monitoring and control of industrial processes. SCADA systems collect data from various sensors, including temperature sensors, and present it to operators in a user-friendly interface.
These systems also allow operators to remotely adjust process parameters to maintain desired delta temperature ranges.
Statistical Process Control (SPC) Charts: Identifying Trends and Anomalies
Statistical Process Control (SPC) charts are powerful tools for monitoring process stability and identifying trends or anomalies in temperature data. These charts graphically display temperature measurements over time, along with statistical control limits.
By analyzing SPC charts, operators can quickly detect deviations from normal operating conditions and take corrective action before they lead to quality problems or safety hazards.
Leveraging Data Analysis for Proactive Problem Solving
The ultimate goal of delta temperature monitoring is not simply to collect data, but to use that data to improve process performance, enhance product quality, and prevent potential problems. By applying appropriate data analysis techniques, organizations can unlock the full potential of their ΔT monitoring systems.
Data analysis can be used to identify trends in temperature data, such as gradual increases or decreases that may indicate equipment degradation or process drift. Anomalies, such as sudden temperature spikes or dips, can also be detected and investigated.
By proactively addressing these issues, organizations can prevent costly downtime, reduce waste, and improve overall operational efficiency. Furthermore, effective data analysis can provide valuable insights into the underlying causes of process variations, enabling organizations to optimize their operations and achieve greater levels of consistency and control.
Beyond the Basics: Applications and Critical Considerations for Delta Temperature
Having explored the core applications of delta temperature (ΔT) in HVAC and process control, it's essential to broaden our perspective. While these are prominent examples, ΔT plays a crucial, if often understated, role in a variety of other fields.
Furthermore, understanding the limitations inherent in ΔT measurements and knowing where to seek further expertise are vital for accurate interpretation and application of this powerful metric.
Delta Temperature in Fluid Dynamics and Heat Transfer Equipment
Fluid dynamics offers numerous applications for ΔT, particularly in the analysis and optimization of heat exchangers. These devices, critical in various industries, rely on efficient heat transfer between two fluids.
ΔT measurements across a heat exchanger's inlet and outlet points provide a direct indication of its performance. A lower-than-expected ΔT might signal fouling, reduced flow rates, or other inefficiencies that compromise heat transfer.
Analyzing ΔT profiles within computational fluid dynamics (CFD) simulations offers a powerful tool for optimizing heat exchanger design, identifying areas of stagnation, and improving overall thermal performance.
Thermal Management in Electronics and Systems
As electronic devices become increasingly powerful and compact, effective thermal management becomes paramount. Excessive heat generation can lead to performance degradation, reduced lifespan, and even catastrophic failure.
ΔT measurements are critical in monitoring the thermal behavior of electronic components and systems. By measuring the temperature difference between a heat sink and the ambient air, or between a component's surface and its internal temperature, engineers can assess the effectiveness of cooling solutions.
This data informs design decisions, optimizing heat sink selection, fan placement, and other thermal management strategies to ensure reliable operation within safe temperature limits. Effective thermal management is vital for product longevity and performance.
Acknowledging Limitations and Sources of Error
While ΔT is a valuable metric, it's essential to acknowledge its limitations and potential sources of error. Inaccurate temperature sensors are a primary concern.
Calibration drift, environmental factors, and sensor placement can all introduce inaccuracies that propagate through ΔT calculations.
Environmental factors such as airflow and ambient temperature variations must be considered during data interpretation. Ensure sensors are properly shielded and calibrated, and that data is collected under controlled conditions whenever possible.
Furthermore, the accuracy of ΔT calculations depends on the resolution of the temperature sensors used. Sensors with limited resolution may not capture subtle temperature differences, leading to inaccurate or misleading results.
Resources for Further Learning and Professional Guidance
This overview provides a foundation for understanding and applying delta temperature. However, the complexities of specific applications may require deeper knowledge and specialized expertise.
For those seeking to expand their understanding of ΔT, numerous resources are available. Reputable online courses, technical publications, and industry conferences can offer in-depth knowledge and practical insights.
Professional consultation with thermal engineers, HVAC specialists, or process control experts can provide valuable guidance for specific applications. Seeking expert advice ensures accurate measurement, effective analysis, and optimal implementation of delta temperature monitoring.
Video: Delta Temperature: The Ultimate Guide You Need to Know
Frequently Asked Questions About Delta Temperature
Here are some common questions we receive about delta temperature and its uses. Hopefully, these answers will provide further clarity on the topic.
What exactly is delta temperature?
Delta temperature refers to the difference in temperature between two points. It's calculated by subtracting the initial temperature from the final temperature. This measurement is critical in many applications, from HVAC systems to scientific experiments.
Why is delta temperature important?
Understanding the delta temperature allows you to assess the efficiency of processes and systems. For example, in cooling systems, a large delta temperature might indicate efficient heat transfer, while a small delta temperature could suggest inefficiencies.
How do you calculate delta temperature?
The formula for calculating delta temperature is simple: ΔT = T₂ - T₁, where ΔT represents the delta temperature, T₂ is the final temperature, and T₁ is the initial temperature. Make sure your temperature measurements are in the same unit (Celsius or Fahrenheit).
What are some practical applications of delta temperature?
Delta temperature measurements are essential in HVAC (heating, ventilation, and air conditioning) systems for optimizing airflow and temperature control. It's also used in manufacturing to monitor process temperatures and in scientific research to analyze thermal changes in experiments.