Unlock Elastic Energy: The Ultimate Guide You Need to Read!
Understanding elastic energy is crucial for grasping principles behind various physical phenomena. Springs, ubiquitous in mechanics, store potential energy when compressed or stretched, directly related to elastic energy. The study of materials, specifically through the lens of Hooke's Law, provides fundamental equations to quantify elastic energy. Notably, biomechanics applies these concepts to analyze movement, demonstrating elastic energy's role in activities. Thus, our ultimate guide aims to unlock a deep understanding of elastic energy.
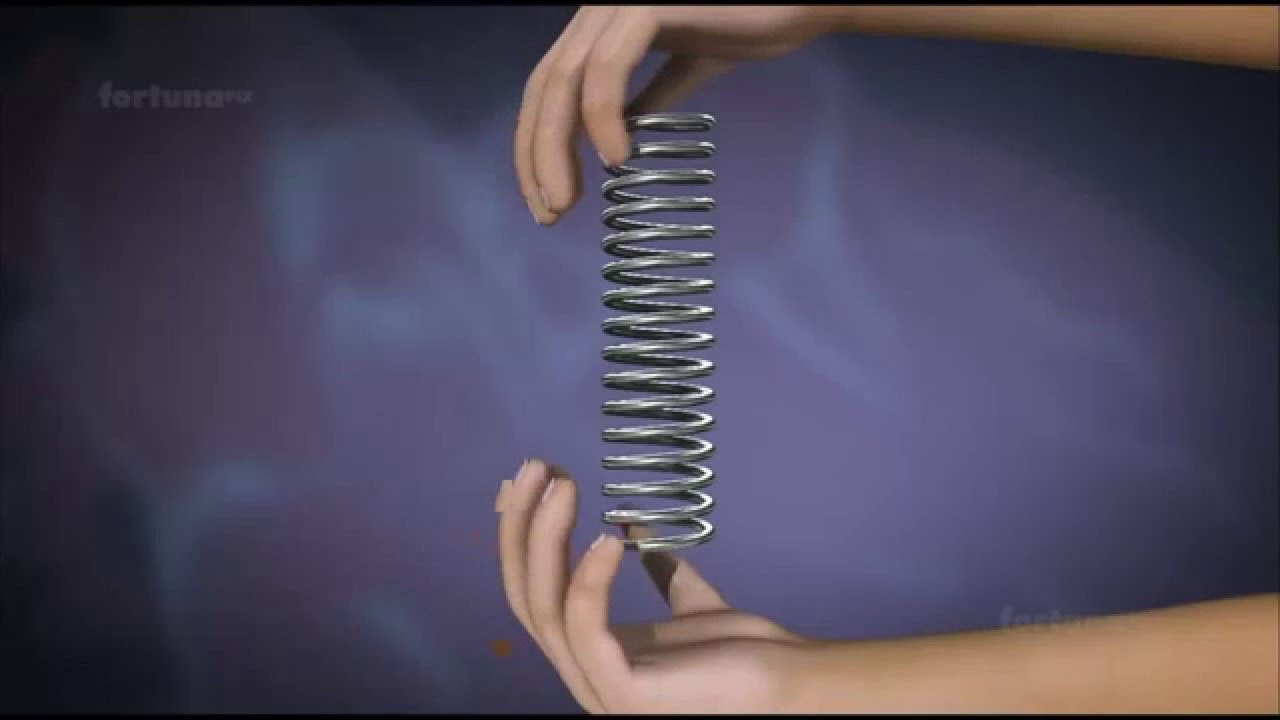
Image taken from the YouTube channel Nicholas Eidle , from the video titled Elastic Potential Energy .
Elastic energy is a fundamental form of energy that quietly shapes our world, often unnoticed yet ever-present. It's the unseen force behind a bouncing ball, the resilience of a trampoline, and the controlled release in a precisely engineered spring.
At its core, elastic energy is the potential energy stored in a deformable object. This storage happens when an external force causes the object to change shape, be it stretching, compressing, or twisting.
What is Elastic Energy? A Simple Explanation
Imagine stretching a rubber band. As you pull, you're doing work, and that work isn't lost. Instead, it's transformed into elastic potential energy stored within the rubber band's molecular structure.
This stored energy waits patiently, ready to be unleashed the moment you release the tension. The rubber band snaps back, converting the stored potential energy into kinetic energy—the energy of motion.
Elastic Energy: From Playtime to High-Tech
The reach of elastic energy extends far beyond simple toys. It is a cornerstone of countless applications, spanning from the playful to the profoundly practical.
Consider the humble spring. It is a key component in everything from car suspensions, absorbing bumps and ensuring a smooth ride, to the intricate mechanisms of mechanical watches, driving the delicate dance of gears and hands.
In engineering, elastic energy principles are vital for designing structures that can withstand stress and deformation. Understanding how materials store and release energy is crucial for building safer bridges, resilient buildings, and efficient machines.
The Principle of Storage and Release
The beauty of elastic energy lies in its elegant cycle of storage and release. When a force deforms an elastic material, the material resists that deformation. This resistance manifests as stored potential energy.
Upon the removal of the deforming force, the material springs back to its original shape, releasing the stored energy. This release can be gradual and controlled, as in a shock absorber, or sudden and explosive, as in a catapult.
This ability to store and release energy on demand makes elastic materials invaluable in various applications.
A Roadmap to Understanding Elastic Energy
This guide will explore the fascinating world of elastic energy in detail, providing a comprehensive understanding of its underlying principles, real-world applications, and technological potential.
We will delve into Hooke's Law, the mathematical relationship governing elastic behavior, and examine how different materials respond to deformation.
We will showcase everyday examples of elastic energy, from simple springs to complex systems like bungee jumping, and explore the factors that influence energy storage capacity.
Finally, we will examine the exciting potential of elastic energy in technological advancements, from energy storage systems to shock absorption technologies.
Join us on this journey to uncover the power and versatility of elastic energy, a force that shapes our world in countless ways.
The Principle of Storage and Release
As we’ve seen, elastic energy showcases a fascinating interplay between potential and kinetic forms. But what are the underlying scientific principles that govern this behavior? Delving into the specifics requires a closer look at elastic potential energy, Hooke's Law, and the relationships between force, displacement, and energy within an elastic system.
The Science Behind the Stretch: Understanding Elastic Potential Energy
The world of elastic energy may seem simple, but behind every stretched spring and bouncing ball lies a rich set of scientific principles. Understanding these principles allows us to not only appreciate the phenomenon but also to harness its potential for various applications.
Defining Elastic Potential Energy
At its core, elastic potential energy is the potential energy stored in a deformable object when it's stretched or compressed. It represents the energy that is ready to be converted into other forms, such as kinetic energy, once the deforming force is removed.
Think of it as the "stored work" done to change the object's shape.
The amount of elastic potential energy stored is directly related to the stiffness of the object and the extent of its deformation.
The formula for elastic potential energy (U) is:
U = (1/2) k x²
Where:
- U represents the elastic potential energy (measured in Joules, J).
- k is the spring constant (measured in Newtons per meter, N/m), which indicates the stiffness of the material. A higher k value means a stiffer material.
- x is the displacement or the change in length from the object's equilibrium position (measured in meters, m).
Hooke's Law: The Foundation of Elasticity
Unveiling Hooke's Law
Hooke's Law is a fundamental principle that describes the relationship between the force required to stretch or compress a spring (or other elastic material) and the distance of that stretch or compression.
It states that the force (F) needed is directly proportional to the displacement (x).
This relationship is expressed mathematically as:
F = -kx
Where:
- F is the force applied (measured in Newtons, N).
- k is the spring constant (as described above).
- x is the displacement (measured in meters, m).
- The negative sign indicates that the force exerted by the spring is in the opposite direction to the displacement. This is a restoring force, pulling or pushing the object back to its equilibrium position.
Spring Constant (k): A Measure of Stiffness
The spring constant (k) is a crucial property of an elastic material. It quantifies the stiffness of the material. Materials with high spring constants require more force to achieve a given displacement.
For example, a stiff metal spring will have a higher k value than a flimsy rubber band.
Understanding the spring constant is essential for designing systems that rely on elastic energy.
Limitations of Hooke's Law
It is important to remember that Hooke's Law is a model that works well under certain conditions. Specifically, Hooke's Law holds true only within the elastic limit of the material.
Beyond this limit, the material will undergo permanent deformation, and Hooke's Law no longer applies.
At extreme deformations, the material's behavior becomes nonlinear, and the relationship between force and displacement is no longer directly proportional. Exceeding the elastic limit can lead to material failure or permanent changes to the elastic properties of the material.
The Interplay of Potential, Kinetic, and Elastic Energy
Within a system involving elastic energy, potential energy, kinetic energy, and elastic energy are constantly interchanging.
When an object is deformed, kinetic energy (energy of motion) is converted into elastic potential energy (stored energy). When the object is released, the elastic potential energy is converted back into kinetic energy, causing motion.
For example, when you compress a spring, you're using kinetic energy from your hand to do work on the spring and convert the energy into the elastic potential energy.
When the spring is released, this elastic potential energy propels it upwards, back into the kinetic form.
Energy Conservation in Elastic Systems
The principle of energy conservation dictates that the total energy in a closed system remains constant. In the context of elastic systems, this means that the sum of potential energy, kinetic energy, and other forms of energy (like heat due to friction) remains the same.
However, friction or air resistance can cause some of the energy to dissipate as heat, leading to a decrease in the overall mechanical energy of the system. In ideal situations, with no energy losses, all of the elastic potential energy will fully transform into kinetic energy.
Force, Displacement, and Elastic Energy: A Closer Look
Force and displacement are fundamental concepts that define the elastic energy phenomena. As we have established, force is the external influence that causes deformation, while displacement is the measure of that deformation.
The amount of elastic energy stored is directly related to both the magnitude of the force applied and the extent of the displacement.
Greater force and displacement generally lead to a higher amount of stored elastic energy, up to the material's elastic limit.
In conclusion, understanding the science behind elastic energy requires grasping the concepts of elastic potential energy, Hooke's Law, and the relationships between force, displacement, and energy conservation. These principles provide the foundation for analyzing and applying elastic energy in various real-world scenarios.
Elasticity in Action: Real-World Examples You Can See and Feel
The abstract world of physics often finds its most compelling voice in the tangible reality around us. Elastic energy, a concept seemingly confined to equations, is constantly at play in everyday scenarios, from the mundane to the exhilarating. Let's explore some common examples where elastic energy manifests, examining the principles at work and the materials that make it all possible.
Springs: The Quintessential Elastic Element
Springs are arguably the most recognizable embodiment of elastic energy storage. Their ability to deform under load and return to their original shape makes them indispensable in countless applications. Different designs cater to specific needs, each harnessing elastic potential energy in a unique way.
Coil Springs: Versatility in Action
Coil springs, characterized by their helical shape, are ubiquitous due to their versatility. When compressed or extended, the material of the spring twists, storing elastic potential energy.
This energy is then released as the spring returns to its original length. Car suspensions, for example, use coil springs to absorb shocks, providing a smoother ride. Mechanical watches utilize the controlled release of energy from a tightly wound coil spring to power their intricate mechanisms. The playful pogo stick relies on a robust coil spring to convert the rider’s downward force into upward momentum, enabling the bouncing motion.
Leaf Springs: Distributing the Load
Leaf springs, commonly found in vehicle suspensions, consist of multiple layers of metal stacked on top of each other. This design allows them to distribute the load over a larger area, making them ideal for heavy-duty applications.
The bending of the leaves stores elastic potential energy, which is then released to absorb shocks and maintain stability.
Torsion Springs: Twisting Forces
Torsion springs, unlike coil springs that compress or extend, resist twisting forces. When twisted, the material of the spring experiences shear stress, storing elastic potential energy.
This energy is then released as the spring unwinds. Examples include clothespins, where torsion springs provide the clamping force, and vehicle suspension systems that control body roll.
Rubber Bands: Simplicity and Elasticity
Rubber bands, seemingly simple objects, are excellent examples of elastic energy storage. Made from polymers with remarkable elasticity, rubber bands can be stretched significantly and still return to their original shape.
Stretching a rubber band increases the orderliness of polymer chains, thereby storing potential energy. Releasing the tension allows these chains to relax, converting potential energy back into kinetic energy. This simple principle powers countless applications, from securing everyday objects to propelling simple toys.
Trampolines: A Symphony of Springs and Fabric
Trampolines brilliantly demonstrate the combined action of springs and elastic fabric to create a bouncing surface. When a person jumps onto a trampoline, the springs extend, storing elastic potential energy.
Simultaneously, the fabric stretches, also storing elastic energy. As the springs contract and the fabric recoils, the stored energy is transferred back into kinetic energy, launching the person upwards. The materials used, typically high-tensile steel for the springs and woven polypropylene for the fabric, are chosen for their ability to withstand repeated deformation and high stress.
Bungee Jumping: An Extreme Test of Elasticity
Bungee jumping takes elastic energy to the extreme. A long, highly elastic cord is attached to the jumper, allowing for a dramatic freefall followed by a series of rebounds. The elastic cord is the heart of the system, designed to stretch significantly without exceeding its elastic limit.
As the jumper falls, the cord stretches, converting kinetic energy into elastic potential energy. At the lowest point, the cord's elasticity pulls the jumper back up, converting the stored elastic potential energy back into kinetic energy. This continuous conversion results in the characteristic bouncing motion until air resistance and internal friction dissipate the energy.
Archery: Precision and Elastic Energy
Archery beautifully illustrates the controlled release of elastic potential energy. The bow, typically made from fiberglass, carbon fiber, or wood laminates, stores elastic potential energy when drawn.
As the archer pulls back the string, the limbs of the bow bend, storing energy. Upon release, the limbs snap back to their original shape, transferring the stored elastic potential energy to the arrow, propelling it forward with significant force. The efficiency of this energy transfer depends on the bow's design, the string's tension, and the archer's technique.
Pushing the Limits: Factors That Influence Elastic Energy Storage
The ability to harness elastic energy isn't simply about having a stretchy material. Several factors dictate just how much energy a material can actually store and release. Material properties play a crucial role, as does understanding the boundaries of deformation a material can withstand before undergoing permanent change.
These limitations are not arbitrary; they're governed by the material's inherent structure and its response to applied forces. Let's delve into these critical aspects to gain a deeper appreciation of elastic energy storage.
Material Properties: The Elasticity and Resilience Connection
The capacity of a material to store elastic energy hinges significantly on its elasticity and resilience. Elasticity refers to a material's ability to return to its original shape after deformation. Resilience, on the other hand, quantifies the amount of energy a material can absorb without undergoing permanent deformation.
The Role of Material Composition
The microscopic structure of a material dictates its elastic behavior. Polymers, for example, consist of long, chain-like molecules that can stretch and recoil.
Metals, with their crystalline structures, rely on the shifting of atomic layers to store energy. The arrangement and bonding strength of these constituents greatly influence the material's ability to store elastic energy efficiently.
Comparing Elastic Properties: A Material Spectrum
Different materials exhibit varying degrees of elasticity. Steel, known for its high elastic modulus, can store significant amounts of energy before deforming permanently. Rubber, with its flexible polymer chains, can undergo large deformations and still return to its original shape, albeit storing less energy than steel for a similar volume.
Comparing materials requires considering both their elastic modulus (stiffness) and their yield strength (the point at which permanent deformation begins). This comparison allows engineers to select materials optimized for specific elastic energy applications.
Deformation Limits: The Point of No Return
Every elastic material has a limit to how much it can be stretched, compressed, or twisted before it undergoes permanent damage. Understanding these deformation limits is crucial to avoid material failure and ensure the reliable performance of elastic systems.
Elastic vs. Plastic Deformation: A Tale of Two Behaviors
Elastic deformation is reversible. When the applied force is removed, the material returns to its original form. Plastic deformation, conversely, results in a permanent change in shape. The material's internal structure is altered to the point where it cannot fully recover.
Think of bending a paperclip. A slight bend might be elastic, and the paperclip springs back. But, if you bend it too far, it stays bent – that's plastic deformation.
Consequences of Exceeding the Elastic Limit
Exceeding the elastic limit can lead to a cascade of problems. The material may weaken, develop cracks, or even fracture completely. In engineered systems, this can result in catastrophic failure, rendering the system unusable and potentially causing harm.
Therefore, careful consideration of the material's elastic limit is paramount in design. Engineers must factor in safety margins and anticipate potential overloads to prevent irreversible damage and ensure the longevity and reliability of elastic components.
Pushing materials to their limits reveals the intricacies of elastic energy storage, but understanding those limits is only half the battle. The true power of this knowledge lies in its application. How can we harness the potential of elastic energy to shape technology and improve our world?
Elastic Energy in Action: Technological and Engineering Applications
The principles of elastic energy aren't confined to theoretical physics; they're actively shaping innovations across various technological and engineering fields. From developing cutting-edge energy storage solutions to enhancing safety and comfort through advanced shock absorption, elastic energy plays a pivotal role. Let's examine some key applications.
Energy Storage Systems: A Sustainable Alternative?
The quest for sustainable energy solutions has led researchers to explore novel methods of energy storage. Elastic energy storage systems (EESS) present a compelling alternative to traditional batteries and other energy storage technologies. EESS typically involves mechanically deforming elastic materials, like springs or specialized polymers, to store energy. The energy is then released when the material returns to its original shape.
This approach holds significant promise for several reasons:
- Longevity: Unlike batteries that degrade over time, EESS components can potentially withstand numerous charge-discharge cycles with minimal performance loss.
- Environmental Friendliness: EESS can be constructed from relatively benign materials, reducing environmental concerns associated with battery disposal and manufacturing.
- Rapid Response: Elastic energy can be released very quickly, making EESS suitable for applications requiring bursts of power.
Research and Development Efforts
Significant research and development efforts are underway to improve the efficiency, energy density, and scalability of EESS. Scientists are exploring new materials with enhanced elasticity and resilience, as well as innovative mechanical designs to optimize energy storage capacity.
Flywheel energy storage, which stores energy in a rotating mass, is a form of elastic energy storage that has seen commercial applications. Advanced composite materials and magnetic bearings are enabling flywheels to achieve higher rotational speeds and store more energy.
Compressed air energy storage (CAES) also relies on elasticity. CAES systems store energy by compressing air and releasing it to drive turbines when power is needed. While geographically constrained, CAES offers a scalable solution for grid-level energy storage.
Advantages and Disadvantages Compared to Other Methods
EESS presents several advantages over other energy storage methods, but it also has its drawbacks:
Advantages:
- High power density
- Long lifespan
- Environmentally friendly materials
- Rapid charge/discharge rates
Disadvantages:
- Lower energy density compared to batteries
- Potential for mechanical wear and tear
- Size and weight considerations
While the energy density of EESS is currently lower than that of batteries, ongoing research is focused on improving this aspect. The longevity and environmental benefits of EESS make it a viable option for specific applications, particularly those where high power output and long cycle life are paramount.
Shock Absorption: Minimizing Impact Forces
Elastic energy is also crucial in shock absorption systems, which are designed to mitigate the effects of sudden impacts and vibrations. These systems rely on the ability of elastic materials to deform under stress, absorb kinetic energy, and then release it gradually, thereby reducing the force transmitted to the object being protected.
Vehicle Suspensions
Vehicle suspensions are a prime example of shock absorption in action. Springs and dampers work together to absorb the energy from bumps and uneven road surfaces, providing a smoother and more comfortable ride. The springs compress and extend, storing and releasing elastic energy, while the dampers dissipate energy as heat, preventing excessive bouncing.
Sports Equipment
Shock absorption is also vital in sports equipment, where it helps to protect athletes from injuries. Running shoes incorporate cushioning materials that compress upon impact, reducing the stress on joints and muscles. Helmets utilize impact-absorbing foam that deforms to cushion the head during collisions.
Converting Kinetic Energy
The key to effective shock absorption lies in converting kinetic energy into other forms of energy, such as heat or sound, or storing and releasing it over a longer period. By dissipating or redistributing the energy from an impact, shock absorbers minimize the peak forces experienced by the protected object, thereby reducing the risk of damage or injury. Damping is achieved through friction (e.g., in a car shock absorber) or through viscoelastic materials.
The application of elastic energy in shock absorption is widespread and essential for enhancing safety, comfort, and performance in various industries, ranging from transportation to sports. As materials science and engineering continue to advance, we can expect even more sophisticated and effective shock absorption systems to emerge, further minimizing the impact of forces on our bodies and equipment.
Video: Unlock Elastic Energy: The Ultimate Guide You Need to Read!
FAQs: Understanding Elastic Energy
Hopefully, this guide has helped you unlock the potential of elastic energy. Here are some common questions to clarify a few key points.
What exactly is elastic energy?
Elastic energy is potential energy stored in an object when it's deformed elastically, meaning it returns to its original shape once the deforming force is removed. Think of a stretched rubber band or a compressed spring.
How is elastic energy different from kinetic energy?
Kinetic energy is the energy of motion. A moving car has kinetic energy. Elastic energy, however, is stored energy waiting to be released, related to an object's deformation, not its movement. When the rubber band is released, that elastic energy is transformed into kinetic energy.
Can elastic energy be used for practical applications?
Absolutely! It's utilized in many ways, from simple springs in mechanical devices to advanced materials designed for energy storage. Think of trampolines or the suspension system in your car. Researchers are constantly exploring new ways to harness and optimize elastic energy for greater efficiency.
What factors influence the amount of elastic energy stored?
The amount of elastic energy stored depends on the material's properties (elasticity), the extent of the deformation (how much it's stretched or compressed), and the geometry of the object. More elastic material or greater deformation results in more stored elastic energy.