Temperature Approach: Master It Now For Ultimate Success!
The success of process optimization, a key attribute of Lean Manufacturing, often hinges on accurate control of thermal dynamics. This makes the Temperature Control Loop, a fundamental component of industrial automation, critically important. Understanding the temperature approach, therefore, empowers process engineers to improve efficiency and product quality. Furthermore, incorporating best practices outlined by organizations like the ISA (International Society of Automation), leads to enhanced system performance. As a result, mastering the temperature approach is pivotal for ultimate success in many areas.
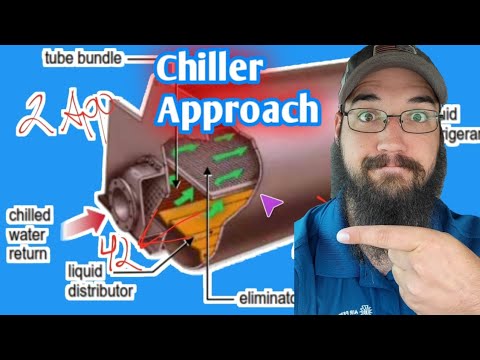
Image taken from the YouTube channel HVACTIME , from the video titled HVAC Chiller Approach Explained .
Temperature. We experience it daily, from the warmth of the sun to the chill of a winter breeze. But beyond a simple sensory perception, temperature represents a fundamental force that, when understood and strategically managed, unlocks a world of possibilities. This is where the "temperature approach" comes into play.
It's more than just knowing whether something is hot or cold. It’s a comprehensive methodology for understanding, controlling, and leveraging temperature to achieve specific, desired outcomes across a multitude of disciplines.
Defining the Temperature Approach
At its core, the temperature approach is a strategic framework.
It involves analyzing the thermal properties of a system, identifying the optimal temperature range for a given process or outcome, and implementing strategies to maintain or manipulate temperature accordingly.
This approach recognizes temperature not as a static condition, but as a dynamic variable that can be actively managed for maximum benefit.
The Ubiquitous Importance of Temperature Management
The significance of the temperature approach reverberates across a vast spectrum of fields.
Consider the realm of medicine, where precise temperature control is crucial for preserving organs for transplant, storing vaccines, and even performing delicate surgeries.
In the food industry, temperature dictates not only safety but also flavor and texture, influencing everything from the fermentation of yogurt to the perfect sear on a steak.
Manufacturing processes rely heavily on thermal management to ensure material integrity, optimize reaction rates, and achieve consistent product quality.
From the intricate workings of microchips to the expansive reach of climate science, temperature plays a pivotal role in shaping our world.
Navigating This Exploration: Scope and Objectives
This article will serve as your guide to understanding and implementing the temperature approach.
We will delve into the fundamental principles that govern temperature, exploring the tools and technologies used to measure and control it, and showcasing real-world examples of its successful application.
Our objective is to empower you with the knowledge and insights necessary to harness the power of temperature in your own endeavors, fostering efficiency, safety, and innovation along the way.
By the end, you'll not only understand what the temperature approach is, but how and why it's so critical to success in an increasingly complex and interconnected world.
Fundamentals of Temperature: A Thermodynamic Perspective
The ability to manage temperature effectively hinges on a solid grasp of its underlying principles. We move now from considering the broad applicability of the temperature approach to dissecting the science that makes it all possible. At its heart, temperature is a thermodynamic property, deeply intertwined with concepts like heat, energy, and entropy.
Thermodynamics: The Foundation of Temperature
Thermodynamics provides the very definition of temperature. In essence, temperature is a measure of the average kinetic energy of the particles (atoms or molecules) within a system. The more vigorously these particles move, the higher the temperature.
It's crucial to understand that thermodynamics isn't just about heat and cold; it's about the flow of energy. The Laws of Thermodynamics dictate how energy is transferred and transformed, and these laws govern all temperature-related phenomena.
Heat Transfer: The Engine of Change
Temperature differentials drive heat transfer, the process by which thermal energy moves from one place to another. There are three primary modes of heat transfer:
-
Conduction: This occurs through direct contact, as energy is passed from one molecule to another. Think of a metal spoon heating up when placed in a hot cup of coffee.
-
Convection: This involves the movement of fluids (liquids or gases). Warm air rising and cool air sinking is a classic example of convection.
-
Radiation: This is the transfer of energy through electromagnetic waves, such as the heat you feel from the sun.
Understanding these mechanisms is crucial because controlling heat transfer is often the key to controlling temperature. Insulation, for instance, minimizes heat transfer, while heat sinks maximize it.
Equilibrium: The State of Balance
Thermal equilibrium is a state where there is no net flow of heat between two or more systems. In other words, they have reached the same temperature. Understanding equilibrium is vital for predicting how systems will behave and for designing effective temperature control strategies.
For example, when a hot object is placed in a cooler environment, heat will flow from the object to the environment until they both reach the same temperature – equilibrium. This principle is used in many applications, from designing efficient refrigerators to understanding climate change.
Cooling and Heating: Manipulating Thermal Energy
The practical application of the temperature approach depends on our ability to heat and cool things effectively. Heating involves adding energy to a system, increasing the kinetic energy of its particles. Cooling, conversely, involves removing energy, reducing that kinetic energy.
Heating Methods
Heating methods are diverse, ranging from simple combustion to sophisticated electrical resistance heating. The choice of method depends on factors such as efficiency, cost, and the specific requirements of the application.
Cooling Methods
Cooling methods are equally varied. Refrigeration cycles use the evaporation and condensation of fluids to remove heat. Heat exchangers transfer heat from one fluid to another. The selection hinges on similar considerations as heating.
The Imperative of Accurate Measurement
Underlying all of this is the need for accurate temperature measurement. Without precise measurements, it's impossible to effectively control or manage temperature. Inaccurate readings can lead to inefficiencies, errors, and even dangerous situations.
Therefore, understanding the principles of temperature measurement and using appropriate instruments are essential components of the temperature approach.
Temperature Scales and Measurement Tools: A Practical Guide
Having established the fundamental link between temperature and thermodynamics, we now turn our attention to the practical tools and scales that enable us to quantify and control this crucial property. Understanding the different temperature scales and the instruments used to measure temperature is essential for anyone seeking to apply the “temperature approach” effectively.
Understanding Temperature Scales: Celsius, Fahrenheit, and Kelvin
Temperature isn’t a directly observable quantity. It's inferred by observing changes in other physical properties, such as the expansion of a liquid or the electrical resistance of a material. Different temperature scales provide different frameworks for interpreting these changes.
Each scale has its advantages and is suited for different applications. The most common scales are Celsius (°C), Fahrenheit (°F), and Kelvin (K).
Degrees Celsius (°C): A Scale Rooted in Water
The Celsius scale, also known as the centigrade scale, is widely used around the world, particularly in scientific contexts. Its defining feature is that 0°C is defined as the freezing point of water, and 100°C is defined as the boiling point of water at standard atmospheric pressure.
This decimal-based system makes it intuitive for many calculations and everyday applications.
Degrees Fahrenheit (°F): A Scale with Historical Roots
The Fahrenheit scale is primarily used in the United States. It defines the freezing point of water as 32°F and the boiling point as 212°F.
The origins of the Fahrenheit scale are less intuitive than Celsius, as its zero point was originally based on the freezing point of a brine solution.
Kelvin (K): The Absolute Temperature Scale
The Kelvin scale is the absolute thermodynamic temperature scale. Its zero point, 0 K, represents absolute zero, the theoretical point at which all molecular motion ceases.
One Kelvin is equal in size to one degree Celsius, but the Kelvin scale is offset so that 0°C is equal to 273.15 K.
The Kelvin scale is crucial in scientific and engineering applications where absolute temperature values are required, such as in thermodynamic calculations.
Navigating Conversions Between Temperature Scales
Being able to convert between temperature scales is a fundamental skill. Here are the key conversion formulas:
- Celsius to Fahrenheit: °F = (°C × 9/5) + 32
- Fahrenheit to Celsius: °C = (°F - 32) × 5/9
- Celsius to Kelvin: K = °C + 273.15
- Kelvin to Celsius: °C = K - 273.15
- Fahrenheit to Kelvin: K = (°F + 459.67) × 5/9
- Kelvin to Fahrenheit: °F = (K × 9/5) - 459.67
These conversions are essential for interpreting data from different sources and ensuring consistency in calculations.
Thermometers: Measuring Temperature Directly
Thermometers are instruments used to measure temperature. They rely on the principle that certain physical properties change predictably with temperature.
There are various types of thermometers, each with its own advantages and limitations:
Liquid-in-Glass Thermometers
These thermometers, often using mercury or alcohol, rely on the expansion of a liquid within a glass tube. As the temperature increases, the liquid expands, and the level rises, indicating the temperature on a calibrated scale.
They are simple, inexpensive, and relatively accurate for many applications.
Bimetallic Strip Thermometers
These thermometers use a strip made of two different metals with different thermal expansion coefficients. When the temperature changes, the metals expand at different rates, causing the strip to bend. This bending motion is then linked to a pointer on a dial, indicating the temperature.
They are robust and often used in ovens and other high-temperature applications.
Resistance Thermometers (RTDs) and Thermistors
These thermometers utilize the change in electrical resistance of a material with temperature. RTDs use metals, while thermistors use semiconductors. They offer high accuracy and are often used in industrial and scientific applications.
Thermocouples
Thermocouples consist of two dissimilar metals joined at a junction. When the junction is heated or cooled, a voltage is produced that is proportional to the temperature difference between the junction and a reference point.
Thermocouples are versatile and can measure a wide range of temperatures, making them suitable for various industrial processes.
Infrared Thermometers
These thermometers measure temperature by detecting the infrared radiation emitted by an object. They do not need to be in direct contact with the object, making them ideal for measuring the temperature of moving or hazardous objects.
Thermostats: Maintaining Temperature Automatically
Thermostats are control devices that maintain a desired temperature automatically. They work by sensing the temperature and then activating heating or cooling systems as needed.
Mechanical Thermostats
These thermostats typically use a bimetallic strip to sense temperature changes. The bending of the strip activates a switch that turns the heating or cooling system on or off.
Electronic Thermostats
These thermostats use electronic sensors, such as thermistors, to measure temperature. They offer greater accuracy and control compared to mechanical thermostats.
Programmable thermostats allow users to set different temperature schedules for different times of the day, optimizing energy efficiency and comfort.
In conclusion, a thorough understanding of temperature scales and measurement tools is paramount for effectively applying the "temperature approach" across diverse fields. By mastering these fundamental concepts, individuals can accurately quantify, control, and manipulate temperature to achieve desired outcomes, whether it's optimizing industrial processes, ensuring product quality, or enhancing energy efficiency.
Having explored the landscape of temperature scales and the instruments used to measure them, it's time to delve into the realm of automated temperature management. This is where sensors and control systems come into play, enabling us to not only monitor temperature with precision, but also to actively adjust it to maintain desired conditions.
Sensors and Control Systems: Automated Temperature Management
At the heart of any effective temperature management strategy lies the ability to accurately measure the current temperature. This is where sensors take center stage.
These devices act as the eyes and ears of the system, providing real-time temperature readings that form the basis for automated adjustments.
The Role of Sensors in Accurate Temperature Measurement
Sensors are the critical interface between the physical environment and the control system. They translate temperature into a signal that can be interpreted and acted upon.
Different types of temperature sensors exist, each with its own strengths and limitations.
Types of Temperature Sensors
-
Thermocouples: These sensors generate a voltage proportional to the temperature difference between two dissimilar metals. They are robust and can operate over a wide temperature range.
-
Resistance Temperature Detectors (RTDs): RTDs measure temperature based on the change in electrical resistance of a metal. They offer high accuracy and stability.
-
Thermistors: Thermistors are semiconductor devices whose resistance changes significantly with temperature. They are highly sensitive but have a limited temperature range.
-
Infrared (IR) Sensors: IR sensors measure temperature by detecting the infrared radiation emitted by an object. They are ideal for non-contact temperature measurement.
The selection of the appropriate sensor depends on the specific application, required accuracy, and operating temperature range. Proper sensor placement is also crucial to ensure representative temperature readings.
How Control Systems Leverage Temperature Data for Automated Adjustments
Once the temperature is measured by a sensor, the data is fed into a control system. The control system acts as the brain, processing the information and making decisions to maintain the desired temperature.
Control System Components
A typical control system consists of:
-
A Sensor: As previously discussed, to measure the temperature.
-
A Controller: This component compares the measured temperature to the desired setpoint and calculates the necessary adjustments.
-
An Actuator: The actuator is the device that implements the adjustments, such as turning on a heater or opening a valve to release coolant.
Control Algorithms
The controller uses a specific control algorithm to determine how to adjust the actuator. Common control algorithms include:
-
On-Off Control: The simplest type of control, where the actuator is either fully on or fully off.
-
Proportional (P) Control: The actuator output is proportional to the difference between the measured temperature and the setpoint.
-
Proportional-Integral (PI) Control: This algorithm combines proportional control with an integral term to eliminate steady-state errors.
-
Proportional-Integral-Derivative (PID) Control: The most advanced type of control, PID control uses proportional, integral, and derivative terms to achieve optimal performance.
The choice of control algorithm depends on the specific requirements of the application, such as the desired accuracy, response time, and stability.
The Synergy Between Sensors and Control Systems
The true power of automated temperature management lies in the synergy between sensors and control systems. Sensors provide the necessary data, and control systems use that data to make intelligent adjustments.
This closed-loop feedback system allows for precise and responsive temperature control, maintaining desired conditions even in the face of disturbances or changing environmental conditions. The result is improved efficiency, reduced energy consumption, and enhanced product quality.
Having explored the landscape of temperature scales and the instruments used to measure them, it's time to delve into the realm of automated temperature management. This is where sensors and control systems come into play, enabling us to not only monitor temperature with precision, but also to actively adjust it to maintain desired conditions.
Real-World Applications: Temperature Control in Action
The "temperature approach," as a strategic methodology, finds its true validation in the myriad of real-world applications across diverse industries. From optimizing manufacturing processes to ensuring the safety and efficacy of pharmaceuticals, the ability to precisely control and manage temperature is paramount.
This section will showcase practical examples of how the thoughtful application of temperature principles can lead to significant improvements in efficiency, quality, and overall performance.
Industrial Processes: Optimizing Efficiency and Quality
In industrial settings, temperature control is not merely a matter of comfort; it is often a critical factor determining the success or failure of a manufacturing process. Consider, for example, the production of semiconductors.
The creation of these intricate electronic components requires precise temperature management at every stage. From crystal growth to etching and deposition, even slight deviations from the ideal temperature can lead to defects, reduced performance, and ultimately, wasted resources.
Advanced temperature control systems are employed to maintain uniformity and stability throughout the manufacturing process, ensuring that each semiconductor meets the required specifications. This level of precision translates directly into higher yields, reduced scrap rates, and improved product reliability.
Similarly, in the metals industry, heat treatment processes like annealing, quenching, and tempering rely heavily on accurate temperature control to achieve desired material properties. The mechanical strength, hardness, and ductility of metals can be significantly altered by varying the temperature and duration of these treatments.
By implementing sophisticated temperature control strategies, manufacturers can tailor the properties of their materials to meet specific application requirements, leading to stronger, more durable, and more reliable products.
Beyond Manufacturing: Temperature Control in Diverse Industries
The importance of temperature control extends far beyond the confines of manufacturing. In the food processing industry, for example, precise temperature management is essential for ensuring food safety, preserving quality, and extending shelf life.
From pasteurization and sterilization to refrigeration and freezing, temperature control plays a critical role in preventing the growth of harmful bacteria, preserving nutrients, and maintaining the desired texture and flavor of food products.
The Chilling Facts of Food Safety
Inadequate temperature control can lead to spoilage, contamination, and potentially life-threatening foodborne illnesses. Therefore, food processors must adhere to strict temperature regulations and implement robust monitoring systems to ensure the safety of their products.
Pharmaceuticals: Maintaining Potency and Purity
The pharmaceutical industry is another area where temperature control is of utmost importance. Many drugs and vaccines are highly sensitive to temperature fluctuations, and exposure to extreme temperatures can degrade their potency, alter their chemical composition, or even render them completely ineffective.
To ensure the safety and efficacy of pharmaceutical products, manufacturers must maintain strict temperature control throughout the entire supply chain, from production and storage to transportation and distribution.
This often involves the use of specialized packaging, refrigerated vehicles, and temperature monitoring devices to prevent exposure to adverse conditions. Failure to maintain proper temperature control can have serious consequences, including reduced therapeutic efficacy, adverse side effects, and even product recalls.
Agriculture: Cultivating Optimal Growth
Even in agriculture, the "temperature approach" holds considerable sway. Greenhouses utilize climate control systems to regulate temperature, humidity, and light levels, creating an optimal environment for plant growth.
This allows growers to extend the growing season, increase yields, and produce crops in areas where they would not normally thrive. Precise temperature control can also help to prevent diseases and pests, reducing the need for pesticides and other harmful chemicals.
By carefully managing temperature, farmers can improve the quality and quantity of their crops, leading to increased profitability and a more sustainable agricultural system.
Having explored the landscape of temperature scales and the instruments used to measure them, it's time to delve into the realm of automated temperature management. This is where sensors and control systems come into play, enabling us to not only monitor temperature with precision, but also to actively adjust it to maintain desired conditions. The "temperature approach," as a strategic methodology, finds its true validation in the myriad of real-world applications across diverse industries. From optimizing manufacturing processes to ensuring the safety and efficacy of pharmaceuticals, the ability to precisely control and manage temperature is paramount. This section will showcase practical examples of how the thoughtful application of temperature principles can lead to significant improvements in efficiency, quality, and overall performance. Similarly, in the metals industry, heat treatment processes rely on precise temperature cycles to achieve desired material properties. But before we can confidently implement any of these advanced control strategies, it's imperative that we first establish and uphold the accuracy of our measurement tools. This brings us to the critical, yet often overlooked, aspects of calibration and maintenance.
Calibration and Maintenance: Ensuring Accuracy and Reliability
In the pursuit of precise temperature management, calibration and maintenance are not mere afterthoughts; they are the cornerstones upon which accuracy and reliability are built. Neglecting these crucial aspects can lead to significant errors, with potentially costly and even dangerous consequences.
The Paramount Importance of Calibration
Calibration is the process of comparing the readings of a temperature-sensitive instrument against a known standard. This verifies that the instrument is providing accurate measurements.
Why is this so critical? Because over time, even the most sophisticated equipment can drift from its original calibration due to factors like wear and tear, environmental conditions, and general usage.
Without regular calibration, you simply cannot be certain that the temperature readings you're relying on are trustworthy. Imagine a scenario in pharmaceutical manufacturing where a sterilizer is believed to be operating at 121°C, but is actually only reaching 115°C due to calibration drift.
The result could be inadequately sterilized products, posing a serious risk to public health. Calibration is your assurance of accuracy.
Best Practices for Maintaining Temperature-Sensitive Equipment
Maintaining temperature-sensitive equipment goes hand-in-hand with calibration. Good maintenance practices not only extend the lifespan of your instruments, but also help to prevent calibration drift in the first place.
Regular Cleaning and Inspection
Dust, dirt, and other contaminants can interfere with the performance of temperature sensors and probes. Regularly clean your equipment according to the manufacturer's instructions.
Inspect sensors for any signs of physical damage, such as cracks, corrosion, or loose connections. Address any issues promptly.
Proper Storage
When not in use, store temperature-sensitive equipment in a clean, dry environment. Avoid extreme temperatures or humidity, as these can accelerate degradation.
Use protective cases or covers to shield instruments from physical damage and contamination.
Scheduled Maintenance
Adhere to the manufacturer's recommended maintenance schedule for each piece of equipment. This may include tasks such as replacing worn parts, lubricating moving components, and verifying sensor integrity.
Keep detailed records of all maintenance activities. This helps to track the performance of your equipment over time and identify potential problems before they escalate.
Environmental Considerations
Be mindful of the environment in which your temperature-sensitive equipment is used. Factors such as ambient temperature, humidity, and vibration can all affect accuracy and reliability.
Take steps to mitigate these environmental influences. For example, you might use insulated probes to minimize the impact of ambient temperature fluctuations, or mount equipment on vibration-dampening platforms.
Training and Competency
Ensure that personnel who use and maintain temperature-sensitive equipment are properly trained and competent. They should understand the principles of temperature measurement, the importance of calibration, and the proper procedures for handling and caring for the instruments.
Consequences of Neglecting Calibration and Maintenance
The consequences of neglecting calibration and maintenance can be far-reaching. Inaccurate temperature readings can lead to:
- Compromised product quality: In manufacturing, deviations from the ideal temperature can result in defects, reduced performance, and product recalls.
- Inefficient processes: Inaccurate temperature control can waste energy, increase production time, and reduce throughput.
- Safety hazards: In industries such as food processing and pharmaceuticals, improper temperature management can lead to the growth of harmful bacteria or the degradation of critical ingredients.
- Regulatory non-compliance: Many industries are subject to strict regulations regarding temperature control. Failure to meet these regulations can result in fines, penalties, and even legal action.
By prioritizing calibration and maintenance, you are safeguarding the accuracy of your temperature measurements, protecting the integrity of your processes, and mitigating potential risks.
Video: Temperature Approach: Master It Now For Ultimate Success!
Mastering Temperature Approach: Your FAQs Answered
The temperature approach can seem tricky, but understanding these key points can significantly boost your success. Here are some frequently asked questions.
What exactly is the temperature approach in this context?
The temperature approach involves carefully assessing and managing the "temperature" of a situation, a person's emotional state, or a project's progress. It's about being aware of subtle cues and adjusting your strategy accordingly.
How does understanding the temperature approach lead to greater success?
By accurately gauging the situation's "temperature," you can anticipate potential problems, tailor your communication, and make informed decisions. Mastering the temperature approach allows you to navigate complex situations more effectively.
What are some key indicators to look for when using the temperature approach?
Look for non-verbal cues like body language and tone of voice. Also, pay attention to project timelines, resource availability, and any conflicts that might arise. These factors can influence the overall "temperature."
Why is adjusting my strategy important when using the temperature approach?
If the "temperature" is rising (e.g., stress levels are high), a direct, confrontational approach might be counterproductive. Adjusting your strategy to a more collaborative or understanding approach can often diffuse tension and achieve a more positive outcome using the temperature approach method.
So, go ahead and put these ideas about the temperature approach into practice! You might be surprised at the difference it makes. Good luck, and here's to your ultimate success!