SS Abbreviation: Decoding Stainless Steel & Uses

The ubiquitous material known for its corrosion resistance, stainless steel, often appears with a simple two-letter designation. The American Iron and Steel Institute (AISI), a leading organization in the steel industry, recognizes various grades of stainless steel, each defined by its unique composition and properties. The abbreviation for stainless steel, commonly "SS," simplifies referencing this versatile alloy in technical documents and everyday communication. Industries employing Computer-Aided Design (CAD) software frequently use "SS" when specifying material types in their designs.
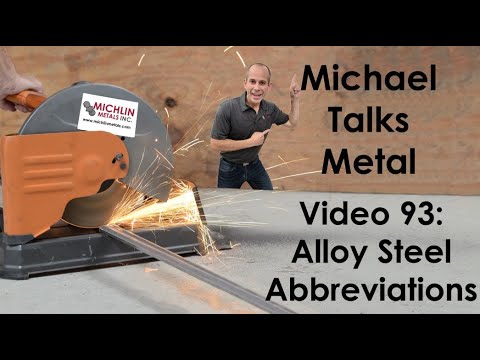
Image taken from the YouTube channel Michlin Metals Inc , from the video titled Metal and Steel Abbreviations - Vocabulary - What Do These Steel Words mean? .
Stainless steel stands as a cornerstone material in modern engineering and manufacturing. Its defining attribute, exceptional corrosion resistance, distinguishes it from ordinary steel.
This key property makes it suitable for a vast array of applications across diverse industries. From the mundane to the highly specialized, stainless steel's presence is pervasive.
Its ubiquity stems not only from its durability, but also from its hygienic qualities and aesthetic appeal. These characteristics collectively contribute to its widespread adoption in both consumer and industrial settings.
Defining Stainless Steel
At its core, stainless steel is an iron-based alloy. Its composition is carefully tailored to achieve specific properties.
What sets it apart is the inclusion of chromium, typically at a minimum of 10.5% by weight. This seemingly small addition is the magic ingredient, imbuing the alloy with its remarkable resistance to corrosion.
Without chromium, the iron in steel readily reacts with oxygen and moisture, leading to rust. The presence of chromium mitigates this process significantly, resulting in a material with extended lifespan.
The Widespread Prevalence of Stainless Steel
Stainless steel's robustness translates directly to longevity in service. Components made from stainless steel can withstand harsh environments.
Its resistance to corrosion is not merely a convenience; it's a critical factor in applications where reliability and safety are paramount. Consider the chemical processing industry, where exposure to corrosive substances is constant.
Likewise, in the food and beverage sector, the material's resistance to bacteria growth and ease of cleaning make it ideal for maintaining sanitary conditions. The same is true in medical applications, where sterilization is vital.
Beyond its functional attributes, stainless steel offers aesthetic advantages. Its sleek, modern appearance makes it a popular choice for architectural elements, appliances, and decorative items.

A Brief History of Development and Standardization
The story of stainless steel begins in the early 20th century with the discovery of chromium's passivating effect on iron. This was a watershed moment.
Researchers and metallurgists quickly recognized the potential of this new alloy. The race to develop commercially viable stainless steel grades was underway.
Over time, various formulations were created, each tailored to specific applications and performance requirements. As the industry matured, standardization became necessary to ensure consistency and quality.
Organizations such as the American Iron and Steel Institute (AISI) stepped in to create grading systems that could be used to classify the different types of stainless steel.
The Role of AISI in Steel Grade Designation
The American Iron and Steel Institute (AISI) played a pivotal role in establishing a standardized system for identifying different stainless steel grades. The AISI system assigns a three-digit number (often with letter suffixes) to each grade.
These designations provide a concise way to communicate the alloy's composition and properties. This allows engineers and manufacturers to select the appropriate material for their specific needs.
While AISI no longer actively maintains this system, its legacy endures. The designations continue to be widely used as a convenient shorthand for identifying stainless steel alloys.
The Recipe: Composition and Alloying Elements in Stainless Steel
Stainless steel stands as a cornerstone material in modern engineering and manufacturing. Its defining attribute, exceptional corrosion resistance, distinguishes it from ordinary steel.
This key property makes it suitable for a vast array of applications across diverse industries. From the mundane to the highly specialized, stainless steel's presence is undeniable. But what exactly gives stainless steel its remarkable characteristics? The answer lies in its intricate composition and the strategic addition of alloying elements.
The Heart of Corrosion Resistance: Chromium (Cr)
At its core, stainless steel is an iron-based alloy with a minimum of 10.5% chromium by mass. This seemingly small addition transforms the properties of iron dramatically.
Chromium is the key ingredient that imbues stainless steel with its corrosion resistance. Without it, the alloy would be susceptible to rust and degradation like any other ferrous metal.
Passivation: Chromium's Protective Shield
The magic of chromium lies in its ability to undergo passivation. When exposed to oxygen, chromium atoms on the surface of the steel react to form a thin, adherent, and invisible layer of chromium oxide (Cr₂O₃).
This oxide layer acts as a protective barrier, preventing further oxidation of the iron below. If the layer is damaged, it quickly self-repairs in the presence of oxygen, ensuring continuous protection.
This self-healing capability is what makes stainless steel so durable and long-lasting in corrosive environments. The higher the chromium content, the more robust the passivation layer and the greater the resistance to corrosion.
Beyond Chromium: The Supporting Cast of Alloying Elements
While chromium is the star of the show, other alloying elements play crucial supporting roles, further enhancing the properties of stainless steel. Each element contributes unique characteristics that tailor the alloy for specific applications.
Nickel (Ni): Enhancing Toughness and Formability
Nickel is a common addition to austenitic stainless steels. It significantly improves the alloy's toughness, ductility, and corrosion resistance.
Nickel stabilizes the austenitic crystal structure, which provides superior formability and weldability. It also enhances resistance to corrosion in reducing environments.
Molybdenum (Mo): Fortifying Against Pitting and Crevice Corrosion
Molybdenum is particularly effective in enhancing resistance to localized corrosion, such as pitting and crevice corrosion.
These types of corrosion are especially problematic in chloride-rich environments, such as seawater or industrial processing plants. Molybdenum additions make stainless steel more resilient in these harsh conditions.
Titanium (Ti): Stabilizing Against Sensitization
Titanium is added to some stainless steel grades to prevent sensitization. Sensitization is a phenomenon that can occur during welding or heat treatment, where chromium carbides precipitate at the grain boundaries, depleting the chromium content in those areas and reducing corrosion resistance.
Titanium acts as a stabilizer by preferentially reacting with carbon, preventing the formation of chromium carbides and preserving the alloy's corrosion resistance.
Carbon (C): A Balancing Act
Carbon is an unavoidable element in steelmaking. However, its concentration in stainless steel is carefully controlled, typically kept low. High carbon levels can negatively impact weldability and corrosion resistance.
While carbon can increase the strength and hardness of steel, it can also lead to the formation of chromium carbides, especially during welding, which can compromise corrosion resistance.
Therefore, the carbon content is carefully balanced to achieve the desired mechanical properties without sacrificing corrosion resistance.
Alloys: More Than Just a Mixture
The creation of stainless steel highlights a fundamental principle in materials science: the power of alloying. Alloying involves combining two or more metallic elements to create a new material with enhanced or modified properties.
The properties of an alloy are not simply the sum of the properties of its constituent elements. Instead, the interaction between the elements at the atomic level leads to entirely new characteristics.
In the case of stainless steel, the addition of chromium to iron transforms a relatively weak and corrosion-prone metal into a strong, durable, and corrosion-resistant material that has revolutionized countless industries. The careful selection and precise control of alloying elements are essential to unlocking the full potential of stainless steel and tailoring it for a wide range of demanding applications.
stainless steel stands as a cornerstone material in modern engineering and manufacturing. Its defining attribute, exceptional corrosion resistance, distinguishes it from ordinary steel. This key property makes it suitable for a vast array of applications across diverse industries. From kitchenware to chemical processing equipment, its versatility is undeniable. This section will decode the classification system of stainless steel, categorizing different types based on their unique microstructures and properties.
Decoding the Code: Types of Stainless Steel Explained
Understanding the diverse landscape of stainless steel requires delving into its classification. Each type possesses a unique microstructure and set of properties, making it suitable for specific applications. Let's explore the four primary categories: austenitic, ferritic, martensitic, and duplex stainless steels.
Austenitic Stainless Steel: The Workhorse of the Industry
Austenitic stainless steel stands as the most commonly used type, prized for its exceptional corrosion resistance and weldability. These alloys contain high levels of chromium and nickel, contributing to their non-magnetic properties and outstanding formability.
Key Characteristics:
- High Corrosion Resistance: Excellent resistance to a wide range of corrosive environments.
- Excellent Weldability: Readily welded using various techniques.
- Non-Magnetic: Typically non-magnetic in the annealed condition.
- High Formability: Easily formed into complex shapes.
Common Grades:
-
304 Stainless Steel: The most widely used grade, known for its versatility and good corrosion resistance. It finds applications in kitchen equipment, food processing, and architectural panels.
-
316 Stainless Steel: Offers enhanced corrosion resistance, especially against chlorides, making it suitable for marine environments and chemical processing.
Ferritic Stainless Steel: Magnetic and Economical
Ferritic stainless steels are magnetic alloys with good corrosion resistance. However, they generally exhibit lower strength and ductility compared to austenitic grades. They contain chromium but little or no nickel, making them a cost-effective alternative for certain applications.
Key Characteristics:
- Magnetic: Possesses magnetic properties.
- Good Corrosion Resistance: Offers adequate resistance to corrosion in mildly corrosive environments.
- Lower Strength: Generally weaker than austenitic stainless steels.
- Limited Weldability: Requires careful welding techniques.
Common Grades:
- 430 Stainless Steel: A common ferritic grade used in appliance components, automotive trim, and decorative applications due to its moderate corrosion resistance and good formability.
Martensitic Stainless Steel: Hardness Through Heat Treatment
Martensitic stainless steels are heat-treatable alloys that can achieve high hardness and strength. They are magnetic and offer moderate corrosion resistance. The hardening process involves quenching and tempering, allowing for tailored mechanical properties.
Key Characteristics:
- Heat Treatable: Can be hardened through heat treatment.
- Magnetic: Exhibits magnetic properties.
- High Hardness: Capable of achieving high hardness levels.
- Moderate Corrosion Resistance: Offers moderate resistance to corrosion.
Common Grades:
- 410 Stainless Steel: A general-purpose martensitic grade used in cutlery, fasteners, and valve components. Its hardenability makes it suitable for applications requiring wear resistance.
Duplex Stainless Steel: Strength and Corrosion Resistance Combined
Duplex stainless steels possess a mixed microstructure of both austenite and ferrite. This unique combination results in enhanced strength and improved resistance to localized corrosion, such as pitting and crevice corrosion.
Key Characteristics:
- High Strength: Exhibits higher strength compared to austenitic stainless steels.
- Excellent Corrosion Resistance: Offers superior resistance to pitting, crevice corrosion, and stress corrosion cracking.
- Good Weldability: Can be welded with appropriate techniques.
- Moderate Formability: Less formable than austenitic grades.
The balanced properties of duplex stainless steels make them ideal for demanding applications in the chemical, oil and gas, and marine industries, where both strength and corrosion resistance are critical.
By understanding these classifications, engineers and designers can select the most appropriate stainless steel for their specific needs, ensuring optimal performance and longevity in diverse environments.
Strength and Resilience: Key Properties of Stainless Steel
[stainless steel stands as a cornerstone material in modern engineering and manufacturing. Its defining attribute, exceptional corrosion resistance, distinguishes it from ordinary steel. This key property makes it suitable for a vast array of applications across diverse industries. From kitchenware to chemical processing equipment, its versatility i...] rests on a combination of factors, notably its inherent resistance to degradation and robust mechanical properties. These characteristics are paramount in determining its suitability for diverse and demanding applications.
This section examines the essential properties of stainless steel, with a focus on both corrosion resistance and key mechanical attributes. Understanding these properties is critical in appreciating stainless steel’s widespread applicability and its enduring role in engineering solutions.
The Indomitable Shield: Corrosion Resistance
Corrosion resistance is the defining characteristic of stainless steel, setting it apart from conventional carbon steels. This remarkable ability to withstand degradation from environmental factors is primarily attributed to the presence of chromium (Cr).
Chromium, when present in sufficient quantities (typically above 10.5%), forms a passive layer of chromium oxide (Cr2O3) on the surface of the steel. This layer acts as a self-healing barrier, preventing further oxidation and corrosion.
Resistance to Oxidation
Oxidation, commonly known as rusting in iron-based materials, is a major concern in many engineering applications. Stainless steel's chromium oxide layer effectively blocks oxygen from reaching the underlying iron, thus preventing the formation of rust.
This resistance to oxidation is not merely superficial. The self-healing nature of the chromium oxide layer means that if the surface is scratched or damaged, the layer reforms almost immediately, maintaining its protective function.
The Role of Alloying Elements
While chromium is the primary driver of corrosion resistance, other alloying elements can further enhance this property. Molybdenum (Mo), for example, improves resistance to pitting and crevice corrosion, which are localized forms of corrosion that can occur in specific environments.
Nickel (Ni) can also contribute to improved corrosion resistance, particularly in certain acidic or alkaline environments.
Mechanical Fortitude: Key Properties
Beyond its corrosion resistance, stainless steel exhibits a range of mechanical properties that contribute to its overall performance and versatility. These properties include tensile strength, yield strength, hardness, and weldability, each playing a distinct role in determining its suitability for specific applications.
Tensile Strength
Tensile strength measures a material's resistance to being pulled apart. It is defined as the maximum stress that a material can withstand while being stretched or pulled before breaking.
Stainless steel typically exhibits high tensile strength, making it suitable for applications where structural integrity and resistance to deformation are critical.
Yield Strength
Yield strength refers to the amount of stress a material can withstand before it begins to deform permanently. Exceeding the yield strength will result in plastic deformation, meaning the material will not return to its original shape after the stress is removed.
A high yield strength is desirable in applications where dimensional stability and resistance to permanent deformation are essential.
Hardness
Hardness measures a material's resistance to localized plastic deformation, such as indentation or scratching. It is an important property for applications where wear resistance and surface durability are required.
Stainless steel can be heat-treated to increase its hardness, making it suitable for applications where it will be subjected to abrasion or impact.
Weldability
Weldability refers to the ability of a material to be welded without significant loss of its properties. Stainless steel exhibits varying degrees of weldability, depending on its composition and grade.
Austenitic stainless steels, such as 304 and 316, are generally considered to have excellent weldability. This makes them suitable for fabrication processes involving welding, allowing for the creation of complex structures and assemblies.
Lower carbon content is also necessary when selecting a material for welding to prevent carbide precipitation along grain boundaries which can lead to corrosion issues down the line.
Following the Rules: Standards and Organizations Governing Stainless Steel
Stainless steel, despite its seemingly straightforward composition, is a complex material governed by a web of standards and specifications. These regulations ensure consistency in production, performance, and application, giving engineers and manufacturers the confidence to specify the right grade for their needs. Understanding the key organizations and standards is, therefore, essential for anyone working with this versatile alloy.
The Role of AISI in Grade Designation
The American Iron and Steel Institute (AISI) played a significant role in developing a numerical designation system that is widely used to classify different types of stainless steel. This system, while not a strict standard in the legal sense, has become a de facto industry standard for identifying various grades.
The AISI system uses a three-digit number, sometimes with letter suffixes, to denote the alloy's composition and general properties. For example, 304 stainless steel, a ubiquitous grade, is an austenitic stainless steel containing chromium and nickel. The AISI designation allows for quick identification and communication about the material's basic characteristics.
It's important to note that the AISI does not create the actual standards that dictate the precise manufacturing processes or performance requirements. Its role is primarily in providing a common language for identifying and categorizing different stainless steel alloys.
ASTM International: Setting the Benchmarks for Quality
While AISI provides a naming convention, ASTM International (formerly known as the American Society for Testing and Materials) is the organization responsible for developing and publishing the technical standards that define how stainless steel is produced, tested, and used. ASTM standards are incredibly comprehensive.
They cover a wide range of aspects, from the chemical composition and mechanical properties to the acceptable tolerances and testing methods. These standards ensure that stainless steel products meet specific performance criteria and are fit for their intended purpose.
Navigating ASTM Standards for Stainless Steel
ASTM standards are identified by an alphanumeric code, such as ASTM A240 (Standard Specification for Chromium and Chromium-Nickel Stainless Steel Plate, Sheet, and Strip for Pressure Vessels and for General Applications). This code provides a clear reference to the specific requirements for a particular type of stainless steel product.
ASTM standards are living documents. They are regularly reviewed and updated to reflect advancements in technology and changes in industry best practices. This continuous improvement process ensures that ASTM standards remain relevant and effective in maintaining the quality and reliability of stainless steel products.
The Importance of Compliance
Compliance with ASTM standards is often a critical requirement in many industries. Particularly for applications where safety or performance is paramount. Using stainless steel that meets the relevant ASTM standards provides assurance that the material will perform as expected. It also offers a level of legal protection for manufacturers and users.
In conclusion, while the AISI designation provides a convenient way to identify different types of stainless steel, ASTM International sets the detailed technical benchmarks that govern its production and application. Understanding both systems is essential for selecting the right material and ensuring its reliable performance in demanding environments.
From Kitchen to Construction: Applications of Stainless Steel Across Industries
Stainless steel, despite its seemingly straightforward composition, is a complex material governed by a web of standards and specifications. These regulations ensure consistency in production, performance, and application, giving engineers and manufacturers the confidence to select the appropriate grade for diverse applications. This section explores the ubiquitous presence of stainless steel, showcasing its versatility across a spectrum of industries, from the mundane to the highly specialized.
Culinary Applications: Where Hygiene and Durability Matter
Perhaps the most familiar application of stainless steel lies within our kitchens. Its resistance to corrosion and ease of cleaning make it ideal for food preparation and storage.
Pots, pans, and cutlery crafted from stainless steel are not only durable but also prevent the leaching of harmful substances into food.
Furthermore, its aesthetic appeal contributes to a clean and modern kitchen environment. The inert nature of the material is crucial in ensuring food safety, a paramount concern in both residential and commercial kitchens.
Fasteners: The Unsung Heroes of Structural Integrity
Moving beyond the kitchen, stainless steel plays a critical role in structural integrity. Fasteners such as bolts, screws, and nuts made from stainless steel are essential in construction, automotive, and aerospace applications.
These components ensure secure connections in environments where exposure to moisture or corrosive elements is unavoidable.
The superior strength and corrosion resistance of stainless steel fasteners guarantee long-term reliability and prevent structural failures, making them indispensable in critical applications.
Pressure Vessels: Containing the Uncontainable
In industries dealing with high-pressure containment, stainless steel pressure vessels are the gold standard. These vessels are designed to safely store and transport liquids and gases under significant pressure.
The material's high tensile strength and resistance to creep deformation at elevated temperatures make it ideally suited for this purpose.
Chemical processing plants, oil refineries, and power generation facilities rely on stainless steel pressure vessels to ensure the safe and efficient operation of their processes. The integrity of these vessels is paramount to preventing catastrophic failures and protecting personnel and the environment.
Piping: The Veins of Industry
The transportation of fluids and gases is a fundamental requirement across numerous industries. Stainless steel piping systems are the preferred choice in applications where corrosion resistance and hygiene are critical.
These systems are widely used in chemical processing, pharmaceuticals, food and beverage production, and water treatment plants.
The smooth surface of stainless steel minimizes friction and prevents the buildup of contaminants, ensuring the purity and integrity of the transported media. The longevity and reliability of stainless steel piping systems translate to reduced maintenance costs and minimized downtime.
Medical Implants: A Lifesaving Material
The biocompatibility of certain grades of stainless steel makes them suitable for medical implants. Surgical instruments, orthopedic implants, and cardiovascular stents utilize stainless steel for its strength, corrosion resistance, and ability to integrate with the body's tissues.
The material's inertness minimizes the risk of adverse reactions, such as inflammation or rejection. Stainless steel implants have significantly improved the quality of life for millions of patients, restoring mobility, function, and overall well-being.
Architectural Applications: Beauty and Longevity
Stainless steel is increasingly used in architectural applications. Its sleek appearance, durability, and resistance to environmental factors make it an attractive and practical choice for building facades, roofing, and interior design elements.
The material's ability to withstand harsh weather conditions and maintain its aesthetic appeal for decades ensures long-term value and reduces the need for frequent maintenance.
Stainless steel's versatility allows architects to create visually stunning and sustainable structures that stand the test of time.
Video: SS Abbreviation: Decoding Stainless Steel & Uses
FAQ: SS Abbreviation: Decoding Stainless Steel & Uses
What exactly does "SS" mean?
"SS" is the common abbreviation for stainless steel. It's a shorthand used widely in industries and everyday conversations to refer to this corrosion-resistant alloy.
Why is understanding "SS" important?
Recognizing "SS" as the abbreviation for stainless steel allows for quicker comprehension of product descriptions, material specifications, and engineering documents where space is often limited. It helps you understand what materials are being discussed or used.
Is "stainless steel" always truly "stainless"?
While stainless steel is highly corrosion-resistant, it's not entirely immune to staining or rust under all conditions. The term implies a high resistance, depending on the specific grade of stainless steel, but harsh environments can affect it. Therefore, "SS", the abbreviation for stainless steel, should be interpreted as highly resistant, but not infallible.
Where is stainless steel typically used?
Because of its durability and resistance to corrosion, stainless steel (often shortened to "SS") is used in many applications. These include cookware, surgical instruments, construction materials, food processing equipment, and automotive parts. Its versatility makes it a preferred material across diverse industries.
So, next time you see "SS" stamped on something, you'll know it's more than just a couple of letters! Hopefully, this has helped demystify stainless steel (SS) a bit and given you a better appreciation for its versatility and the science behind it. Pretty cool stuff, right?