Sauter Mean Diameter: Nozzle Selection Guide
Spray nozzle selection for specific applications requires careful consideration of several factors, with the Sauter Mean Diameter (SMD) being a critical parameter. The Sauter Mean Diameter, often measured using laser diffraction techniques, quantifies the average droplet size produced by a nozzle, influencing spray coverage and evaporation rates. The performance of agricultural spray nozzles, for instance, is heavily reliant on achieving an optimal SMD to ensure effective pesticide or fertilizer application, minimizing drift while maximizing target coverage. Furthermore, organizations like the American Society of Agricultural and Biological Engineers (ASABE) provide standards and guidelines for characterizing spray quality based on SMD values, aiding in the appropriate nozzle selection for various agricultural and industrial processes.
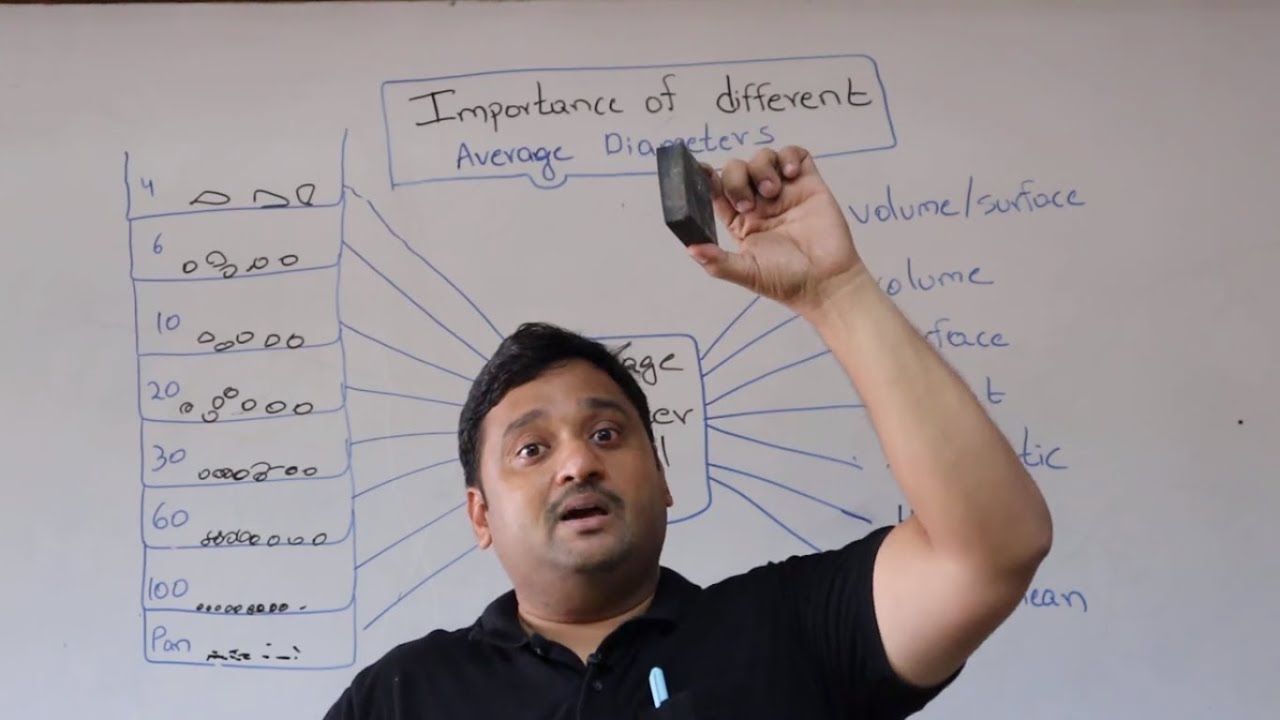
Image taken from the YouTube channel Dr. Surendra Sasikumar Jampa (PhD,Chem Engg, IITB) , from the video titled Lec 7: Why Different Average Diameters Exist?(Sautermean, Volumemean etc):Mechanical Unit Operations .
Liquid Atomization: The Science of Sprays
Liquid atomization, at its core, is the process of transforming a bulk liquid into a multitude of droplets, effectively creating a spray. This seemingly simple transformation underpins a vast array of industrial, agricultural, and even medical applications. The significance of atomization lies not only in the creation of sprays but also in the precise control over their characteristics.
Defining Atomization and its Significance
The term "atomization" often evokes images of atoms being separated, but in the context of fluid mechanics, it refers to the dispersion of a liquid into a collection of droplets. The scale of these droplets can range from several micrometers to millimeters, depending on the specific application and atomization technique employed.
Atomization is a critical process in:
- Spray drying, where liquid solutions are transformed into dry powders.
- Fuel injection, where fuel is atomized for efficient combustion in engines.
- Agricultural spraying, where pesticides and fertilizers are dispersed over crops.
In each of these examples, the effectiveness of the process hinges on the quality of the atomization. Poor atomization can lead to inefficient drying, incomplete combustion, or uneven distribution of agricultural chemicals, resulting in wasted resources and suboptimal performance.
Controlling Spray Characteristics: The Key to Optimization
The characteristics of a spray, such as droplet size distribution, spray pattern, and droplet velocity, are crucial determinants of its performance. Understanding and controlling these parameters is essential for optimizing application efficiency and achieving desired outcomes.
For instance, in spray drying, a narrow droplet size distribution ensures uniform drying and consistent product quality. In fuel injection, fine atomization promotes complete combustion and reduces emissions. In agricultural spraying, the spray pattern and droplet size must be carefully controlled to minimize drift and maximize target coverage.
Achieving this level of control requires a deep understanding of the factors that influence atomization, including liquid properties, nozzle design, and operating conditions. By manipulating these variables, engineers and scientists can tailor spray characteristics to meet the specific demands of a given application.
Decoding Spray Formation: Key Parameters at Play
The formation of a spray, seemingly instantaneous, is in reality a carefully orchestrated event governed by a confluence of factors. Understanding these parameters is paramount to achieving desired spray characteristics and optimizing application performance. These factors can be broadly categorized into: liquid properties, nozzle characteristics, and operational conditions, each exerting a distinct influence on the resulting spray.
Liquid Properties: The Foundation of Atomization
The inherent physical characteristics of the liquid being atomized play a fundamental role in determining the ease and quality of spray formation. Viscosity and surface tension are two primary liquid properties that significantly impact the atomization process.
Liquid Viscosity: Resistance to Flow
Liquid viscosity, often described as a fluid's resistance to flow, directly impacts atomization quality. High viscosity liquids require greater energy input to break apart into fine droplets.
This increased resistance typically results in larger droplet sizes and a less uniform spray pattern. Imagine trying to spray honey versus water; the difference in atomization is immediately apparent. This is because high viscosity liquids, like honey, have a tendency to form stringy sprays rather than fine mists.
Surface Tension: Holding the Droplet Together
Surface tension is the cohesive force that holds liquid molecules together, creating a "skin" at the liquid's surface. This property opposes the disruptive forces needed for atomization.
Higher surface tension necessitates more energy to overcome these cohesive forces and create new surfaces, i.e., droplets. Consequently, liquids with high surface tension tend to form larger, more stable droplets. Reducing surface tension through additives can significantly improve atomization.
Nozzle Characteristics: The Architect of the Spray
The design and construction of the nozzle are critical in shaping the spray. The nozzle orifice and the nozzle type are key factors that directly influence spray characteristics.
Nozzle Orifice: The Point of Exit
The size and shape of the nozzle orifice are fundamental in determining the droplet size and spray angle.
A smaller orifice generally produces finer droplets but may also restrict flow rate. The shape of the orifice affects the spray pattern, with different shapes designed to create specific spray patterns, such as cone-shaped or fan-shaped sprays.
Types of Nozzles: Tailoring the Spray
Different nozzle designs utilize varying mechanisms to achieve atomization, each with its own strengths and weaknesses. Understanding these differences is essential for selecting the appropriate nozzle for a given application.
Hydraulic Nozzles: Pressure-Driven Atomization
Hydraulic nozzles utilize liquid pressure to force the liquid through a small orifice, causing it to break up into droplets.
Their simplicity and reliability make them a common choice across various applications. However, they often require high pressures to achieve fine atomization.
Pneumatic Nozzles (Air-Assist/Air-Atomizing): Air-Induced Breakup
Pneumatic nozzles, also known as air-assist or air-atomizing nozzles, use compressed air to shear the liquid into fine droplets.
These nozzles are capable of producing very fine sprays at relatively low liquid pressures, making them suitable for applications requiring precise and uniform coverage.
Hollow Cone Nozzles:
Hollow cone nozzles produce a circular spray pattern with a hollow center.
These nozzles are often used in applications where coverage of a specific area is required, such as agricultural spraying or cooling towers.
Solid Cone Nozzles:
Solid cone nozzles generate a circular spray pattern with uniform droplet distribution across the entire cone.
They are commonly used in applications where complete coverage is essential, such as fire suppression systems.
Flat Fan Nozzles:
Flat fan nozzles create a flat, fan-shaped spray pattern.
These nozzles are often used in applications requiring linear coverage, such as surface coating or cleaning.
Full Cone Nozzles:
Full cone nozzles produce a cone shaped spray pattern that covers a broad circular area.
They are often used in applications that require a large volume of coverage.
Operational Conditions: Fine-Tuning the Spray
The conditions under which the nozzle operates, such as flow rate and spray pressure, significantly impact the resulting spray characteristics.
Flow Rate: The Volume of Liquid
The flow rate, or the volume of liquid passing through the nozzle per unit time, affects both droplet size and spray pattern.
Increasing the flow rate can lead to larger droplets and a wider spray angle, potentially compromising atomization quality if pressure is not adjusted accordingly.
Spray Pressure: The Force Behind the Spray
Spray pressure plays a crucial role in atomization, droplet size, and spray velocity.
Higher spray pressure generally results in finer droplets and increased spray velocity, improving atomization and coverage. However, excessively high pressure can lead to increased wear and tear on the nozzle and may also result in unwanted spray drift.
Characterizing Spray Quality: Measuring the Invisible
The true measure of a spray's effectiveness extends beyond visual inspection. To truly understand a spray, we must delve into quantifying its properties. This involves characterizing aspects of the spray such as droplet size, spray geometry, and spray dynamics. These characteristics will determine the suitability of the spray for its intended application.
Droplet Size: The Foundation of Spray Performance
Droplet size is arguably the most critical parameter in spray characterization. It directly influences factors like coverage, penetration, and evaporation rate. Therefore, understanding the nuances of droplet size is essential.
Droplet Size Distribution: Beyond the Average
A spray is not composed of uniformly sized droplets. Instead, it features a distribution of droplet sizes, ranging from very small to relatively large. Understanding this distribution is paramount. Averages alone can be misleading; knowing the range and frequency of different droplet sizes provides a more complete picture of the spray's potential performance.
Sauter Mean Diameter (SMD): A Key Metric
The Sauter Mean Diameter (SMD) represents the diameter of a droplet having the same surface area to volume ratio as the entire spray. In essence, it's a representative droplet size that accounts for both the total surface area and the total volume of the spray. SMD is a critical parameter for predicting evaporation rates, heat transfer, and mass transfer processes within the spray. A smaller SMD generally indicates finer atomization and increased surface area for interaction.
Uniformity Coefficient: Quantifying Spray Evenness
The Uniformity Coefficient is a metric used to assess the evenness of the droplet size distribution within a spray. A low coefficient indicates a narrow droplet size distribution, signifying a more uniform spray. This uniformity is desirable in applications where consistent coverage and performance are critical. A high coefficient suggests a wider range of droplet sizes, which can lead to uneven application and potential inefficiencies.
Monodisperse and Polydisperse Sprays: Defining Spray Types
Sprays can be broadly categorized as either monodisperse or polydisperse. Monodisperse sprays consist of droplets that are nearly uniform in size. Polydisperse sprays, on the other hand, exhibit a wide range of droplet sizes. While monodisperse sprays offer advantages in certain specialized applications (such as drug delivery), polydisperse sprays are more commonly encountered in industrial and agricultural settings. The choice between the two depends on the specific application requirements.
Spray Geometry: Shaping the Application
Beyond droplet size, the physical shape and extent of the spray play a crucial role in determining its effectiveness. Spray geometry encompasses factors such as spray angle, spray pattern, and coverage.
Spray Angle: Defining Spray Width
Spray angle refers to the angle formed by the diverging edges of the spray plume. It determines the width of the spray pattern at a given distance from the nozzle. Spray angle is typically measured using optical techniques or by analyzing spray deposit patterns. The appropriate spray angle depends on the application requirements. Narrow spray angles are suitable for targeted applications, while wider spray angles are preferable for covering larger areas.
Spray Pattern: Visualizing Spray Distribution
The spray pattern is a visual representation of the spatial distribution of liquid within the spray. It reveals how the liquid is dispersed across the target area. The spray pattern can be visualized using various techniques, including laser-induced fluorescence or by collecting the spray deposit on a substrate. An ideal spray pattern ensures uniform coverage and minimizes areas of over- or under-application.
Coverage: The Ultimate Goal
Coverage refers to the area effectively sprayed by the nozzle. Proper coverage is crucial for maximizing the efficacy of the application. Under-coverage can lead to missed areas and reduced performance, while over-coverage can result in wasted material and potential environmental concerns. The area of coverage is often assessed by visually inspecting the sprayed surface or by using specialized imaging techniques.
Dimensionless Numbers: Scaling Spray Behavior
Dimensionless numbers are powerful tools for scaling spray behavior and predicting performance under different conditions. They allow us to compare sprays generated by different nozzles, fluids, and operating conditions.
Weber Number (We): Predicting Atomization Quality
The Weber number (We) represents the ratio of inertial forces to surface tension forces. It provides insight into the stability of liquid droplets. A high Weber number indicates that inertial forces dominate, leading to droplet breakup and finer atomization. Conversely, a low Weber number suggests that surface tension forces are dominant, resulting in larger, more stable droplets. The Weber number is crucial for predicting the onset of atomization and optimizing nozzle design.
Reynolds Number (Re): Characterizing Flow Regime
The Reynolds number (Re) is a dimensionless quantity that characterizes the flow regime within the nozzle and the spray plume. It represents the ratio of inertial forces to viscous forces. A low Reynolds number indicates laminar flow, while a high Reynolds number suggests turbulent flow. The flow regime influences atomization efficiency and droplet size distribution.
Spray Dynamics: Capturing Movement and Change
Spray dynamics encompasses the temporal changes that occur within the spray plume. This includes droplet evaporation and potential for drift.
Evaporation Rate: Impact on Spray Performance
Evaporation rate refers to the rate at which liquid droplets transform into vapor. Several factors influence this, including temperature, humidity, droplet size, and air velocity. Evaporation can significantly impact spray performance. It reduces the size of droplets, increases their concentration, and alters their trajectory. Understanding evaporation rate is crucial for predicting the final distribution of the spray and optimizing application parameters.
Drift Potential: Addressing Environmental Concerns
Drift potential refers to the risk of spray droplets being carried away from the target area by wind or air currents. Drift is a major concern in agricultural and industrial spraying. It can lead to off-target contamination, environmental damage, and reduced application efficacy. Drift potential is influenced by droplet size, wind speed, and nozzle type. Assessing and minimizing drift potential is essential for responsible spray application.
Sprays in Action: Applications Across Industries
[Characterizing Spray Quality: Measuring the Invisible The true measure of a spray's effectiveness extends beyond visual inspection. To truly understand a spray, we must delve into quantifying its properties. This involves characterizing aspects of the spray such as droplet size, spray geometry, and spray dynamics. These characteristics will determine the quality of application of sprays.]
The utility of controlled liquid atomization extends far beyond theoretical understanding; it is a cornerstone of countless industrial, agricultural, energy, and environmental processes. By manipulating spray characteristics, engineers and scientists can optimize these processes for efficiency, effectiveness, and sustainability. Let's explore some of these applications:
Industrial Applications: Precision and Efficiency
Industrial applications of sprays often demand exacting precision and consistent performance.
Spray Drying: In the food and pharmaceutical industries, spray drying is employed to transform liquid solutions into dry powders. This process involves atomizing the liquid feed into a hot gas stream, causing rapid evaporation of the solvent and leaving behind solid particles.
Spray drying allows for the creation of heat-sensitive products because of the rapidity of the process. Milk powder production, for example, relies heavily on spray drying to create a stable and easily transportable product. Similarly, many pharmaceuticals are spray-dried to improve their bioavailability or shelf life. The precise control over droplet size and drying conditions is essential for ensuring product quality and consistency.
Coating Applications: The application of paints, protective coatings, and functional layers often relies on spray technology. Automotive painting, for example, demands uniform coverage, precise thickness, and minimal overspray.
Controlled atomization ensures that the coating material is evenly distributed across the surface, resulting in a smooth, durable finish. The benefits extend beyond aesthetics. Protective coatings used in aerospace or marine environments require careful control of spray parameters to ensure they provide adequate corrosion resistance and adhesion.
Agricultural Applications: Maximizing Coverage, Minimizing Drift
Agricultural spraying is a vital practice for crop protection and yield enhancement. The goal is to deliver pesticides, herbicides, and fertilizers to the target plants efficiently while minimizing off-target drift, which can have negative environmental and economic consequences.
Droplet size is a critical factor in agricultural spraying. Larger droplets are less prone to drift, reducing the risk of environmental contamination. However, they may also provide less uniform coverage of the plant surfaces. Smaller droplets, on the other hand, offer better coverage but are more susceptible to drift.
Optimizing droplet size distribution, spray pressure, and nozzle type is crucial for balancing these competing factors and achieving the desired outcome: effective pest control or nutrient delivery with minimal environmental impact. Precision agriculture techniques, such as variable rate spraying, rely on advanced spray technologies to apply inputs only where and when they are needed, further reducing waste and environmental impact.
Energy and Environmental Applications: Combustion and Control
Sprays play a significant role in energy production and environmental management.
Fuel Injection: Fuel injection is fundamental to the operation of internal combustion engines and gas turbines. The fuel is atomized into a fine spray, which mixes with air to create a combustible mixture. The quality of atomization directly affects combustion efficiency, fuel consumption, and emissions.
Improved atomization leads to more complete combustion, reducing the formation of pollutants such as unburned hydrocarbons, carbon monoxide, and particulate matter. In modern engines, advanced fuel injection systems use sophisticated nozzle designs and control strategies to optimize atomization under a wide range of operating conditions.
Fire Suppression: Water mist systems represent an innovative approach to fire suppression. These systems employ fine sprays of water to cool the fire, displace oxygen, and reduce radiant heat.
Water mist is particularly effective in enclosed spaces, where it can quickly suppress fires with minimal water damage. Compared to traditional sprinkler systems, water mist systems use significantly less water, reducing the risk of water damage and minimizing environmental impact. They are widely used in commercial buildings, data centers, and other sensitive environments.
The true measure of a spray's effectiveness extends beyond visual inspection. To truly understand a spray, we must delve into quantifying its properties. This involves characterizing aspects of the spray such as droplet size, spray geometry, and droplet velocity.
These parameters directly influence the performance of the spray in its intended application. Several advanced measurement techniques enable us to "see the unseen" and accurately characterize these spray characteristics.
Seeing the Unseen: Measurement Techniques for Spray Characterization
Characterizing spray behavior is crucial for optimizing processes across various industries. From ensuring uniform coating in manufacturing to maximizing pesticide efficacy in agriculture, understanding droplet size, velocity, and distribution is paramount. Fortunately, sophisticated measurement techniques provide detailed insights into these critical spray parameters.
Droplet Sizing Techniques
One of the most important aspects of spray characterization is determining the size distribution of the droplets. Several techniques are available for this purpose, each with its own strengths and limitations.
Laser Diffraction
Laser diffraction is a widely used technique for measuring droplet size distribution. It operates on the principle that droplets scatter light, with the angle of scattering being inversely proportional to the droplet size.
A laser beam is passed through the spray, and the resulting diffraction pattern is analyzed by a series of detectors. By analyzing the intensity of light at different angles, the droplet size distribution can be determined.
This method is relatively simple to implement and provides rapid measurements. However, it assumes that the droplets are spherical and may not be accurate for non-spherical droplets.
Phase Doppler Anemometry (PDA)
Phase Doppler Anemometry (PDA) is a more advanced technique that measures both the size and velocity of individual droplets simultaneously. PDA utilizes two laser beams that intersect at a point in the spray.
As a droplet passes through the intersection, it scatters the light from both beams. The scattered light is collected by detectors, and the phase difference between the light from the two beams is used to determine the droplet size.
The frequency of the scattered light provides the droplet velocity. PDA is highly accurate and can provide detailed information about the droplet size-velocity correlation. However, it is more complex and expensive than laser diffraction.
Imaging Techniques
Imaging techniques offer a direct visual representation of the spray and allow for the measurement of droplet size, shape, and velocity.
High-Speed Imaging
High-speed imaging captures images of the spray at very short exposure times. The fast exposure allows for the recording of individual droplets.
These images can then be analyzed to determine the size and velocity of the droplets. Specialized algorithms are employed to identify and measure the droplets.
High-speed imaging is particularly useful for studying dynamic spray phenomena, such as droplet breakup and coalescence. It provides a detailed visual record of the spray behavior. However, it can be challenging to analyze large numbers of images and accurately identify individual droplets in dense sprays.
Predicting Spray Behavior: Computational Modeling of Sprays
[The true measure of a spray's effectiveness extends beyond visual inspection. To truly understand a spray, we must delve into quantifying its properties. This involves characterizing aspects of the spray such as droplet size, spray geometry, and droplet velocity.
These parameters directly influence the performance of the spray in its intended application, but often, understanding these parameters through experimentation alone can be time-consuming and expensive. This is where computational modeling steps in as a powerful tool, offering insights and predictions that complement and, in some cases, replace physical experimentation.]
Computational modeling offers a way to simulate spray behavior and predict key characteristics, providing a virtual environment for optimizing spray systems. Among the various modeling techniques, Computational Fluid Dynamics (CFD) stands out as a versatile and widely adopted method.
Leveraging Computational Fluid Dynamics (CFD) for Spray Analysis
CFD is a numerical method that solves the governing equations of fluid dynamics to simulate fluid flow and heat transfer.
In the context of spray analysis, CFD is used to model the atomization process, droplet transport, and evaporation phenomena.
By discretizing the spray domain into a grid of cells and solving the governing equations at each cell, CFD can predict spray characteristics such as droplet size distribution, spray pattern, and droplet velocity.
How CFD Models Spray Formation
CFD models typically employ a combination of different approaches to simulate spray formation:
-
Primary Breakup Modeling: This approach focuses on modeling the initial stages of atomization, where the liquid jet or sheet breaks up into ligaments and subsequently into droplets. Various models are available to describe this process, including linear instability models, Kelvin-Helmholtz instability models, and Rayleigh-Taylor instability models.
-
Secondary Breakup Modeling: Once droplets are formed, they can undergo further breakup due to aerodynamic forces. Secondary breakup models account for this phenomenon, predicting the breakup of larger droplets into smaller ones.
-
Droplet Transport and Evaporation: After droplet formation and breakup, the droplets are transported by the surrounding gas flow. CFD models track the droplets' trajectories, accounting for drag forces, gravity, and other relevant factors. They also simulate droplet evaporation, which can significantly influence spray characteristics, especially in high-temperature environments.
Predicting Sauter Mean Diameter (SMD) with CFD
One of the key applications of CFD in spray analysis is predicting the Sauter Mean Diameter (SMD).
As discussed previously, SMD is a crucial metric for characterizing spray quality, as it represents the average droplet size in terms of surface area to volume ratio.
CFD simulations can predict SMD by solving the transport equations for droplet number density and droplet surface area density.
By accurately predicting SMD, CFD helps engineers optimize nozzle design and spray parameters to achieve the desired spray characteristics for specific applications.
The Role of CFD in Optimizing Nozzle Design and Spray Parameters
CFD plays a crucial role in optimizing nozzle design and spray parameters. By simulating spray behavior under different conditions, CFD can help engineers:
-
Identify optimal nozzle geometries for achieving desired droplet size distributions and spray patterns.
-
Determine optimal operating conditions, such as flow rate and spray pressure, for maximizing spray performance.
-
Evaluate the impact of different liquid properties on spray characteristics.
-
Reduce the need for expensive and time-consuming physical experiments by providing a virtual environment for testing different design options.
Benefits and Limitations of CFD
While CFD offers significant advantages for spray analysis, it's important to acknowledge its limitations.
Benefits:
- Cost-effective compared to experimental testing.
- Provides detailed insights into spray behavior.
- Facilitates optimization of nozzle design and spray parameters.
Limitations:
- Requires computational resources and expertise.
- Accuracy depends on the quality of the models and the accuracy of the input parameters.
- Can be time-consuming for complex simulations.
Despite these limitations, CFD remains a powerful tool for understanding and predicting spray behavior, enabling engineers to design and optimize spray systems for a wide range of applications. It's essential to note that CFD is often used in conjunction with experimentation. Experiments can be used to validate CFD results, and CFD can be used to interpolate and extrapolate experimental data.
Video: Sauter Mean Diameter: Nozzle Selection Guide
FAQs: Sauter Mean Diameter Nozzle Selection
What is Sauter Mean Diameter (SMD) and why is it important for nozzle selection?
Sauter Mean Diameter (SMD) is a way to express the average droplet size of a spray. It represents the diameter of a droplet having the same surface area to volume ratio as the entire spray.
Choosing a nozzle with the appropriate SMD is crucial. It impacts factors like coverage, penetration, drift potential, and reaction rates in applications like agricultural spraying, cooling, and coating.
How does SMD relate to the type of nozzle I should use?
Different nozzle types produce different droplet size distributions, resulting in varying Sauter Mean Diameters. For example, air atomizing nozzles generally produce finer sprays (smaller SMD) than hydraulic nozzles.
Your application's requirements for droplet size will dictate the most suitable nozzle type and operating parameters to achieve the desired Sauter Mean Diameter.
What factors besides nozzle type affect Sauter Mean Diameter?
Several factors influence the Sauter Mean Diameter, including liquid pressure, flow rate, fluid properties (viscosity and surface tension), and ambient conditions like air temperature and humidity.
Higher pressure generally reduces the Sauter Mean Diameter. Nozzle orientation and spray angle also play a role in the final droplet size achieved.
How can I find the right nozzle with a specific Sauter Mean Diameter for my needs?
Nozzle manufacturers typically provide data sheets or catalogs that list the Sauter Mean Diameter for their nozzles under various operating conditions.
Consider using a nozzle selection guide or consulting with a nozzle specialist to determine the optimal nozzle type and settings to achieve the desired Sauter Mean Diameter for your application.
So, there you have it! Hopefully, this guide gives you a solid starting point for understanding and utilizing Sauter Mean Diameter to pick the right nozzle for your application. It might seem a little complex at first, but getting a handle on Sauter Mean Diameter is key to optimizing your spray performance and getting the results you need. Happy spraying!