Motion Control Solutions: Guide to Types & Trends
Motion control solutions, pivotal in modern automation, are fundamentally transforming industries from robotics to aerospace. Precise manipulation, a critical attribute, is facilitated by sophisticated algorithms embedded within Programmable Logic Controllers (PLCs). Bosch Rexroth, a leader in automation technology, significantly contributes to the advancement of these motion control systems. The EtherCAT protocol, widely adopted in industrial settings, ensures real-time communication, thereby enabling synchronized and accurate movements in complex manufacturing processes.
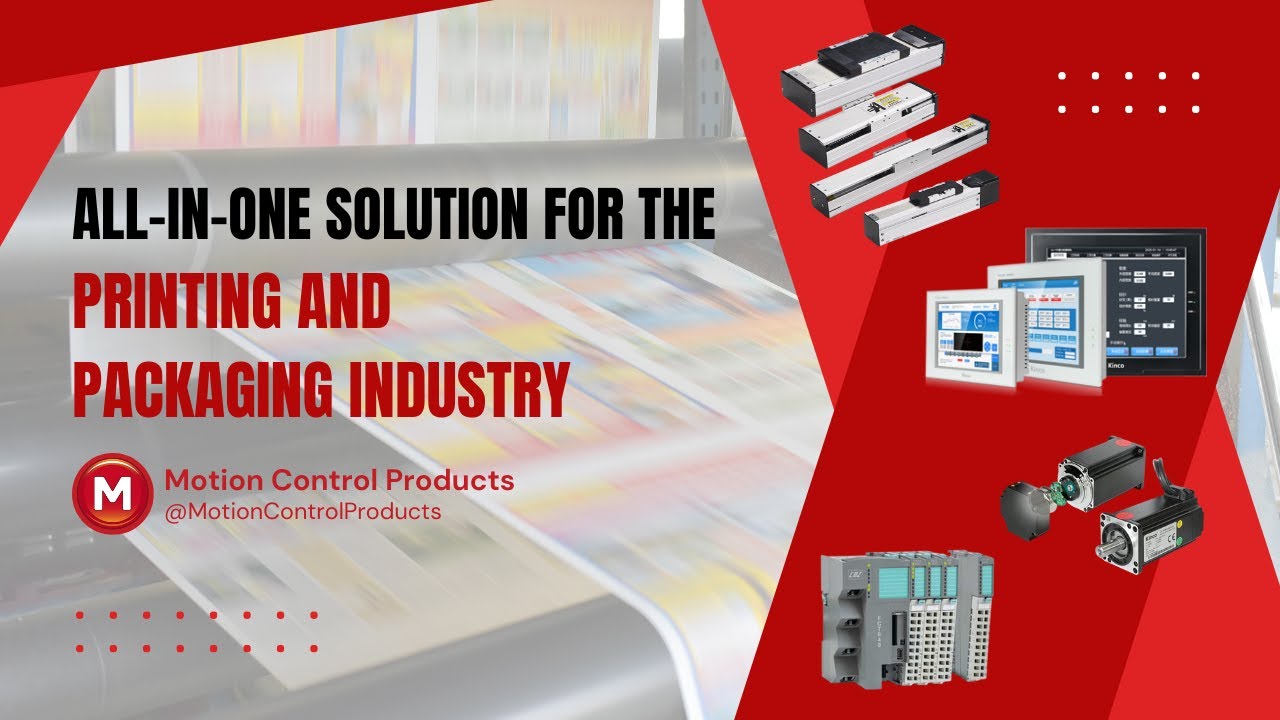
Image taken from the YouTube channel Motion Control Products Ltd , from the video titled Exploring Motion Control Solutions for Printing & Packaging | Industry Overview! 📰 .
Motion control systems are the unseen orchestrators of modern automation. They represent a sophisticated integration of mechanical, electrical, and computational elements, meticulously engineered to govern movement with unparalleled accuracy. Understanding their foundational principles is critical to appreciating their impact across diverse industries.
Defining Motion Control Systems
At its core, a motion control system is a mechanism designed to regulate the movement of an object or a series of objects. This control is achieved through a closed-loop process, where the actual motion is continuously monitored and compared against a desired motion profile.
Any deviation from this profile triggers corrective actions, ensuring that the object adheres as closely as possible to the intended trajectory. This feedback-driven approach distinguishes motion control from simple open-loop systems, which lack the ability to self-correct.
Fundamental Principles
Several key principles underpin the operation of effective motion control systems:
-
Feedback Control: Continuous monitoring of position, velocity, and acceleration, enabling real-time adjustments.
-
Servo Mechanisms: Utilizing servomotors and drives to translate control signals into precise mechanical motion.
-
Control Algorithms: Employing sophisticated algorithms, such as PID control, to optimize system response and stability.
-
Trajectory Planning: Generating smooth and efficient motion profiles that minimize wear and tear on mechanical components.
The Significance of Precision, Accuracy, and Reliability
In many applications, the value of a motion control system is directly proportional to its precision, accuracy, and reliability.
-
Precision refers to the repeatability of a motion. A precise system will consistently reproduce the same movement, even under varying conditions.
-
Accuracy, on the other hand, describes how closely the actual motion matches the desired motion. A highly accurate system will minimize the error between the target and achieved positions.
-
Reliability is the ability of the system to consistently perform its intended function over an extended period without failure.
These three attributes are non-negotiable for high-stakes applications like semiconductor manufacturing or medical robotics.
Impact on Application Performance
Imagine a robotic arm assembling microchips. Even a slight deviation from the intended position could render the entire product defective. Similarly, in a CNC machine, the accuracy of the cutting tool's trajectory directly affects the quality of the finished part.
-
Enhanced Throughput: More accurate and repeatable processes translate to fewer errors and less rework.
-
Improved Product Quality: Tighter control over motion parameters ensures that products meet stringent specifications.
-
Reduced Downtime: Reliable systems minimize the risk of unexpected failures, keeping production lines running smoothly.
Key Components: A System Overview
A typical motion control system comprises several interconnected components, each playing a crucial role in achieving precise and reliable movement.
These components include:
-
Motors: The primary source of motive power, converting electrical energy into mechanical motion.
-
Drives: Power amplifiers that regulate the voltage and current supplied to the motors.
-
Motion Controllers: The brains of the system, executing control algorithms and coordinating the movement of multiple axes.
-
Encoders: Sensors that provide feedback on motor position and velocity.
-
Mechanical Components: Gearboxes, actuators, and linear guides that translate rotary motion into linear motion and provide mechanical support.
Understanding these components and their interactions is fundamental to designing and implementing effective motion control solutions. Each element must be carefully selected and integrated to ensure optimal system performance.
Core Components: The Building Blocks of Motion Control
Motion control systems are the unseen orchestrators of modern automation. They represent a sophisticated integration of mechanical, electrical, and computational elements, meticulously engineered to govern movement with unparalleled accuracy. Understanding their foundational principles is critical to appreciating their impact across diverse industries. Let's delve into the individual components that form the bedrock of these advanced systems.
Motors: The Prime Movers
Motors are the heart of any motion control system, converting electrical energy into mechanical motion. The choice of motor dictates performance characteristics such as speed, torque, and precision. Several types are prevalent, each suited for specific applications.
Servomotors: Precision Redefined
Servomotors are designed for high-precision, closed-loop control systems. These motors incorporate feedback mechanisms, typically encoders, to provide real-time information on position and velocity. This allows the control system to make minute adjustments, achieving exceptional accuracy.
Servomotors excel in applications demanding precise positioning, such as robotics, CNC machining, and automated assembly lines. Their ability to maintain stability under varying loads makes them indispensable in demanding environments.
Stepper Motors: Incremental Accuracy
Stepper motors operate by dividing a full rotation into a discrete number of steps. Each step corresponds to a precise angular displacement, enabling accurate incremental movement. This characteristic makes them ideal for applications requiring precise positioning without the need for closed-loop feedback in simpler systems.
Stepper motors find widespread use in applications such as 3D printers, textile machines, and medical devices, where controlled, incremental motion is paramount.
AC Motors: Power and Speed
AC motors are widely used in industrial applications due to their robust design and ability to deliver high speed and power. Induction motors and synchronous motors are the most common types. These motors are known for their efficiency and reliability, especially in constant-speed applications.
AC motors are the workhorses of many industries, powering pumps, fans, compressors, and other heavy-duty equipment. Their ability to handle high loads and continuous operation makes them indispensable in numerous industrial settings.
DC Motors: Versatility and Portability
DC motors are characterized by their simplicity and suitability for battery-powered and portable devices. Brushed DC motors are simple and inexpensive, while brushless DC motors offer higher efficiency and longer lifespan.
DC motors are commonly found in applications such as electric vehicles, consumer electronics, and portable medical devices. Their compact size and ease of control make them a popular choice for a wide range of applications.
Drives (Motor Drives): Power and Control
Motor drives, also known as motor controllers, serve as intermediaries between the control system and the motor. They amplify and regulate the electrical power supplied to the motor, ensuring precise control over its speed, torque, and direction.
Motor drives are essential for optimizing motor performance and protecting it from overloads and other electrical faults.
Different types of motor drives are available, each tailored to specific motor types and application requirements. AC drives, DC drives, and servo drives are among the most common. Key parameters such as voltage, current, and control modes are carefully configured to achieve the desired motion profile.
Motion Controllers: The Brains of the Operation
Motion controllers are the central processing units of motion control systems. They execute control algorithms, interpret feedback signals, and generate commands to precisely manage motor movement. These controllers can range from simple, standalone units to complex, PC-based systems.
Standalone controllers are self-contained units designed for specific tasks, while PC-based controllers offer greater flexibility and processing power. Embedded controllers are integrated directly into the motor drive or other system components, providing a compact and efficient solution.
Key features of motion controllers include real-time processing, multi-axis control, and various communication interfaces. These features enable precise coordination of multiple motors and seamless integration with other system components.
Encoders: Providing Positional Awareness
Encoders are feedback devices that provide real-time information on motor position and velocity. This information is crucial for closed-loop control systems, enabling precise adjustments to maintain desired performance.
Encoders translate mechanical motion into electrical signals, allowing the control system to "see" what the motor is doing.
Two main types of encoders exist: incremental and absolute. Incremental encoders generate pulses as the motor rotates, while absolute encoders provide a unique code for each position. Absolute encoders offer the advantage of retaining position information even after power loss.
Encoders are widely used in applications such as robotics, CNC machines, and automated assembly lines, where precise position feedback is essential for accurate motion control.
Sensors: Beyond Encoders
While encoders provide critical position feedback, other sensors play important roles in motion control systems. Resolvers, for instance, are robust position feedback devices particularly well-suited for harsh environments. These analog sensors offer reliable performance in conditions where optical encoders might struggle.
Actuators: Translating Rotary to Linear
Actuators convert energy into mechanical motion. While motors provide rotary motion, many applications require linear movement. Linear actuators achieve this conversion, typically using mechanisms such as ball screws or lead screws. These actuators are found in applications ranging from valve control to precise positioning stages.
Mechanical Components: Amplifying and Adapting
Mechanical components play a vital role in adapting the motor's output to the specific requirements of the application. Gearboxes, for example, increase torque or reduce speed, optimizing the motor's performance for the task at hand. Other mechanical components, such as linkages and cams, can be used to create complex motion profiles.
Control Algorithms and Techniques: Guiding the Motion
Motion control systems are the unseen orchestrators of modern automation. They represent a sophisticated integration of mechanical, electrical, and computational elements, meticulously engineered to govern movement with unparalleled accuracy. Understanding their foundational principles is critical, but it is the control algorithms and techniques that truly dictate the system's performance, ensuring movements are not only accurate but also efficient and predictable. This section will delve into the software and mathematical aspects of motion control, focusing on PID control and trajectory planning, to explain how these techniques achieve precise and predictable movement.
PID Control: The Cornerstone of Feedback Control
PID (Proportional-Integral-Derivative) control forms the bedrock of many motion control systems. It's a feedback control loop mechanism used to regulate a process by continuously calculating an error value.
This error is the difference between a desired setpoint and the actual measured process variable. The PID controller then applies corrections based on proportional, integral, and derivative terms.
Understanding the PID Components
-
Proportional (P): The proportional term provides a control output that is proportional to the current error value. A larger error results in a larger corrective response. While simple, relying solely on proportional control often results in a steady-state error.
-
Integral (I): The integral term addresses the accumulated error over time. It eliminates steady-state errors that proportional control alone cannot handle. However, an excessively large integral term can lead to oscillations or instability.
-
Derivative (D): The derivative term predicts future errors based on the rate of change of the current error. This anticipates changes and dampens oscillations, improving system stability and response time. The derivative term is sensitive to noise and requires careful implementation.
Tuning the PID Controller
Properly tuning a PID controller is paramount to achieving optimal performance. The process involves finding the right balance between the P, I, and D gains to meet specific performance requirements.
-
Manual Tuning: This method involves adjusting the gains one at a time. Observe the system's response to step changes in the setpoint. It requires experience and a good understanding of the system's dynamics.
-
Auto-Tuning Techniques: Algorithms automatically calculate the optimal PID gains based on the system's response to test signals. Auto-tuning methods can significantly reduce the time and effort required for tuning. However, they may not always yield the best possible performance.
PID Applications in Motion Control
PID control is versatile and applicable to various aspects of motion control:
-
Position Control: PID is used to accurately position a motor or actuator to a desired location. This is essential in applications such as robotics and CNC machining.
-
Velocity Control: Maintaining a constant speed or following a desired velocity profile requires precise velocity control. PID ensures the motor accelerates and decelerates smoothly and accurately.
-
Torque Control: In some applications, controlling the torque output of a motor is critical. PID control regulates the motor current to achieve the desired torque.
Trajectory Planning: Orchestrating Movement Paths
Trajectory planning is the process of generating a time-based sequence of positions, velocities, and accelerations. These guide a motion control system from an initial state to a desired final state. It's not just about getting from point A to point B, but about how the system gets there.
Defining Optimal Motion Paths
Trajectory planning optimizes motion paths by considering several factors, including:
-
Minimizing travel time: Reducing cycle times is crucial for increasing productivity in many applications.
-
Minimizing energy consumption: Optimizing the motion profile can significantly reduce energy usage.
-
Reducing wear and tear: Smooth motion profiles with limited jerk can extend the lifespan of mechanical components.
Trajectory Planning Techniques
Different applications require different trajectory planning techniques:
-
Point-to-Point Motion: In this simple approach, the system moves directly from one point to another without regard for the path. It's suitable for applications where the path is not critical.
-
Continuous Path Motion: This involves generating a smooth path that passes through a series of predefined points. It's essential for applications such as CNC machining and robotic welding.
Important Considerations
Several critical factors influence trajectory planning:
-
Jerk Limitation: Jerk is the rate of change of acceleration. Limiting jerk prevents sudden changes in acceleration, reducing stress on mechanical components and improving ride quality.
-
Acceleration Profiling: Choosing the appropriate acceleration profile (e.g., trapezoidal, S-curve) can significantly affect the smoothness and efficiency of the motion. S-curve profiles, for instance, provide a smoother transition than trapezoidal profiles, reducing jerk.
Applications of Motion Control: Where Precision Matters
Motion control systems are the unseen orchestrators of modern automation. They represent a sophisticated integration of mechanical, electrical, and computational elements, meticulously engineered to govern movement with unparalleled accuracy. Understanding their foundational principles is critical, but it's equally important to grasp the breadth and depth of their real-world applications. From the factory floor to the operating room, motion control technology is driving innovation and efficiency across a diverse spectrum of industries.
This section highlights some of the most prominent applications, demonstrating how precision motion enables groundbreaking advancements.
Motion Control in Manufacturing: The Backbone of Automation
Manufacturing stands as one of the earliest and most pervasive adopters of motion control systems. The demand for increased throughput, reduced waste, and improved product quality has made motion control an indispensable component of modern production lines.
Automated assembly lines rely heavily on sophisticated motion control systems to coordinate the movement of parts, tools, and robots. Pick-and-place machines, for example, utilize precise motion control to rapidly and accurately position components onto circuit boards or within packaging. Similarly, robotic welding systems employ complex motion profiles to ensure consistent and high-quality welds across a variety of materials and geometries.
Furthermore, advanced material handling systems leverage motion control to efficiently transport raw materials, work-in-progress, and finished goods throughout the manufacturing facility. Conveyor systems, automated guided vehicles (AGVs), and robotic palletizers all depend on precise and reliable motion to maintain a smooth and uninterrupted flow of production.
Robotics: Enabling Dexterity and Precision
Motion control forms the very essence of robotics. Without precise and coordinated control of joint movements, robots would be relegated to simple, repetitive tasks. Motion control systems provide the "brains" and "muscle" necessary for robots to perform complex operations with dexterity and accuracy.
Industrial robots, commonly employed in manufacturing, rely on sophisticated multi-axis motion control to execute tasks such as welding, painting, assembly, and material handling. These robots often incorporate advanced control algorithms, such as inverse kinematics and trajectory planning, to ensure smooth and accurate movements along complex paths.
Beyond industrial applications, motion control is also crucial in the development of mobile robots and autonomous vehicles. Self-driving cars, for instance, require precise control of steering, throttle, and braking systems to navigate roadways safely and efficiently. Similarly, mobile robots used in logistics and warehousing depend on motion control to autonomously navigate complex environments and perform tasks such as picking and packing.
Packaging: Ensuring Speed and Accuracy
The packaging industry is another significant beneficiary of motion control technology. High-speed packaging machines require precise and synchronized motion to accurately fill, seal, and label products.
Form-fill-seal (FFS) machines, commonly used in the food and beverage industry, utilize sophisticated motion control systems to precisely form the packaging material, fill it with the product, and then seal it securely. Similarly, labeling machines rely on precise motion to accurately position labels onto products at high speeds.
Motion control also plays a crucial role in ensuring the integrity of the packaging process. Systems that incorporate vision inspection and feedback control can detect and reject defective packages, minimizing waste and ensuring product quality.
Semiconductor Manufacturing: The Pinnacle of Precision
Semiconductor manufacturing represents perhaps the most demanding application of motion control technology. The fabrication of microchips requires extreme precision and accuracy, often down to the nanometer scale.
Wafer handling systems, for example, utilize sophisticated motion control to precisely position and move silicon wafers through various stages of the manufacturing process. These systems must minimize vibration and ensure smooth, controlled movements to prevent damage to the delicate wafers.
Lithography systems, which are used to pattern the circuits onto the wafers, also rely on extreme precision motion control. These systems employ advanced motion stages and feedback control to ensure that the patterns are accurately aligned and positioned on the wafer.
Medical Devices: Enhancing Diagnostics and Treatment
Motion control is increasingly prevalent in the medical device industry, enabling advancements in diagnostics, treatment, and rehabilitation.
Surgical robots, for instance, allow surgeons to perform minimally invasive procedures with enhanced precision and control. These robots utilize multi-axis motion control to accurately guide surgical instruments and provide surgeons with haptic feedback.
Medical imaging devices, such as MRI scanners and CT scanners, also rely on motion control to precisely position the patient and acquire high-resolution images. Rehabilitation robots employ motion control to assist patients in regaining motor skills and improving their range of motion.
Aerospace: Controlling Flight and Beyond
The aerospace industry utilizes motion control in a variety of applications, ranging from flight surface control to satellite positioning.
Aircraft flight control systems rely on precise motion control to adjust the position of control surfaces such as ailerons, elevators, and rudders. These systems must be highly reliable and responsive to ensure safe and stable flight.
Satellite positioning systems utilize motion control to accurately orient satellites in space. These systems often employ reaction wheels or thrusters, controlled by precise motion algorithms, to maintain the satellite's orientation and point its instruments towards the desired targets.
Automotive: Automating Production and Improving Performance
Motion control is pervasive in the automotive industry, both in the manufacturing of vehicles and in the vehicles themselves.
In automotive manufacturing, robots with advanced motion control systems perform tasks such as welding, painting, and assembly. These robots enhance productivity, improve quality, and reduce labor costs.
Modern vehicles also incorporate motion control systems in various applications, such as electronic stability control (ESC), anti-lock braking systems (ABS), and adaptive cruise control (ACC). These systems utilize sensors and actuators to enhance vehicle safety and improve driving performance.
Computer Numerical Control (CNC): The Foundation of Automated Machining
CNC machining remains a cornerstone of manufacturing. CNC machines use programmed instructions to control the movement of cutting tools, enabling the automated production of complex parts with high precision.
Motion control is fundamental to CNC technology, dictating the speed, direction, and acceleration of the cutting tool. Advanced CNC systems incorporate sophisticated algorithms to optimize toolpaths, minimize vibration, and improve surface finish. The ability to create intricate and precise parts has revolutionized manufacturing processes across numerous industries.
Communication Protocols: Connecting the System
[Applications of Motion Control: Where Precision Matters Motion control systems are the unseen orchestrators of modern automation. They represent a sophisticated integration of mechanical, electrical, and computational elements, meticulously engineered to govern movement with unparalleled accuracy. Understanding their foundational principles is crit...]
In the intricate world of motion control, the seamless exchange of information between components is paramount. This section delves into the critical role of communication protocols, the digital languages that enable drives, controllers, and sensors to function as a cohesive unit. We will focus on fieldbus networks, the backbone of modern industrial automation, specifically examining EtherCAT and PROFINET.
The Importance of Communication Protocols
Effective communication is the nervous system of any advanced motion control system. It dictates the speed, reliability, and determinism of data transfer. The choice of protocol directly impacts the system's overall performance, scalability, and diagnostic capabilities.
A robust communication network ensures that commands are executed precisely. Feedback is received promptly, and errors are detected and managed efficiently.
Fieldbus Networks: The Industrial Backbone
Fieldbus networks are designed to operate in harsh industrial environments. They provide real-time communication between devices. Unlike standard Ethernet, fieldbuses offer deterministic behavior, a critical requirement for synchronized motion.
Determinism means that data transmission times are predictable and consistent. This is essential for applications demanding precise coordination between multiple axes of motion.
EtherCAT: High-Performance Communication
EtherCAT (Ethernet for Control Automation Technology) has emerged as a leading protocol in high-performance automation. Its on-the-fly processing significantly reduces latency.
Technical Superiority of EtherCAT
EtherCAT employs a unique "telegram processing on the fly" approach. Each device reads and writes data as the telegram passes through. This eliminates the need for individual nodes to process and forward each packet separately.
The result is exceptionally fast cycle times, often in the microsecond range, making it ideal for demanding applications like robotics, semiconductor manufacturing, and high-speed packaging.
EtherCAT Advantages
- High Speed: Enables exceptionally fast communication cycles.
- Flexible Topology: Supports various network topologies (line, star, tree).
- Synchronization: Provides excellent synchronization capabilities for multi-axis motion.
- Cost-Effective: Reduces hardware costs due to simplified cabling and infrastructure.
PROFINET: Industrial Ethernet Standard
PROFINET (Process Field Network) is an Industrial Ethernet standard developed by Siemens. It leverages standard Ethernet infrastructure while adding features for real-time communication and industrial robustness.
Versatility of PROFINET
PROFINET offers several conformance classes to meet diverse application requirements. These range from non-real-time communication to highly deterministic isochronous real-time (IRT) communication.
This versatility allows PROFINET to be used in a wide range of applications. They include process automation, factory automation, and motion control.
PROFINET Advantages
- Integration: Seamlessly integrates with existing Ethernet networks.
- Scalability: Supports large and complex network topologies.
- Real-Time Communication: Offers deterministic communication for time-critical applications.
- Diagnostics: Provides extensive diagnostic capabilities for network monitoring and troubleshooting.
Selecting the Right Protocol
Choosing the appropriate communication protocol is a critical decision. It should be based on the specific requirements of the application.
Factors to consider include:
- Real-time performance needs.
- Network topology.
- Integration with existing systems.
- Cost constraints.
While EtherCAT excels in high-speed, deterministic applications, PROFINET offers broader compatibility and scalability. Careful evaluation is crucial to ensure optimal system performance and reliability.
Key Players: Leading Companies in Motion Control
[Communication Protocols: Connecting the System Applications of Motion Control: Where Precision Matters Motion control systems are the unseen orchestrators of modern automation. They represent a sophisticated integration of mechanical, electrical, and computational elements, meticulously engineered to govern movement with unparalleled accuracy. Und...]
The motion control industry is populated by a diverse array of companies, each contributing unique expertise and specialized solutions. These key players drive innovation, set industry standards, and provide the building blocks for automated systems across the globe. Here's a look at some of the leading companies shaping the motion control landscape:
Titans of Automation: Comprehensive Solution Providers
These companies offer broad portfolios of motion control products integrated with extensive automation solutions.
Siemens: As a global powerhouse in automation, Siemens provides a comprehensive range of motion control solutions, from drives and motors to PLCs and CNC systems. Their integrated approach and industry-specific expertise make them a go-to provider for complex automation projects.
Rockwell Automation: Rockwell Automation offers a wide array of industrial automation and motion control solutions, excelling in programmable logic controllers (PLCs), human-machine interfaces (HMIs), and integrated motion systems. Their emphasis on scalability and connectivity makes them a popular choice for modern manufacturing environments.
ABB: ABB's expertise spans robotics, motion, and automation technologies, offering comprehensive solutions for industrial automation. Their strength lies in robotics and high-performance motion control systems, catering to industries requiring advanced automation capabilities.
Schneider Electric: Schneider Electric offers a comprehensive range of motion control products and systems, focusing on energy management and automation solutions. Their focus on sustainable solutions and energy efficiency distinguishes them in the motion control market.
Specialists in Precision Motion: Focusing on Core Components
These companies specialize in manufacturing high-quality components, such as motors, drives, and linear motion systems.
Delta Electronics: Delta Electronics is a leading provider of motion control products, known for their robust drives and motors used in various industrial applications. Their focus on power electronics and energy efficiency complements their motion control offerings.
Yaskawa: Yaskawa is a global leader in servo systems, motion controllers, and robotics, offering comprehensive motion control solutions for industrial automation. Their high-performance servo systems and advanced motion control technology are widely adopted in industries requiring precise motion.
Mitsubishi Electric: Mitsubishi Electric offers advanced motion control technology, particularly in servo systems, CNC systems, and programmable logic controllers (PLCs). Their innovative solutions are employed across industries demanding high precision and reliability.
Bosch Rexroth: Bosch Rexroth excels in drive and control technologies, offering a wide range of hydraulic, electric, and pneumatic solutions for industrial automation. Their integrated approach to motion control systems and their focus on industry-specific applications make them a valuable partner for automation projects.
Parker Hannifin: Parker Hannifin delivers motion and control technologies, including hydraulic, pneumatic, and electromechanical systems. Their diverse portfolio and expertise in fluid power make them a leading supplier of motion control components and systems.
Niche Players and Innovators: Pushing the Boundaries of Motion
These companies focus on specialized applications or cutting-edge technologies in motion control.
Moog: Moog specializes in high-performance motion control solutions, including servo valves, actuators, and integrated systems for demanding applications in aerospace, defense, and industrial markets. Their expertise in precision motion control and hydraulic systems makes them a key player in critical applications.
Beckhoff Automation: Beckhoff Automation is renowned for its PC-based control technology, offering innovative solutions for automation and motion control. Their EtherCAT-based control systems and open architecture provide flexibility and scalability for a wide range of applications.
Hiwin Technologies: Hiwin Technologies focuses on linear motion components and systems, including linear guides, ball screws, and actuators. Their high-quality products and focus on linear motion technology make them a key supplier for industrial automation applications.
THK: THK is known for its linear motion guides and actuators, offering precision components for industrial automation. Their expertise in linear motion technology and their focus on high-performance solutions make them a valuable partner for demanding applications.
Aerotech: Aerotech specializes in precision motion control systems, including positioning stages, motion controllers, and air bearings. Their high-performance solutions are used in demanding applications such as semiconductor manufacturing and laser processing.
PI (Physik Instrumente): PI (Physik Instrumente) is a leading provider of nanopositioning and precision motion control solutions, offering high-resolution stages, actuators, and controllers. Their expertise in piezo technology and nanopositioning makes them a key player in scientific and industrial applications.
Omron: Omron provides integrated motion control solutions, combining PLCs, servo systems, and vision systems for comprehensive automation. Their focus on integrated solutions and their expertise in automation make them a valuable partner for manufacturers.
This overview provides a snapshot of the leading companies driving innovation and shaping the future of motion control. The competitive landscape ensures continuous development and refinement of motion control technologies, ultimately benefiting industries seeking greater precision, efficiency, and automation.
Future Trends: The Evolution of Motion Control
Motion control systems are the unseen orchestrators of modern automation. They represent a sophisticated integration of mechanical, electrical, and computational elements, meticulously engineered to achieve precise and repeatable movements. As technology continues to advance at an exponential pace, several key trends are poised to reshape the landscape of motion control. Understanding these trends is crucial for stakeholders looking to leverage the next generation of automation solutions.
Digital Twins: Virtualizing the Physical World
The concept of a digital twin—a virtual replica of a physical system—is gaining significant traction in the motion control domain. Digital twins enable engineers to simulate, analyze, and optimize the behavior of motion control systems in a virtual environment, prior to physical implementation.
This approach offers numerous benefits, including reduced development time, lower costs, and improved system performance. By creating accurate digital models, manufacturers can identify potential design flaws, test different control strategies, and predict system behavior under various operating conditions. This proactive approach minimizes costly errors and ensures optimal performance once the physical system is deployed.
AI and Machine Learning: Intelligent Motion
Artificial intelligence (AI) and machine learning (ML) are revolutionizing motion control by enabling systems to learn, adapt, and optimize their performance in real-time. These technologies are being applied to a wide range of applications, including predictive maintenance, adaptive control, and automated system tuning.
Predictive maintenance algorithms analyze sensor data to detect anomalies and predict potential failures, allowing maintenance teams to proactively address issues before they result in downtime. Adaptive control algorithms continuously adjust control parameters based on real-time feedback, ensuring optimal performance even in the face of changing operating conditions. Furthermore, AI algorithms are increasingly used to automate the process of tuning PID controllers, significantly reducing the time and effort required to optimize system performance.
Cloud-Based Motion Control: Remote Management and Monitoring
Cloud-based motion control platforms are enabling remote monitoring, control, and diagnostics of motion control systems. By connecting systems to the cloud, manufacturers can gain real-time visibility into system performance, access historical data for analysis, and remotely troubleshoot issues.
This capability is particularly valuable for applications involving geographically dispersed systems or those operating in remote or hazardous environments. Cloud-based platforms also facilitate collaboration among engineers and technicians, enabling them to share data, insights, and best practices more effectively. Security concerns surrounding sensitive production data remain a pivotal area of focus for cloud adoption in motion control applications.
Edge Computing: Bringing Intelligence to the Edge
Edge computing involves processing data closer to the source, reducing latency and improving response times. In motion control, edge computing enables real-time decision-making and control, even in the absence of a reliable network connection.
By deploying processing power at the edge, systems can analyze sensor data locally, execute control algorithms, and respond to changing conditions with minimal delay. This is particularly important for applications requiring high-speed, precise control, such as robotics and automated manufacturing. The combination of edge and cloud computing offers a powerful approach to motion control, balancing the need for real-time performance with the benefits of centralized data management and analysis.
EtherCAT Adoption: The Need for Speed
EtherCAT (Ethernet for Control Automation Technology) is becoming increasingly prevalent in motion control systems. Its high-performance and real-time capabilities make it an ideal choice for demanding applications requiring synchronized motion across multiple axes.
EtherCAT's distributed clock synchronization ensures precise coordination between different components of the system, enabling highly accurate and repeatable movements. The increasing adoption of EtherCAT reflects the growing demand for faster, more reliable communication protocols in the motion control industry.
Sensor Fusion: Enhanced Awareness
Sensor fusion combines data from multiple sensors to provide a more comprehensive and accurate understanding of the system's state. By integrating data from encoders, accelerometers, vision systems, and other sensors, motion control systems can achieve enhanced awareness of their environment and respond more effectively to changing conditions.
Sensor fusion enables more robust and reliable control, especially in applications where individual sensors may be subject to noise or interference. This technology is particularly valuable for applications requiring high levels of precision and accuracy, such as robotics and autonomous vehicles.
Collaborative Robots (Cobots): Working Hand-in-Hand
Collaborative robots, or cobots, are designed to work safely alongside humans, sharing the same workspace. Motion control plays a critical role in ensuring the safety and performance of cobots.
Advanced motion control algorithms enable cobots to sense their environment, detect human presence, and adjust their movements accordingly. This allows them to perform tasks that would be unsafe or impractical for traditional robots. As cobots become more sophisticated, motion control will continue to be a key enabler of their safe and effective integration into manufacturing and other industries.
Integrated Safety Features: Prioritizing Safety
Safety is paramount in motion control applications, particularly those involving human-machine interaction. Integrated safety features are becoming increasingly common in motion control systems, providing built-in protection against accidents and injuries.
These features include safe torque off (STO), safe stop 1 (SS1), and safe limited speed (SLS), which can be activated in response to unexpected events or detected hazards. Integrated safety features help to ensure that motion control systems operate safely and reliably, protecting both personnel and equipment.
Predictive Maintenance: Preventing Failures Before They Happen
Predictive maintenance leverages data analytics to anticipate potential failures in motion control systems, allowing maintenance teams to proactively address issues before they result in downtime.
By analyzing sensor data, historical maintenance records, and other relevant information, predictive maintenance algorithms can identify patterns and trends that indicate impending failures. This enables maintenance teams to schedule repairs and replacements in advance, minimizing disruptions to production and reducing the risk of costly unplanned downtime.
Video: Motion Control Solutions: Guide to Types & Trends
FAQs: Motion Control Solutions Guide
What are the primary types of motion control covered in the guide?
The guide primarily covers electric, hydraulic, and pneumatic motion control solutions. Each uses different power sources and mechanisms to achieve precise movement. We also discuss hybrid systems that combine these approaches.
How has digitalization impacted motion control?
Digitalization has led to smarter, more connected motion control solutions. This includes advanced control algorithms, predictive maintenance, and seamless integration with industrial networks for real-time data and optimization.
What key trends are shaping the future of motion control?
Key trends include increased use of AI and machine learning for autonomous motion, the rise of collaborative robots (cobots), and a growing emphasis on energy efficiency and sustainability in motion control solutions.
Why is understanding different motion control types important?
Understanding the various types allows engineers and designers to select the optimal motion control solutions for specific applications. Factors like precision, speed, load capacity, and environmental constraints all play a crucial role in this decision-making process.
So, there you have it! Hopefully, this has given you a clearer picture of the wide world of motion control solutions and where things are headed. Whether you're just starting out or looking to upgrade your existing systems, understanding these types and trends can really make a difference in achieving smoother, more efficient, and ultimately, more successful operations. Happy automating!