Mass Ratio: Rocketry Explained | Formula & Examples
In rocketry, the performance of vehicles such as the Saturn V, a critical component of NASA's Apollo program, is fundamentally governed by the mass ratio. The mass ratio, a dimensionless parameter, mathematically relates a rocket's initial mass to its final mass after propellant is expended. This parameter is crucial in the Tsiolkovsky rocket equation, which defines the theoretical limits of a rocket's velocity change (delta-v). Therefore, a higher mass ratio typically indicates a more efficient rocket design, and advanced materials contribute to optimizing it by minimizing structural weight.
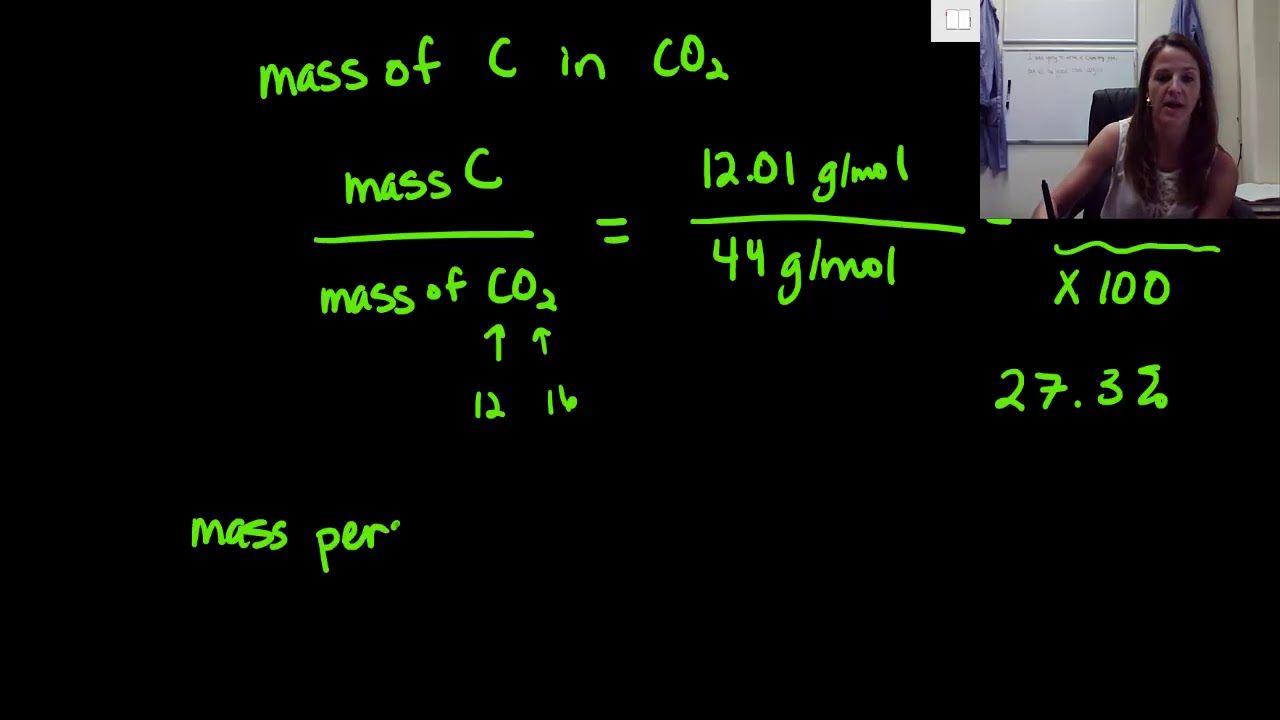
Image taken from the YouTube channel Kate Biberdorf , from the video titled Mass Ratio .
The Indispensable Mass Ratio: A Cornerstone of Rocketry
In the realm of space exploration, where ambition meets the unforgiving laws of physics, the concept of mass ratio stands as a pivotal determinant of success. It is not merely a technical parameter; it is the embodiment of efficiency, the keystone upon which mission feasibility rests, and a direct reflection of our capacity to transcend terrestrial bounds. Understanding mass ratio is essential for grasping the fundamental challenges and triumphs of rocketry.
Defining Mass Ratio: The Essence of Propulsive Efficiency
Mass ratio is defined as the quotient of a rocket's initial mass to its final mass. Simply stated, it’s the rocket’s mass fully fueled and ready for launch divided by the rocket’s mass after all its propellant is expended. This dimensionless ratio encapsulates the proportion of the rocket's mass that is dedicated to propellant versus the mass that comprises the vehicle itself – the structure, engines, payload, and other non-expendable components.
A higher mass ratio implies that a greater percentage of the rocket's initial mass is dedicated to propellant. This, in turn, suggests a greater potential for achieving higher velocities and, consequently, more ambitious missions.
Significance: Mission Enablement and Performance Bottleneck
The significance of mass ratio extends far beyond mere calculation. It dictates whether a particular mission is even possible within the constraints of current technology and budget. A spacecraft destined for Mars, for instance, requires a significantly higher mass ratio than a satellite intended for low Earth orbit. This is because the delta-v (change in velocity) required for interplanetary travel is substantially greater.
Put plainly: A high mass ratio is critical for deep space missions.
Moreover, mass ratio directly influences the size and cost of a launch vehicle. A rocket with a poor mass ratio will require significantly more propellant to achieve a given mission profile. This necessitates larger and more expensive tanks, engines, and overall vehicle architecture. Thus, optimizing mass ratio is not only about achieving greater performance. It's also about minimizing costs and maximizing the efficiency of resource utilization.
Scope: Principles, Technologies, and Pioneering Figures
This exploration will delve into the underlying principles governing mass ratio, primarily the Tsiolkovsky Rocket Equation, which mathematically articulates the relationship between mass ratio, exhaust velocity, and delta-v. We will also examine the key technologies and design strategies employed to optimize mass ratio, including:
-
Staging
-
Advanced Materials
-
High-Efficiency Engines
Furthermore, this discussion will recognize the profound contributions of historical figures, like Konstantin Tsiolkovsky and Wernher von Braun, whose insights and innovations shaped our understanding of mass ratio and its critical role in enabling spaceflight. By exploring these principles, technologies, and historical contexts, we aim to provide a comprehensive understanding of mass ratio, the silent architect of space exploration.
Foundational Principles: Decoding the Rocket Equation and its Components
The pursuit of efficient space travel hinges on a deep understanding of the fundamental principles that govern rocket propulsion. Central to this understanding is the Tsiolkovsky Rocket Equation, a mathematical cornerstone that elegantly describes the relationship between a rocket's change in velocity (delta-v), its exhaust velocity, and its mass ratio. Let's delve into the intricacies of this equation and explore the crucial concepts that underpin its significance.
The Tsiolkovsky Rocket Equation Unveiled
The Tsiolkovsky Rocket Equation, often referred to simply as the rocket equation, is expressed as:
Δv = ve * ln(m₀/mf)
Where:
- Δv represents the change in velocity (delta-v) that the rocket can achieve.
- ve is the exhaust velocity of the propellant.
- m₀ is the initial total mass of the rocket (including propellant).
- mf is the final total mass of the rocket (after all propellant is spent).
- ln denotes the natural logarithm.
This equation reveals a profound truth: the change in velocity a rocket can achieve is directly proportional to the exhaust velocity of its propellant and the natural logarithm of its mass ratio.
Unpacking the Variables: Delta-V, Exhaust Velocity, and Mass Ratio
Each variable within the rocket equation holds significant weight in determining a rocket's performance. Delta-v (Δv) is a measure of the total change in velocity a rocket can achieve and represents the total "effort" the rocket can exert. It dictates the types of missions possible, from reaching orbit to traveling to distant planets.
Exhaust velocity (ve) is the speed at which the propellant is expelled from the rocket engine. It's a crucial factor, as higher exhaust velocities translate to greater efficiency. Specific Impulse (Isp) is directly proportional to the exhaust velocity, and is measured in seconds.
The mass ratio (m₀/mf), as previously defined, is the ratio of the rocket's initial mass to its final mass. It embodies the proportion of the rocket's mass that is dedicated to propellant. A higher mass ratio indicates that a larger fraction of the rocket's mass is propellant, allowing for a greater change in velocity.
The Impact of Mass Ratio on Achievable Delta-V
The rocket equation starkly illustrates how mass ratio directly influences the achievable change in velocity. For a given exhaust velocity, a higher mass ratio allows for a significantly greater delta-v.
This relationship underscores the importance of minimizing the dry mass of the rocket (the mass without propellant) and maximizing the amount of propellant carried.
In essence, a higher mass ratio equates to a greater capacity for performing maneuvers, reaching higher orbits, and undertaking more ambitious space missions.
Optimizing for Success: Propellant Fraction, Dry Mass, and Payload Mass
Beyond the core variables of the rocket equation, several related concepts play crucial roles in optimizing mass ratio. Propellant fraction is the ratio of propellant mass to the initial total mass of the rocket.
Maximizing propellant fraction involves designing efficient propellant tanks, using high-density propellants, and minimizing structural weight.
Dry mass represents the mass of the rocket without propellant. Minimizing dry mass is paramount to achieving a high mass ratio. This requires utilizing lightweight materials, optimizing structural designs, and reducing the mass of non-essential components.
Payload mass refers to the mass of the satellite, spacecraft, or other cargo that the rocket is intended to deliver. There exists an inherent trade-off between payload mass and achievable delta-v. Increasing payload mass necessitates either increasing the initial mass of the rocket or reducing the amount of propellant carried. This trade-off must be carefully considered during mission planning to ensure that the rocket can deliver its payload to the desired destination while still retaining sufficient maneuvering capability.
Key Concepts and Technologies: Optimizing Rocket Design for Enhanced Mass Ratio
The journey to optimize mass ratio extends beyond the theoretical realm of equations and delves into the practical implementation of innovative technologies and design philosophies. Several crucial concepts play pivotal roles in minimizing a rocket's mass ratio, each presenting unique engineering challenges and trade-offs.
Staging (Multi-stage Rockets)
One of the most effective methods to improve mass ratio is through staging, where a rocket consists of two or more stages, each with its own engines and propellant. Once a stage has exhausted its propellant, it is discarded, reducing the overall mass of the rocket.
This process significantly enhances the rocket's acceleration capabilities and overall performance.
Multi-stage rockets like the Saturn V (used in the Apollo missions) and the Falcon Heavy exemplify this principle.
Each stage is optimized for a specific portion of the flight. Discarding unnecessary mass as the rocket ascends allows the remaining stages to operate more efficiently.
Structural Efficiency: Minimizing the Skeleton
Structural efficiency is paramount to minimizing dry mass. It refers to the ability of the rocket's structure to withstand the stresses of flight while using the least amount of material possible.
This involves utilizing materials with high strength-to-weight ratios, such as aluminum alloys, titanium, and composite materials like carbon fiber reinforced polymers.
Advanced design techniques like isogrid and orthogrid structures are also employed. These techniques optimize the distribution of material to maximize strength while minimizing weight.
Finite Element Analysis (FEA) is critical in these structural designs. FEA is used to model and simulate the stresses on the structure, allowing engineers to identify weak points and optimize the design.
Propellant Density: Packing the Punch
The density of the propellant significantly impacts the size and mass of the propellant tanks. Denser propellants allow for smaller tanks, reducing overall dry mass.
Liquid oxygen (LOX) and kerosene (RP-1) are commonly used propellants due to their relatively high densities and favorable performance characteristics.
However, there are trade-offs. While denser propellants can reduce tank size, they may have lower specific impulse (a measure of engine efficiency), requiring more propellant to achieve the same delta-v.
The choice of propellant is a critical design decision that must consider mission requirements and performance goals.
Rocket Engines: Power and Efficiency
Rocket engines play a critical role through their efficiency and thrust-to-weight ratio. More efficient engines, characterized by higher specific impulse, require less propellant to achieve a given change in velocity.
The thrust-to-weight ratio of the engine determines the rocket's acceleration. Higher thrust-to-weight ratios allow for faster ascents and greater payload capacity.
Advanced engine designs, such as staged combustion cycles and expander cycles, are employed to maximize engine efficiency and performance.
Electric propulsion systems, while offering very high specific impulse, typically have low thrust. They are suitable for long-duration space missions.
Propellant Tanks: Containing the Energy
The design and materials of propellant tanks are crucial for minimizing structural mass. Tanks must be strong enough to withstand the high pressures of the propellant while being as lightweight as possible.
Materials like aluminum alloys and composite materials are commonly used in tank construction.
Thermal insulation is also critical. Effective insulation minimizes propellant boil-off, ensuring that the propellant remains in liquid form during flight. This is particularly important for long-duration missions.
Tank geometry can also play a role. Spherical or cylindrical tanks are typically used to maximize volume while minimizing surface area, reducing the amount of material needed.
Historical Contributions: Pioneering Figures in Mass Ratio Understanding
The bedrock of modern rocketry and space exploration is built upon the theoretical and experimental work of visionary individuals who grappled with the challenge of achieving flight beyond Earth's atmosphere. Understanding and optimizing mass ratio was a critical part of their endeavor. Let's delve into the contributions of four pivotal figures: Konstantin Tsiolkovsky, Robert H. Goddard, Hermann Oberth, and Wernher von Braun.
Konstantin Tsiolkovsky: The Father of Rocketry and the Rocket Equation
Konstantin Eduardovich Tsiolkovsky is rightfully considered the father of theoretical astronautics.
His most significant contribution, the Tsiolkovsky rocket equation (also known as the ideal rocket equation), mathematically describes the relationship between a rocket's change in velocity (delta-v), its exhaust velocity, and its mass ratio.
This equation provided the fundamental framework for understanding how much propellant is required to achieve a given change in velocity.
Tsiolkovsky's work, published in the early 20th century, was groundbreaking, despite being largely theoretical at the time.
He not only conceptualized the physics of rocket propulsion, but also envisioned multistage rockets to overcome the limitations imposed by mass ratio.
His insights highlighted the necessity of minimizing structural mass and maximizing exhaust velocity to achieve efficient spaceflight.
Robert H. Goddard: From Theory to Practical Experimentation
While Tsiolkovsky laid the theoretical groundwork, Robert H. Goddard was instrumental in transforming rocket theory into tangible reality.
Goddard's experiments with liquid-fueled rockets, starting in the 1920s, were crucial in demonstrating the feasibility of achieving high exhaust velocities and controlled rocket flight.
Goddard understood the profound importance of mass ratio in achieving greater altitudes and distances.
His designs incorporated lightweight materials and efficient combustion chambers.
He realized the significance of minimizing the overall mass of the rocket while maximizing the amount of propellant it could carry.
His efforts, though often met with skepticism, paved the way for future advancements in rocket technology.
Hermann Oberth: Mentor and Advocate for Spaceflight
Hermann Oberth, a contemporary of Goddard, was a prominent advocate for spaceflight.
Oberth's influential book, Die Rakete zu den Planetenräumen ("The Rocket into Interplanetary Space"), published in 1923, elucidated the scientific principles behind rocket propulsion and explored the potential of space travel.
Oberth recognized the critical importance of minimizing structural mass.
He emphasized the use of lightweight materials in rocket construction.
He also recognized the potential of staged rockets to improve overall performance by discarding empty stages during flight, effectively improving the mass ratio at each stage.
Oberth's teachings and writings inspired a generation of engineers and scientists.
Wernher von Braun: From V-2 to the Saturn V
Wernher von Braun stands as a towering figure in the history of rocketry and space exploration.
Von Braun, drawing on the work of his predecessors, led the development of the V-2 rocket during World War II and, later, the Saturn V rocket that propelled the Apollo missions to the Moon.
Von Braun's engineering expertise was crucial in translating theoretical concepts into practical, large-scale rocket designs.
He understood the intricate trade-offs involved in optimizing mass ratio, including the balance between payload capacity, propellant volume, and structural integrity.
The Saturn V exemplifies the application of mass ratio principles.
Its multi-stage design, coupled with powerful engines and lightweight materials, enabled it to deliver unprecedented payloads to lunar orbit, showcasing the culmination of decades of research and development.
Organizational Contributions: Agencies Driving Mass Ratio Optimization
The pioneering work of individual scientists and engineers provides the theoretical foundation, but it is the space agencies and organizations worldwide that translate these concepts into tangible launch vehicles and space missions. These entities, often backed by significant governmental or private investment, are the primary drivers of innovation in mass ratio optimization, pushing the boundaries of what is possible in space exploration.
This section explores the specific approaches and achievements of several key players: NASA, ESA, SpaceX, Roscosmos, ISRO, and JAXA. We will examine how each agency strategically addresses the challenges inherent in minimizing mass ratio to achieve ambitious mission objectives.
NASA: A Legacy of Optimized Launch Systems
The National Aeronautics and Space Administration (NASA) has a long and storied history of optimizing mass ratio in its launch vehicle designs. From the Saturn V, a marvel of engineering that enabled the Apollo missions to reach the Moon, to the Space Shuttle, NASA has consistently pushed the boundaries of what is achievable.
NASA's approach involves a comprehensive system-level perspective, considering every component from engine efficiency to structural integrity. Their emphasis on rigorous testing and validation has yielded valuable insights into the complex interplay of factors affecting mass ratio. Ongoing projects like the Space Launch System (SLS) continue this tradition, aiming to deliver unprecedented payload capacity for deep-space exploration.
ESA: Balancing Performance and International Collaboration
The European Space Agency (ESA) has distinguished itself through a commitment to robust and reliable launch systems, often developed through international collaborations. The Ariane series of launchers, a cornerstone of ESA's program, exemplifies this approach.
ESA's focus extends beyond raw performance, emphasizing cost-effectiveness and environmental considerations. Through meticulous design and advanced materials, ESA strives to optimize the trade-offs between payload capacity and overall launch system efficiency. This approach has allowed Europe to maintain a competitive edge in the global space launch market.
SpaceX: Revolutionizing Access to Space Through Reusability
SpaceX has disrupted the space industry with its innovative approach to rocketry, particularly in the area of reusable rocket technology. The Falcon 9, with its partially reusable first stage, dramatically reduces launch costs by recovering and reusing a significant portion of the vehicle.
This reusability is intrinsically linked to mass ratio. By designing the first stage for recovery, SpaceX has accepted a mass penalty in terms of additional structure and propellant for landing maneuvers. However, the economic benefits of reuse far outweigh this penalty, demonstrating a fundamentally different approach to mass ratio optimization. The Starship program aims to take this concept even further with fully reusable stages.
Roscosmos: Leveraging Heritage and Reliability
Roscosmos, the Russian space agency, boasts a rich history in rocketry, tracing its roots back to the earliest days of space exploration. The Soyuz rocket, a remarkably reliable and cost-effective launch vehicle, is a testament to this legacy.
Roscosmos has focused on incremental improvements and proven technologies to maintain the Soyuz's competitive edge. While not necessarily pushing the boundaries of innovation in the same way as some other agencies, Roscosmos continues to play a vital role in providing reliable access to space. Their designs emphasize structural efficiency and propellant management to maximize payload capacity within established parameters.
ISRO: Cost-Effective Solutions for Space Access
The Indian Space Research Organisation (ISRO) has gained international recognition for its ability to deliver cost-effective solutions for space access. ISRO's launch vehicles, such as the Polar Satellite Launch Vehicle (PSLV) and the Geosynchronous Satellite Launch Vehicle (GSLV), are designed with a focus on affordability and indigenous technology.
ISRO's approach to mass ratio optimization involves a strategic blend of proven technologies and innovative design concepts. By carefully selecting materials and optimizing structural design, ISRO has consistently achieved impressive payload capacities at relatively low costs. Their success highlights the importance of resourcefulness and ingenuity in achieving optimal mass ratio.
JAXA: Advanced Technologies and Scientific Missions
The Japan Aerospace Exploration Agency (JAXA) distinguishes itself through its focus on advanced technologies and ambitious scientific missions. JAXA's launch vehicles, such as the H-IIA and H3, are designed to support a wide range of missions, including Earth observation, planetary exploration, and space science.
JAXA's approach to mass ratio optimization involves a combination of advanced materials, efficient engine designs, and sophisticated control systems. They also emphasize the development of innovative propulsion technologies, such as ion engines, which offer extremely high exhaust velocities, albeit at low thrust levels. These technologies are particularly well-suited for long-duration missions to distant destinations.
Launch Vehicle Examples: Real-World Applications of Mass Ratio Principles
Organizational Contributions: Agencies Driving Mass Ratio Optimization The pioneering work of individual scientists and engineers provides the theoretical foundation, but it is the space agencies and organizations worldwide that translate these concepts into tangible launch vehicles and space missions. These entities, often backed by significant governmental resources, are at the forefront of implementing and refining mass ratio principles in practical rocket designs. By analyzing several prominent launch vehicles, we can see these principles put to the test.
Saturn V: A Monument to Mass Ratio Engineering
The Saturn V, the behemoth that propelled the Apollo missions to the Moon, serves as an excellent example of the application of mass ratio principles.
Its sheer size underscored the necessity of efficient staging and meticulous material selection.
The three-stage design allowed for the sequential discarding of empty fuel tanks and engines, dramatically improving the overall mass ratio as the rocket ascended.
Each stage was powered by powerful engines optimized for their specific atmospheric conditions, ensuring maximum thrust and fuel efficiency.
The first stage alone burned through over 2,000 tons of propellant in just 2.5 minutes, a testament to the immense energy required to escape Earth's gravity.
The Saturn V represents a high watermark in chemical rocket engineering, showcasing how careful attention to mass ratio can enable seemingly impossible feats.
Falcon 9: Reusability and Mass Efficiency
SpaceX's Falcon 9 represents a paradigm shift in rocketry, emphasizing reusability as a means of reducing launch costs.
While reusability introduces its own set of challenges in terms of structural reinforcement and landing systems, SpaceX has made significant strides in optimizing the Falcon 9's mass ratio.
The first stage's ability to return to Earth for subsequent missions reduces the effective dry mass of the overall system, improving the mass ratio from a mission perspective.
The use of lightweight materials, advanced manufacturing techniques, and optimized engine designs contribute to the vehicle's overall efficiency.
Furthermore, SpaceX's iterative design process allows for continuous improvements to the Falcon 9, further refining its mass ratio and performance capabilities.
Ariane 5: A Workhorse for European Space Access
The Ariane 5, developed by the European Space Agency (ESA), is a versatile launch vehicle known for its reliability and heavy-lift capabilities.
While not fully reusable like the Falcon 9, the Ariane 5 incorporates several design features to optimize its mass ratio.
The use of a cryogenic upper stage, powered by a high-performance engine, enables efficient delivery of payloads to a variety of orbits.
The solid rocket boosters (SRBs) provide significant thrust during the initial ascent, augmenting the core stage's engines and improving the overall lift capacity.
By carefully balancing the performance characteristics of each stage, the Ariane 5 achieves a favorable mass ratio that allows it to compete effectively in the global launch market.
Soyuz: A Legacy of Reliability and Refinement
The Soyuz rocket, with its long and storied history, represents a testament to the power of incremental design improvements.
While the basic design has remained relatively consistent over the decades, the Soyuz has undergone numerous upgrades to enhance its performance and reliability.
These refinements have included the use of lighter materials, more efficient engines, and improved control systems.
The Soyuz's simple yet robust design contributes to its high reliability and relatively low cost of operation.
Its multi-stage configuration allows for the efficient disposal of spent stages, improving the overall mass ratio and enabling a wide range of missions.
The Soyuz serves as a reminder that even mature rocket designs can benefit from continuous optimization of mass ratio and other key performance parameters.
As each of these examples has demonstrated, the mass ratio is not merely a theoretical calculation. It is the linchpin to unlocking capabilities in space. The ongoing work in optimizing mass ratio and reusability ensures humanity's continued access to space.
Video: Mass Ratio: Rocketry Explained | Formula & Examples
FAQs: Mass Ratio in Rocketry
What does a higher mass ratio mean for a rocket?
A higher mass ratio indicates a more efficient rocket. This means the rocket carries more propellant relative to its dry mass (the mass without propellant). A higher mass ratio allows the rocket to achieve a greater change in velocity (delta-v), enabling it to reach higher orbits or travel further distances.
How does the mass ratio relate to rocket performance?
The mass ratio is a key factor in determining a rocket's overall performance. It directly influences the rocket's delta-v, which is the total change in velocity the rocket can achieve. A larger mass ratio results in a greater delta-v, allowing the rocket to perform more demanding maneuvers or reach destinations further away.
Why is dry mass important when considering mass ratio?
The dry mass is a crucial component of the mass ratio because it represents the weight of the rocket without propellant. Minimizing the dry mass is essential for improving the mass ratio. A lower dry mass means more of the rocket's total mass can be dedicated to propellant, enhancing its performance.
Is there a "good" mass ratio value for a rocket?
There isn't one specific "good" mass ratio, as the ideal value depends on the mission requirements. However, a higher mass ratio is generally desirable. Practical rockets often have mass ratios between 10:1 and 20:1, but achieving significantly higher ratios is challenging due to structural and technological limitations.
So, there you have it! Mass ratio might seem intimidating at first, but with a little understanding, you can start to appreciate its central role in getting rockets off the ground. Hopefully, this has demystified the concept and shown you how crucial a high mass ratio is for achieving those ambitious spacefaring goals. Now you're equipped to think like a rocket scientist, at least when it comes to understanding this key parameter!