Magnesium Nitride: Uses, Benefits, & Safety
Magnesium nitride, a chemical compound represented by the formula Mg3N2, exhibits a range of applications and properties that are increasingly relevant in modern materials science. The substance's formation results from direct reaction between magnesium, a Group 2 element, and nitrogen gas, a common atmospheric component. Industries focused on high-performance ceramics often utilize magnesium nitride because the material demonstrates high thermal stability. Safety measures are essential when handling magnesium nitride because this compound reacts with water, producing ammonia, a potentially hazardous gas, thus necessitating controlled environments and careful handling procedures.
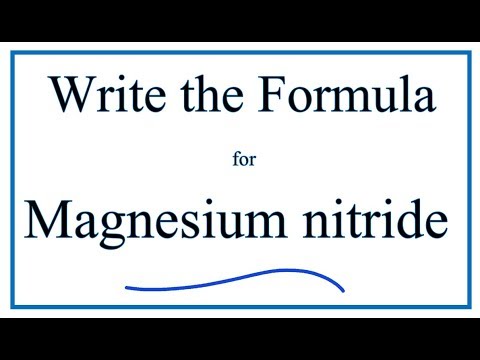
Image taken from the YouTube channel Wayne Breslyn (Dr. B.) , from the video titled How to Write the Formula for Magnesium nitride .
Magnesium nitride, represented by the chemical formula Mg3N2, is a chemical compound comprised of magnesium and nitrogen.
It stands as a testament to the diverse functionalities achievable through solid-state chemistry.
This compound, while perhaps not as widely recognized as other metal nitrides, possesses a unique combination of properties that render it valuable across a spectrum of applications.
Defining Magnesium Nitride
Magnesium nitride is an inorganic compound formed through the direct combination of magnesium and nitrogen. Its chemical formula, Mg3N2, indicates that three magnesium atoms are bonded with two nitrogen atoms in its crystal lattice.
Properties at a Glance
Mg3N2 exhibits several notable properties:
-
It's a solid at room temperature.
-
It possesses a relatively high melting point.
-
Perhaps most significantly, it reacts with water in a process called hydrolysis, releasing ammonia gas. This reactivity plays a crucial role in some of its applications.
Applications: A Brief Overview
The applications of magnesium nitride are varied and continue to expand as research delves deeper into its potential. Traditionally, it has found use as:
-
A source of nitrogen in specific chemical reactions.
-
An additive in the production of high-strength alloys.
-
A component in certain high-temperature ceramics.
Emerging research is exploring its suitability for:
-
Hydrogen storage.
-
Advanced electronic materials.
The Significance in Materials Science and Solid-State Chemistry
Magnesium nitride's importance within materials science stems from its ability to impart specific characteristics to other materials, particularly in contexts requiring high-temperature stability or controlled chemical reactivity.
Its behavior also offers insights into the broader field of solid-state chemistry, specifically regarding the interactions between metals and non-metals at an atomic level. The study of Mg3N2 contributes to a better understanding of:
-
Crystal structure formation.
-
Thermodynamic properties of inorganic compounds.
-
The synthesis of new materials with tailored functionalities.
Therefore, magnesium nitride serves not only as a functional material in its own right, but also as a valuable model for investigating fundamental principles in materials science and solid-state chemistry.
Synthesizing Magnesium Nitride: Methods and Considerations
Magnesium nitride, represented by the chemical formula Mg3N2, is a chemical compound comprised of magnesium and nitrogen. It stands as a testament to the diverse functionalities achievable through solid-state chemistry. This compound, while perhaps not as widely recognized as other metal nitrides, possesses a unique combination of properties that necessitates careful consideration during its synthesis. The methods employed directly impact the purity, yield, and ultimately, the suitability of the resulting magnesium nitride for various applications.
Direct Reaction of Magnesium and Nitrogen
The most common and straightforward method for synthesizing magnesium nitride involves the direct reaction of elemental magnesium with nitrogen gas. This process, while conceptually simple, requires precise control over reaction parameters to ensure a high-quality product.
Reaction Conditions: Temperature, Pressure, and Inert Atmosphere
The reaction between magnesium and nitrogen is highly sensitive to temperature and pressure. Elevated temperatures, typically ranging from 700°C to 900°C, are required to initiate and sustain the reaction. The pressure of the nitrogen atmosphere also plays a critical role. While the reaction can occur at atmospheric pressure, higher pressures generally promote a more complete conversion of magnesium to magnesium nitride.
Crucially, an inert atmosphere is essential to prevent unwanted side reactions. Oxygen and moisture can react with magnesium to form magnesium oxide and magnesium hydroxide, respectively, contaminating the final product. Argon or other inert gases are therefore commonly used as a protective environment.
The Role of Nitrogen Gas (N2)
The purity and flow rate of the nitrogen gas are also critical factors. Impurities such as oxygen or water vapor can hinder the reaction and introduce unwanted byproducts. A consistent flow of nitrogen ensures that the reaction atmosphere remains free of contaminants and that the reaction proceeds efficiently. Higher purity nitrogen (99.999%) is generally preferred for achieving optimal results.
Use of Furnaces
The synthesis is typically carried out in specialized furnaces designed for high-temperature reactions under controlled atmospheres. These furnaces often incorporate features such as precise temperature control, gas flow regulation, and safety interlocks to ensure consistent and safe operation.
Alternative Synthesis Routes
While the direct reaction of magnesium and nitrogen is the most prevalent method, alternative synthesis routes offer potential advantages in specific scenarios.
Reaction with Ammonia (NH3)
Magnesium nitride can also be synthesized by reacting magnesium with ammonia gas at elevated temperatures. This method offers an alternative to using elemental nitrogen and can sometimes provide a more controlled reaction environment. However, care must be taken to manage the byproduct hydrogen gas, which is flammable.
Considerations for Magnesium Oxide (MgO) as a Reactant/Byproduct
In some synthesis routes, magnesium oxide (MgO) may be present as either a reactant or a byproduct. The presence of MgO can complicate the reaction and potentially lead to a lower purity product. Strategies for mitigating the formation of MgO include carefully controlling the reaction atmosphere and using high-purity magnesium as a starting material.
The Chemical Synthesis Process in Detail
The chemical synthesis process, regardless of the specific method employed, involves a nitridation process.
Nitridation Process Explained
Nitridation refers to the chemical process of introducing nitrogen into a material. In the case of magnesium nitride synthesis, the nitridation process involves the reaction of elemental magnesium with nitrogen to form magnesium nitride. The reaction proceeds through a series of steps, including:
- Adsorption of nitrogen molecules onto the surface of the magnesium.
- Dissociation of nitrogen molecules into nitrogen atoms.
- Diffusion of nitrogen atoms into the magnesium lattice.
- Formation of magnesium nitride at the magnesium-nitrogen interface.
The rate and efficiency of the nitridation process are strongly influenced by the reaction conditions, including temperature, pressure, and the presence of impurities. Understanding and controlling these factors are crucial for achieving a successful synthesis of high-quality magnesium nitride.
Properties of Magnesium Nitride: A Detailed Exploration
Magnesium nitride, represented by the chemical formula Mg3N2, is a chemical compound comprised of magnesium and nitrogen. It stands as a testament to the diverse functionalities achievable through solid-state chemistry. This compound, while perhaps not as widely recognized as other metal nitrides, possesses a unique combination of physical and chemical attributes that render it suitable for various high-performance applications. To fully leverage its potential, a deep understanding of its intrinsic properties is essential.
Physical Properties: Foundation of Performance
The physical characteristics of magnesium nitride form the bedrock upon which its applications are built. These properties dictate its behavior under different conditions and its compatibility with various processing techniques.
Crystal Structure: Implications for Material Behavior
Magnesium nitride adopts an antifluorite crystal structure. In this structure, the magnesium atoms occupy the fluoride ion positions, while the nitrogen atoms occupy the calcium ion positions.
This arrangement is significant because it influences the compound's mechanical strength, thermal expansion, and other critical material properties. The rigid, three-dimensional network contributes to its overall stability and resistance to deformation.
Thermal Properties: Withstanding High Temperatures
Magnesium nitride boasts a high melting point, making it suitable for applications in high-temperature environments. This thermal stability is a direct consequence of the strong chemical bonds between magnesium and nitrogen atoms within its crystal lattice.
This characteristic allows it to maintain its structural integrity and functionality even when exposed to extreme heat, making it an attractive option for applications in aerospace, metallurgy, and advanced ceramics.
Chemical Properties: Reactivity and Composition
The chemical properties of magnesium nitride govern its interactions with other substances and its overall stability in various chemical environments. Understanding these characteristics is vital for ensuring safe handling and optimal performance.
Reactivity with Water: Hydrolysis and Byproduct Formation
One of the most notable chemical properties of magnesium nitride is its reactivity with water. Magnesium nitride undergoes hydrolysis when exposed to moisture, yielding magnesium hydroxide (Mg(OH)2) and ammonia (NH3) as byproducts.
This reaction is often represented by the following equation:
Mg3N2(s) + 6H2O(l) → 3Mg(OH)2(aq) + 2NH3(g)
This hydrolysis reaction necessitates careful handling and storage of magnesium nitride to prevent unwanted degradation and the release of ammonia gas. Controlled environments with low humidity are often required to maintain its integrity.
Stoichiometry: Molar Mass and Compositional Integrity
The stoichiometry of magnesium nitride, as represented by the formula Mg3N2, indicates a fixed ratio of magnesium and nitrogen atoms. This fixed ratio translates to a specific molar mass, which is crucial for precise calculations in chemical reactions and material formulations.
Maintaining this stoichiometry is vital for achieving the desired properties and performance characteristics. Deviations from the ideal ratio can lead to changes in its crystal structure, chemical reactivity, and overall stability.
Flammability and Handling: Prioritizing Safety
While magnesium nitride itself is not inherently flammable, the hydrogen gas produced from its reaction with water is highly flammable.
The fine powder form of magnesium nitride poses an increased risk due to the large surface area available for reaction.
Proper handling procedures, including the use of inert atmospheres and personal protective equipment (PPE), are essential to minimize risks. Adequate ventilation is also necessary to prevent the accumulation of ammonia gas, which can be toxic at high concentrations. A thorough understanding of the relevant Safety Data Sheet (SDS) and adherence to Globally Harmonized System (GHS) guidelines are paramount for ensuring safe handling and storage practices.
Applications of Magnesium Nitride: A Diverse Range
Magnesium nitride, represented by the chemical formula Mg3N2, is a chemical compound comprised of magnesium and nitrogen. It stands as a testament to the diverse functionalities achievable through solid-state chemistry. This compound, while perhaps not as widely recognized as other metal nitrides, boasts a surprising array of applications stemming from its unique properties. Let's explore these applications in more detail.
High-Temperature Applications
Magnesium nitride finds utility in high-temperature environments due to its thermal stability and resistance to decomposition at elevated temperatures.
This characteristic makes it suitable for components in high-temperature furnaces, aerospace applications, and other demanding settings.
Its ability to maintain structural integrity and chemical inertness at high temperatures is a key advantage in such applications.
Use as a Nitrogen Source
Mg3N2 serves as a valuable nitrogen source in various chemical processes.
When heated, it decomposes to release nitrogen gas, which can then be utilized in nitriding processes or other chemical reactions requiring a controlled nitrogen atmosphere.
This controlled release of nitrogen makes it a superior alternative to directly introducing nitrogen gas in some applications.
Component in Advanced Ceramics
The integration of magnesium nitride into advanced ceramics enhances their mechanical properties and high-temperature performance.
It can improve the hardness, strength, and wear resistance of ceramic materials, making them suitable for structural components, cutting tools, and wear-resistant coatings.
The resulting composite materials exhibit enhanced durability and longevity in demanding environments.
Use in Metallurgy as an Additive
In metallurgy, magnesium nitride functions as an additive to refine grain size and improve the mechanical properties of metals.
The addition of small amounts of Mg3N2 can lead to enhanced strength, ductility, and toughness in the resulting alloy.
This is particularly beneficial in the production of high-performance alloys for aerospace, automotive, and other engineering applications.
Research and Development
Magnesium nitride continues to be a subject of ongoing research and development.
Scientists are exploring its potential use in new materials and technologies, including energy storage, catalysis, and electronic devices.
The unique properties of Mg3N2, such as its high nitrogen content and reactivity, make it a promising candidate for these emerging applications.
Handling and Safety Precautions: Minimizing Risks
Magnesium nitride, represented by the chemical formula Mg3N2, is a chemical compound comprised of magnesium and nitrogen. It stands as a testament to the diverse functionalities achievable through solid-state chemistry. This compound, while perhaps not as widely recognized as other metal nitrides, presents unique handling challenges due to its reactivity. Therefore, a thorough understanding of its properties and the implementation of stringent safety measures are paramount when working with this material.
The Necessity of Inert Atmospheres
Magnesium nitride reacts readily with moisture in the air, leading to the formation of magnesium hydroxide and ammonia. This reaction, known as hydrolysis, can be represented as follows:
Mg3N2(s) + 6H2O(l) → 3Mg(OH)2(s) + 2NH3(g)
The production of ammonia gas not only poses a respiratory hazard but also indicates the degradation of the material. To prevent this unwanted reaction, handling magnesium nitride under an inert atmosphere, such as argon or nitrogen, is crucial. This mitigates the risk of hydrolysis and ensures the integrity of the compound for its intended use.
Essential Personal Protective Equipment (PPE)
Given the potential hazards associated with magnesium nitride, the use of appropriate personal protective equipment (PPE) is non-negotiable. At a minimum, the following PPE should be worn:
- Safety glasses or goggles: To protect the eyes from particulate matter and potential chemical splashes.
- Gloves: Impervious to chemicals and moisture to prevent skin contact and absorption. Nitrile or neoprene gloves are generally suitable.
- Lab coat or apron: To shield clothing and skin from contamination.
- Respirator: If there is a risk of airborne dust or ammonia exposure, a respirator with appropriate filters should be used.
Understanding Potential Toxicity and Hazards
While the toxicity of magnesium nitride has not been extensively studied, its reactivity with water to produce ammonia warrants caution. Ammonia is a toxic gas that can cause irritation to the eyes, skin, and respiratory tract.
Prolonged or high-level exposure can lead to more severe health effects. Therefore, avoiding inhalation and direct contact with magnesium nitride is essential.
Safe Storage Conditions: Maintaining Stability
The storage of magnesium nitride requires careful consideration to prevent degradation. It should be stored in a tightly sealed container in a cool, dry place, away from sources of moisture and heat. The container should be clearly labeled with appropriate hazard warnings.
Desiccators or glove boxes with an inert atmosphere are ideal for long-term storage.
Reviewing the Safety Data Sheet (SDS)
The Safety Data Sheet (SDS) is a comprehensive resource that provides detailed information about the hazards, safe handling procedures, and emergency measures for magnesium nitride. Before working with the compound, it is imperative to thoroughly review the SDS. This document contains critical information such as:
- Physical and chemical properties.
- Hazard identification.
- First aid measures.
- Firefighting measures.
- Accidental release measures.
- Exposure controls and personal protection.
- Stability and reactivity.
- Toxicological information.
- Ecological information.
- Disposal considerations.
Adhering to the GHS (Globally Harmonized System)
The Globally Harmonized System (GHS) provides a standardized approach to hazard communication, including the labeling of chemicals and the preparation of SDSs. Adhering to the GHS guidelines ensures that all hazards associated with magnesium nitride are clearly communicated to users. This includes the use of pictograms, signal words (e.g., "Danger" or "Warning"), and hazard statements to convey the potential risks. Understanding and implementing GHS principles is vital for maintaining a safe working environment.
Processing Techniques for Magnesium Nitride: Achieving Desired Forms
Magnesium nitride, represented by the chemical formula Mg3N2, is a chemical compound comprised of magnesium and nitrogen. It stands as a testament to the diverse functionalities achievable through solid-state chemistry. This compound, while perhaps not as widely recognized as other metal nitrides, presents unique challenges and opportunities in materials processing due to its reactivity and sensitivity to atmospheric conditions. Achieving desired forms and microstructures of Mg3N2 necessitates the use of specialized techniques, primarily sintering and handling within controlled environments such as glove boxes.
Sintering: Consolidating Magnesium Nitride Powders
Sintering is a crucial process for consolidating Mg3N2 powders into dense, coherent bodies. This process involves heating the powder compact to a high temperature, below its melting point, to induce solid-state diffusion and bonding between particles. The goal is to reduce porosity and increase the mechanical strength of the final product.
Several sintering techniques can be employed for Mg3N2, each with its advantages and disadvantages:
-
Conventional Sintering: This is the most basic method, involving heating the powder compact in a furnace under a controlled atmosphere. The atmosphere is critical to prevent oxidation or decomposition of the Mg3N2.
-
Hot Pressing: This technique applies pressure during the sintering process. The applied pressure enhances densification and reduces the sintering temperature, leading to a finer microstructure and improved mechanical properties. This is particularly beneficial for Mg3N2 as it minimizes grain growth and decomposition.
-
Spark Plasma Sintering (SPS): SPS, also known as Field-Assisted Sintering Technique (FAST), utilizes pulsed DC current to generate localized heating at the particle contacts. This rapid heating rate significantly reduces the sintering time and temperature, resulting in dense materials with minimal grain growth. SPS is well-suited for Mg3N2 due to its ability to achieve high densities in short periods.
The sintering temperature, pressure (if applicable), and atmosphere must be carefully controlled to optimize the densification process and prevent unwanted reactions or decomposition. For instance, sintering in a nitrogen atmosphere can help suppress the decomposition of Mg3N2.
Glove Boxes: Maintaining Controlled Environments
Magnesium nitride is highly reactive with moisture and oxygen, readily undergoing hydrolysis and oxidation. Therefore, processing Mg3N2 requires strict control over the surrounding atmosphere. Glove boxes, also known as dry boxes, provide a sealed environment filled with an inert gas, such as argon or nitrogen, with very low levels of oxygen and water vapor.
Importance of Inert Atmosphere
Inside a glove box, Mg3N2 powders can be handled, mixed, and compacted without the risk of degradation. All equipment and tools used within the glove box must be compatible with the controlled atmosphere and thoroughly cleaned to remove any contaminants.
Glove Box Operation
Proper operation and maintenance of the glove box are essential for maintaining the integrity of the controlled environment. This includes regularly monitoring the oxygen and moisture levels, replacing gas filters, and following strict protocols for introducing and removing materials from the glove box. Any breach in the glove box seal can lead to contamination and compromise the quality of the Mg3N2 being processed.
Applications of Glove Boxes in Mg3N2 Processing
Glove boxes are not only used for handling powders but also for performing other processing steps such as mixing with additives, pressing into green bodies, and even for conducting certain types of sintering experiments on a small scale. By minimizing exposure to reactive elements, glove boxes ensure the purity and stability of Mg3N2 during processing, leading to materials with superior properties.
Characterization Techniques: Unveiling Magnesium Nitride's Structure and Properties
Understanding the fundamental characteristics of magnesium nitride (Mg3N2) requires the application of sophisticated characterization techniques. These methods allow researchers to probe the compound's crystal structure, morphology, and thermal behavior, providing critical insights into its potential applications.
The data obtained through these techniques is essential for correlating synthesis parameters with the resulting material properties. Ultimately this knowledge is crucial for optimizing performance in diverse applications.
X-ray Diffraction (XRD): Determining Crystal Structure
X-ray Diffraction (XRD) is a cornerstone technique for elucidating the crystalline structure of magnesium nitride. By bombarding the sample with X-rays and analyzing the diffraction pattern, researchers can determine the arrangement of atoms within the material.
The peak positions in the XRD pattern correspond to specific interplanar spacings within the crystal lattice. This is governed by Bragg's Law. The intensity of the peaks is related to the degree of crystallinity and preferred orientation.
Phase identification, lattice parameter determination, and crystallite size estimation are all achievable through careful analysis of the XRD data. Deviations from the ideal diffraction pattern can indicate the presence of defects, strain, or secondary phases. This ensures that a pure Mg3N2 phase has been successfully synthesized.
Scanning Electron Microscopy (SEM): Imaging Microstructure
Scanning Electron Microscopy (SEM) provides high-resolution images of the surface morphology of magnesium nitride. SEM allows for the visualization of grain size, shape, and distribution. It also reveals the presence of pores or other microstructural features.
In SEM, a focused beam of electrons scans the surface of the sample. The resulting secondary electrons are detected to create an image.
Energy-dispersive X-ray spectroscopy (EDS) can be coupled with SEM to provide elemental composition information. This enables the identification of any impurities or variations in stoichiometry across the sample. SEM is particularly useful for assessing the homogeneity and density of Mg3N2 powders or sintered compacts.
Transmission Electron Microscopy (TEM): Analyzing Atomic Structure
Transmission Electron Microscopy (TEM) offers even higher resolution capabilities compared to SEM. TEM allows for the direct observation of the atomic structure of magnesium nitride.
In TEM, a beam of electrons is transmitted through a very thin sample. The resulting diffraction pattern and image provide information on the crystal structure, defects, and interfaces at the atomic scale.
High-resolution TEM (HRTEM) can reveal the arrangement of individual atoms. Selected area electron diffraction (SAED) provides information on the crystallinity and orientation of the sample. TEM is indispensable for studying nanoscale features and defects in Mg3N2. This is especially important for the development of advanced materials with tailored properties.
Differential Thermal Analysis (DTA) / Differential Scanning Calorimetry (DSC): Studying Thermal Properties
Differential Thermal Analysis (DTA) and Differential Scanning Calorimetry (DSC) are thermal analysis techniques that provide information on the thermal behavior of magnesium nitride as a function of temperature.
DTA measures the temperature difference between the sample and an inert reference material as they are heated or cooled. DSC measures the heat flow into or out of the sample compared to the reference.
These techniques can identify phase transitions, melting points, and decomposition temperatures. DTA/DSC data are crucial for assessing the thermal stability of Mg3N2. They also inform its suitability for high-temperature applications. Endothermic and exothermic peaks in the DTA/DSC curves provide valuable insights into the thermal events occurring within the material. Understanding thermal properties is essential for predicting the behavior of Mg3N2 under operating conditions.
Potential Concerns and Limitations: Addressing Challenges
Characterization Techniques: Unveiling Magnesium Nitride's Structure and Properties Understanding the fundamental characteristics of magnesium nitride (Mg3N2) requires the application of sophisticated characterization techniques. These methods allow researchers to probe the compound's crystal structure, morphology, and thermal behavior, providing c...
Despite its promising attributes, magnesium nitride is not without its drawbacks. Addressing these limitations is crucial for unlocking its full potential and ensuring its reliable application in various technological domains.
This section will explore key concerns, specifically focusing on environmental sensitivities and degradation mechanisms.
Environmental Sensitivity: Corrosion and Hydrolysis
Magnesium nitride exhibits a notable sensitivity to certain environmental conditions, particularly those involving moisture. The primary concern stems from its reactivity with water, leading to corrosion and the release of ammonia.
Hydrolytic Decomposition
The reaction of magnesium nitride with water (hydrolysis) is a well-documented phenomenon. This process results in the formation of magnesium hydroxide (Mg(OH)2) and ammonia gas (NH3).
The chemical equation representing this reaction is:
Mg3N2 (s) + 6H2O (l) → 3Mg(OH)2 (s) + 2NH3 (g)
This reaction can be problematic in humid environments. The production of ammonia is not only corrosive but also poses a potential health hazard if not properly ventilated.
Mitigation Strategies
To mitigate the hydrolytic decomposition of magnesium nitride, several strategies can be employed:
- Protective Coatings: Applying hydrophobic coatings can create a barrier between the magnesium nitride and moisture.
- Controlled Environments: Storing and handling magnesium nitride in dry, inert atmospheres minimizes exposure to water vapor.
- Material Composition Modifications: Alloying magnesium nitride with other elements may improve its resistance to hydrolysis, although this may affect its other beneficial properties.
Degradation at Elevated Temperatures
While magnesium nitride is considered a high-temperature material, it can still experience degradation under extreme thermal conditions, particularly in reactive atmospheres.
Decomposition Kinetics
At sufficiently high temperatures, magnesium nitride can decompose into its constituent elements, magnesium and nitrogen.
The rate of this decomposition depends on factors such as temperature, pressure, and the surrounding atmosphere. The presence of oxygen or other reactive gases can accelerate the degradation process.
Loss of Nitrogen
The loss of nitrogen from the material can alter its stoichiometry and degrade its structural integrity. This is particularly relevant in applications where precise control over the material's composition is required.
Improving Thermal Stability
Several approaches can be considered to improve the thermal stability of magnesium nitride:
- Optimizing Sintering Processes: Careful control of sintering parameters can reduce the concentration of defects and improve the material's resistance to decomposition.
- Adding Stabilizing Elements: Introducing dopants or alloying elements can enhance the thermal stability by modifying the material's electronic structure.
- Protective Atmospheres: Utilizing inert or reducing atmospheres during high-temperature processing can minimize the loss of nitrogen.
Future Research Directions
Addressing the corrosion and degradation issues associated with magnesium nitride requires ongoing research and development efforts.
Future research should focus on:
- Developing novel protective coatings that offer long-term protection against moisture and reactive gases.
- Investigating the effects of different alloying elements on the hydrolytic and thermal stability of magnesium nitride.
- Exploring new synthesis and processing techniques that can produce magnesium nitride materials with improved resistance to degradation.
Overcoming these challenges will pave the way for broader adoption of magnesium nitride in advanced technological applications.
Video: Magnesium Nitride: Uses, Benefits, & Safety
Frequently Asked Questions About Magnesium Nitride
What is magnesium nitride primarily used for?
Magnesium nitride is mainly used as a chemical reagent in various research and industrial applications. A primary application is in the synthesis of other nitrides. It's also investigated for potential use in hydrogen storage.
What are the benefits of using magnesium nitride?
Magnesium nitride offers benefits like acting as a source of pure nitrogen in chemical reactions. Its reaction with water produces ammonia, which can be useful in specific processes. Researchers are still investigating potential benefits in material science.
Is magnesium nitride dangerous to handle?
Magnesium nitride can be irritating to the skin, eyes, and respiratory tract. It reacts with water to produce ammonia, a toxic gas. Proper handling procedures, including personal protective equipment and ventilation, are necessary when working with magnesium nitride.
How should magnesium nitride be stored safely?
Magnesium nitride should be stored in a cool, dry place, away from moisture and incompatible materials. Due to its reactivity with water, airtight containers are essential to prevent the formation of ammonia gas. Proper labeling is also critical for safety.
So, there you have it! Magnesium nitride is a pretty interesting compound with a surprising number of uses, from creating strong materials to playing a role in nitrogen fixation. While it’s not exactly a household name, understanding its benefits and being aware of the safety precautions makes a real difference if you ever encounter it in industrial settings or research. Just remember to handle magnesium nitride with care, and you'll be good to go!