Induction Helps Heat Tran: Efficiency Guide
Induction heating systems, leveraged across industries from automotive manufacturing to commercial food service, depend on the principles of electromagnetic induction. These systems, which can be optimized through techniques detailed by organizations such as the American Induction Heating Society, offer precise and rapid heating capabilities. The efficiency of induction heating is often measured using specialized tools like thermal imaging cameras to detect heat distribution and losses. This level of control that induction heating provides makes it an appealing alternative to traditional heating methods in processes that can be optimized for heat transfer through induction. By focusing on key factors such as frequency and coil design, induction helps in heat tran with improvements to the speed and effectiveness of heating processes, especially those involving materials with high magnetic permeability.
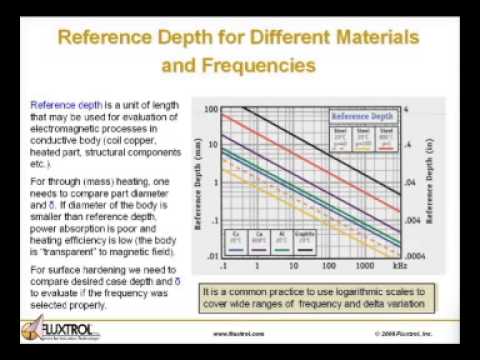
Image taken from the YouTube channel Fluxtrol , from the video titled Power Transfer Factor In Induction Heating .
Unveiling the Power of Induction Heating: A Modern Marvel
Induction heating stands as a testament to the power of harnessing electromagnetic principles for efficient and precise heating. It is a process where an electrically conductive material is heated through electromagnetic induction, a method vastly different from traditional heating approaches.
But what exactly is induction heating, and how does it work?
The Fundamental Principle Explained
At its core, induction heating operates on the principle of electromagnetic induction, discovered by Michael Faraday. An alternating current (AC) is passed through a coil, creating a fluctuating magnetic field around it.
When a conductive material is placed within this magnetic field, it experiences a changing magnetic flux. This changing flux induces a voltage within the material, which in turn drives circulating electrical currents known as eddy currents.
These eddy currents flow through the resistance of the material, generating heat. The amount of heat generated is proportional to the square of the current and the resistance of the material (I²R).
Thus, induction heating achieves direct, internal heating of the workpiece without direct contact.
Induction Heating vs. Traditional Methods: A Comparative Analysis
Compared to conventional heating methods like resistance heating or gas furnaces, induction heating offers several distinct advantages:
- Efficiency: Induction heating boasts significantly higher energy efficiency. This is because energy is directly transferred to the workpiece, minimizing heat loss to the surrounding environment.
- Speed: The rapid generation of heat within the material allows for exceptionally fast heating cycles. This accelerates production processes and reduces overall energy consumption.
- Localized Heating: The heating effect can be precisely targeted to specific areas of the workpiece. This is crucial for applications requiring localized heat treatment or joining processes.
- Cleanliness: As a flameless process, induction heating produces no combustion byproducts, contributing to a cleaner and safer working environment.
- Repeatability: Induction heating systems are easily automated and controlled, ensuring consistent and repeatable results for every heating cycle.
Traditional heating methods often suffer from lower efficiency due to heat loss, slower heating rates, and difficulty in achieving precise temperature control. These limitations make them less suitable for many modern industrial applications where precision and efficiency are paramount.
A Glimpse into the Diverse Applications of Induction Heating
The versatility of induction heating has made it an indispensable technology across numerous industries. From the automotive sector to aerospace and beyond, its applications are vast and varied.
- In heat treating, it is used to harden, temper, or anneal metal components, enhancing their mechanical properties.
- In the automotive industry, induction heating is employed for surface hardening of engine parts, improving wear resistance.
- The aerospace industry utilizes induction heating for brazing and soldering critical components.
- Melting of metals is also a common application, where induction furnaces provide precise temperature control and efficient melting.
These are just a few examples of the many ways induction heating is revolutionizing manufacturing and materials processing across various industries. Its unique capabilities make it an invaluable tool for enhancing efficiency, improving product quality, and reducing environmental impact.
Core Concepts: Understanding the Physics Behind the Heat
Unlocking the potential of induction heating requires a firm grasp of the fundamental physics at play. This section delves into the core scientific concepts that underpin this technology.
We break down the underlying principles, providing a practical understanding of how electromagnetic fields transform into targeted heat. This is the cornerstone of optimizing induction heating processes for efficiency and precision.
Electromagnetic Induction: The Foundation
At the heart of induction heating lies the principle of electromagnetic induction, a phenomenon described by Faraday's Law.
This law states that a changing magnetic field induces a voltage (electromotive force, or EMF) in any closed circuit within the field.
In induction heating, an alternating current flows through an induction coil, generating a fluctuating magnetic field around it.
When a conductive material is placed within this field, the changing magnetic flux induces a voltage within the material.
This induced voltage drives a current flow within the material, laying the foundation for heat generation.
Eddy Currents: The Workhorses of Heat Generation
The currents induced within the material, as a result of electromagnetic induction, are known as eddy currents.
These currents circulate within the material in closed loops, much like eddies in a stream.
Due to the electrical resistance of the material, the flow of eddy currents causes resistive heating (also known as Joule heating).
This is described by the equation P = I²R, where P is the power dissipated as heat, I is the current, and R is the resistance.
Therefore, the higher the eddy current density and the material's resistance, the greater the heat generated.
The Skin Effect: Concentrating the Heat
The skin effect is a phenomenon where alternating current tends to flow near the surface of a conductor, rather than distributing evenly throughout its cross-section.
This effect is more pronounced at higher frequencies.
The depth to which the current penetrates, known as the skin depth, decreases as the frequency increases.
Visualizing the Skin Effect
Imagine the current flow as layers in the conductor. With the skin effect, these layers are concentrated near the surface.
This is why induction heating is particularly effective for surface hardening applications.
By controlling the frequency, we can precisely control the depth of heating.
Frequency and Penetration Depth: A Delicate Balance
The frequency of the alternating current plays a crucial role in determining the penetration depth of the heat.
Higher frequencies result in shallower penetration, concentrating the heat near the surface.
Lower frequencies allow for deeper penetration, heating the bulk of the material more uniformly.
The relationship between frequency (f) and penetration depth (δ) can be approximated by:
δ ≈ √(ρ / (πμf))
Where ρ is the resistivity of the material, and μ is its permeability.
Choosing the appropriate frequency is critical for achieving the desired heating profile.
Power Density: The Key to Rapid Heating
Power density refers to the amount of power applied per unit volume of the material being heated (typically expressed in W/cm³ or W/in³).
Higher power density leads to faster heating rates.
However, it's essential to manage power density carefully to avoid overheating or damaging the material.
Factors influencing power density include:
- The strength of the magnetic field
- The frequency of the alternating current
- The material's properties
- The design of the induction coil
Optimizing power density is key to achieving both efficiency and desired heating outcomes in induction heating applications.
Theoretical Foundation: Deep Dive into the Electromagnetic and Thermal Processes
Unlocking the potential of induction heating requires a firm grasp of the fundamental physics at play. This section elaborates on the electromagnetic induction principles, delving into how magnetic fields and induced voltage and current contribute to the heating process. We'll also discuss the heat transfer mechanisms involved and the impact of material properties on the overall process. This is crucial to understanding how to optimize heating, control the heating process, and select the right materials.
Electromagnetic Induction Principles
The bedrock of induction heating lies in the principles of electromagnetism. Understanding how magnetic fields are generated and how they induce voltage and current is essential for anyone seeking to leverage this technology effectively.
Magnetic Field Generation and Coil Current
The process begins with the passage of alternating current (AC) through the induction coil. This AC current generates a time-varying magnetic field around the coil, as described by Ampere's Law. The strength and frequency of this magnetic field are directly proportional to the magnitude and frequency of the current flowing through the coil.
The coil's design is critical; factors like the number of turns, coil geometry, and spacing between turns influence the magnetic field's intensity and distribution. A well-designed coil concentrates the magnetic field within the workpiece, maximizing heating efficiency.
Induced Voltage and Current in the Workpiece
This time-varying magnetic field then interacts with the workpiece, inducing a voltage within it, according to Faraday's Law of Induction.
This induced voltage drives the flow of eddy currents within the conductive material of the workpiece. These eddy currents are circulating currents that flow in closed loops, primarily near the surface of the material due to the skin effect.
The magnitude of these eddy currents is directly proportional to the rate of change of the magnetic field and the material's electrical conductivity. It is the resistance to the flow of these induced currents that generates heat within the workpiece, according to Joule's Law.
Heat Transfer Mechanisms
Once heat is generated within the workpiece, understanding how this heat is transferred and distributed is crucial for controlling the heating process and achieving the desired temperature profile. There are three primary heat transfer mechanisms at play: conduction, convection, and radiation.
Roles of Conduction, Convection, and Radiation
-
Conduction is the transfer of heat through a material due to a temperature gradient. Heat flows from hotter regions to cooler regions within the workpiece, driven by the material's thermal conductivity.
-
Convection involves heat transfer between a solid surface and a moving fluid (liquid or gas). In induction heating, convection occurs primarily at the surface of the workpiece, where heat is transferred to the surrounding air or a cooling fluid.
-
Radiation is the emission of electromagnetic waves from a surface due to its temperature. The rate of radiative heat transfer increases rapidly with temperature, becoming significant at higher temperatures.
Influence on Temperature Distribution
Each of these heat transfer mechanisms plays a crucial role in shaping the temperature distribution within the workpiece. Conduction helps to even out temperature gradients within the material. Convection and radiation dissipate heat from the surface, preventing overheating.
Carefully balancing these heat transfer mechanisms is essential for achieving uniform and controlled heating.
Impact of Material Properties
The material properties of the workpiece significantly influence its ability to be heated via induction. Thermal conductivity, magnetic permeability, and electrical resistivity are particularly important.
Thermal Conductivity
Thermal conductivity determines how readily heat is conducted through the material. Materials with high thermal conductivity will exhibit more uniform temperature distributions, as heat is rapidly transferred from hotter regions to cooler regions.
Conversely, materials with low thermal conductivity may experience more significant temperature gradients, potentially leading to localized overheating.
Magnetic Permeability
Magnetic permeability is a measure of a material's ability to support the formation of magnetic fields within itself. Materials with high magnetic permeability, such as ferromagnetic materials, are more readily heated by induction.
This is because they concentrate the magnetic field within the material, leading to higher induced currents and more efficient heating.
Electrical Resistivity
Electrical resistivity is a measure of a material's resistance to the flow of electric current. Materials with higher electrical resistivity will generate more heat for a given induced current, due to increased Joule heating.
However, extremely high resistivity can also limit the magnitude of the induced current, reducing the overall heating effect.
Understanding these material properties and how they interact with the electromagnetic and thermal processes is critical for successful induction heating applications.
Materials Under the Influence: Choosing the Right Material for Induction Heating
Unlocking the potential of induction heating relies heavily on understanding how different materials interact with electromagnetic fields.
Not all materials respond equally well to the process. This section focuses on the crucial material properties that determine suitability for induction heating, with a detailed discussion on both ferromagnetic and conductive materials.
Ferromagnetic Materials: The Magnetic Advantage
Ferromagnetic materials exhibit unique characteristics that make them exceptionally well-suited for induction heating. The most significant of these is their high magnetic permeability.
This property allows these materials to concentrate magnetic flux lines within their structure, leading to a more intense interaction with the induced electromagnetic field.
Hysteresis Losses: A Key Heating Mechanism
In ferromagnetic materials, hysteresis losses play a substantial role in the heating process.
As the alternating magnetic field cycles, the magnetic domains within the material repeatedly align and realign, generating heat due to friction and energy dissipation.
This phenomenon, combined with eddy current heating, makes ferromagnetic materials highly efficient absorbers of electromagnetic energy.
Examples and Applications
Common examples of ferromagnetic materials include iron, nickel, cobalt, and various steels. These materials are widely used in applications such as:
-
Heat treating: Hardening, tempering, and annealing of steel components.
-
Surface hardening: Enhancing the wear resistance of parts like gears and crankshafts.
-
Forging: Heating billets of steel to the required temperature for shaping.
The strong magnetic response of these materials makes them ideal for applications requiring rapid and efficient heating.
Conductive Materials: Harnessing Eddy Currents
While ferromagnetic materials benefit from both hysteresis and eddy current losses, non-ferrous conductive metals like aluminum, copper, and brass primarily rely on eddy currents for heating.
These materials do not exhibit significant hysteresis effects, so the heating mechanism is solely based on the circulating currents induced by the alternating magnetic field.
Eddy Current Heating: A Closer Look
The efficiency of induction heating in conductive materials is directly related to their electrical conductivity.
Materials with higher conductivity allow for the generation of stronger eddy currents, leading to increased heat generation.
The skin effect is also particularly relevant here, concentrating the current flow near the surface of the material and influencing the heating profile.
Applications of Conductive Material Heating
Induction heating of conductive materials is prevalent in industries like:
-
Melting: Melting aluminum and copper for casting and refining.
-
Brazing and Soldering: Joining metal parts with high precision and localized heating.
-
Shrink Fitting: Expanding metal components for assembly.
Although the heating mechanism differs from ferromagnetic materials, induction heating provides a rapid, clean, and efficient method for processing conductive metals.
The Induction Heating Arsenal: A Guide to Essential Equipment
Achieving precise and efficient induction heating is impossible without the right tools. This section provides a comprehensive overview of the essential equipment required for a successful induction heating setup. We will explore the function, critical design considerations, and operational nuances of each component.
Induction Coils: The Heart of the System
The induction coil is arguably the most crucial component in an induction heating system. It generates the alternating magnetic field that induces eddy currents within the workpiece, ultimately leading to heating.
The design of the coil is paramount to efficient and targeted heating.
Induction Coil Designs and Types
Induction coils come in a wide array of shapes and sizes, each optimized for specific applications. Some common designs include:
-
Solenoid Coils: These are helical coils that surround the workpiece and are ideal for heating cylindrical objects uniformly.
-
Pancake Coils: These flat, spiral coils are well-suited for heating flat surfaces or for applications requiring concentrated heat.
-
Internal Coils: Designed to fit inside a workpiece (like a pipe).
-
Channel Coils: Suited for continuous heating of moving parts.
-
Hairpin Coils: These coils are shaped like a hairpin and are used for localized heating or hardening of specific areas.
Design Considerations for Induction Coils
Several factors must be carefully considered when designing an induction coil:
-
Geometry: The shape and dimensions of the coil must be tailored to the geometry of the workpiece to ensure optimal coupling and heating uniformity.
-
Number of Turns: The number of turns in the coil affects the magnetic field strength and the impedance of the coil.
-
Coil Material: Copper is the most common coil material due to its high electrical conductivity and ability to dissipate heat effectively.
-
Cooling: Adequate cooling of the coil is essential to prevent overheating and maintain its performance. This is usually achieved using water-cooled copper tubing.
-
Coil Spacing: The distance between the coil and the workpiece, or between turns of the coil.
Careful consideration of these factors will lead to a coil design that delivers the required heating pattern.
Power Supplies (Inverters): Supplying the Energy
Power supplies, often referred to as inverters, are responsible for converting the available AC line voltage into the high-frequency AC power required for induction heating.
The inverter's frequency and power output are critical parameters that must be carefully selected to match the specific application and material being heated. Modern inverters use solid-state technology to achieve high efficiency and precise control over the output power and frequency.
This allows for fine-tuning the heating process and achieving the desired temperature profile.
Matching Networks (Resonant Circuits): Optimizing Power Transfer
Matching networks, also known as resonant circuits, play a vital role in ensuring efficient power transfer from the power supply to the induction coil and workpiece.
The impedance of the induction coil and workpiece typically differs from the output impedance of the power supply. Mismatch in impedance can lead to significant power loss and reduced heating efficiency.
The matching network is carefully designed to match the impedance of the load (coil and workpiece) to that of the power supply. This is typically achieved using capacitors and inductors arranged in a resonant circuit.
By tuning the resonant frequency of the matching network to the operating frequency of the power supply, maximum power transfer can be achieved.
Cooling Systems: Preventing Overheating
Induction heating generates a significant amount of heat, not only in the workpiece but also in the induction coil and other components of the system. Cooling systems are essential to prevent overheating and ensure the reliable operation of the equipment.
Cooling Methods
Several cooling methods are commonly used in induction heating systems:
-
Water Cooling: This is the most common method, where water is circulated through the induction coil and other components to remove heat.
-
Air Cooling: This is suitable for low-power applications, where air is blown over the components to dissipate heat.
The choice of cooling method depends on the power level of the system and the cooling requirements of the individual components.
Temperature Sensors: Monitoring the Heat
Temperature sensors play a crucial role in monitoring and controlling the heating process. Accurate temperature measurement is essential for achieving the desired metallurgical properties in heat-treating applications or preventing overheating in melting processes.
Types of Temperature Sensors
Various types of temperature sensors are used in induction heating systems, including:
-
Thermocouples: These are simple and robust sensors that generate a voltage proportional to the temperature difference between two dissimilar metals.
-
Infrared Pyrometers: These non-contact sensors measure the infrared radiation emitted by the workpiece to determine its temperature.
-
Fiber Optic Sensors: These sensors offer high accuracy and immunity to electromagnetic interference, making them ideal for use in harsh environments.
The data from the temperature sensors is fed into a control system. The control system uses this data to adjust the power output of the power supply. This makes for precise temperature control.
High-Frequency Generators: Power Source
High-frequency generators are the fundamental source of AC power for induction heating systems. They provide the oscillating electrical current that, when passed through the induction coil, creates the magnetic field necessary for the heating process.
The generator's ability to deliver stable and controlled high-frequency power is essential for achieving consistent and repeatable heating results.
Modern generators utilize advanced solid-state technologies to ensure both efficiency and reliability. These improvements allow for precise control and adjustment of the power output based on material properties.
Putting Induction Heating to Work: Real-World Applications Across Industries
The Induction Heating Arsenal: A Guide to Essential Equipment Achieving precise and efficient induction heating is impossible without the right tools. However, understanding its practical applications is equally crucial. This section showcases the diverse and impactful ways induction heating is employed across various industries, transforming manufacturing processes and enabling innovative solutions. From enhancing material properties through heat treating to enabling precision joining techniques, we'll explore the breadth of this technology's utility.
Heat Treating: Tailoring Material Properties with Precision
Heat treating is a core metallurgical process, and induction heating offers significant advantages in this domain. Hardening, tempering, and annealing are all achievable with greater control and efficiency compared to traditional methods.
Induction allows for localized heating, targeting specific areas of a component. This reduces energy consumption and minimizes distortion of the overall part.
This targeted approach also makes it ideal for surface hardening, where only the outer layer of a component needs to be modified.
Surface Hardening: Enhancing Wear Resistance and Fatigue Life
Surface hardening via induction heating is widely employed to improve wear resistance and fatigue life of components. The rapid, localized heating allows for precise control over the hardened layer's depth and hardness.
This is particularly valuable in the automotive industry for components like gears and crankshafts. By selectively hardening the surfaces subjected to the most stress, manufacturers can enhance durability without compromising the core material's properties.
Compared to case hardening methods, such as carburizing or nitriding, induction hardening offers faster processing times and avoids potential issues associated with chemical treatments.
Melting: Clean and Efficient Metal Processing
Induction heating plays a crucial role in melting metals for casting and refining processes.
Induction furnaces provide a cleaner and more energy-efficient alternative to traditional methods like arc furnaces. The absence of combustion byproducts results in a more controlled and environmentally friendly melting process.
Furthermore, the stirring action induced by electromagnetic fields ensures a homogenous melt composition, leading to improved casting quality. From precious metals refining to specialty alloy production, induction melting delivers superior control and purity.
Forging: Precise Heating for Enhanced Formability
Heating metal billets for forging is another area where induction heating excels. Its rapid and uniform heating characteristics are essential for achieving optimal formability.
Compared to traditional furnace heating, induction reduces scale formation, leading to improved surface finish and reduced material waste. This translates to cost savings and enhanced product quality.
The precise temperature control offered by induction ensures that the billet reaches the ideal forging temperature consistently.
Brazing and Soldering: Strong and Precise Metal Joints
Induction heating provides a highly effective method for joining metal parts through brazing and soldering.
The localized heating minimizes heat-affected zones, preventing distortion and preserving the integrity of surrounding materials.
This precision makes it ideal for joining dissimilar metals and delicate components. Induction brazing and soldering are commonly used in electronics manufacturing, HVAC systems, and the automotive industry.
The speed and reliability of the process contribute to higher production rates and reduced manufacturing costs.
Shrink Fitting: A Secure and Efficient Assembly Technique
Shrink fitting involves expanding one component through heating to allow for the insertion of another. Induction heating offers a rapid, controllable, and precise method for this assembly technique.
By selectively heating the outer component, a tight and secure fit can be achieved upon cooling.
This method is particularly useful for assembling large components where mechanical joining methods are impractical or insufficient. Applications include engine assembly, bearing mounting, and structural component fabrication.
Fine-Tuning the Process: Optimization and Control for Peak Efficiency
Achieving precise and efficient induction heating is impossible without the right tools. However, understanding its practical applications is equally crucial. This section delves into the factors that affect the efficiency of induction heating, exploring methods for optimizing the process. Coil design, frequency selection, and power control will be discussed in detail.
The Critical Role of Coil Design
The induction coil is arguably the most critical component dictating the efficiency and effectiveness of the entire heating process. Its geometry and proximity to the workpiece dramatically influence the magnetic field distribution and, consequently, the induced current density within the material.
A poorly designed coil can result in uneven heating, wasted energy, and even damage to the workpiece or the equipment itself.
Geometry Matters: Tailoring the Coil to the Task
The shape and dimensions of the coil must be carefully matched to the geometry of the workpiece. For example, heating a cylindrical part requires a different coil design than heating a flat plate.
Coil geometry affects the magnetic flux density and direction, impacting the induced current path and intensity within the heated material.
Computer simulations are often employed to optimize coil designs, predicting field distributions and identifying potential hotspots or areas of insufficient heating.
Proximity Effects: Managing Electromagnetic Interference
The proximity effect refers to the non-uniform distribution of current within the coil conductors due to the presence of the workpiece and other nearby conductors. This effect can increase the effective resistance of the coil, leading to power losses and reduced efficiency.
Careful coil placement and the use of appropriate conductor materials (e.g., Litz wire) can mitigate the proximity effect and improve overall performance. Understanding the proximity effect is critical for maximizing energy transfer and minimizing heat generation within the coil itself.
Frequency Selection: Finding the Sweet Spot
The frequency of the alternating current supplied to the induction coil plays a crucial role in determining the depth of penetration of the induced current into the workpiece. This relationship is governed by the skin effect, where higher frequencies result in shallower penetration depths.
Balancing Depth and Efficiency
Selecting the optimal frequency involves balancing the desired heating depth with energy efficiency considerations.
For surface hardening, high frequencies are typically preferred to concentrate the heat near the surface. Conversely, for through-heating applications, lower frequencies are used to achieve more uniform temperature distribution throughout the material.
Material Properties and Frequency
The material properties of the workpiece also influence the optimal frequency. Materials with higher electrical conductivity and magnetic permeability tend to require lower frequencies for efficient heating. Careful consideration of these factors is essential for maximizing energy absorption and minimizing losses.
Power Control: Shaping the Heat Profile
Precise power control is essential for achieving the desired heating profile and preventing overheating or damage to the workpiece. The ability to modulate the power delivered to the induction coil allows for precise control over the heating rate and final temperature.
Open-Loop vs. Closed-Loop Control
Open-loop power control relies on pre-programmed settings and does not incorporate feedback from temperature sensors. While simple to implement, this approach is less accurate and less adaptable to variations in material properties or process conditions.
Closed-loop control systems utilize feedback from temperature sensors to continuously adjust the power output, maintaining the desired temperature or heating rate. This approach offers superior accuracy and adaptability, ensuring consistent and reliable results.
Dynamic Adjustment for Optimal Results
Advanced power control systems can dynamically adjust the power output based on real-time temperature measurements, compensating for variations in material properties, load conditions, or environmental factors. This level of control is essential for demanding applications requiring precise temperature uniformity and minimal distortion.
Process Control Systems: The Brains of the Operation
Modern induction heating systems often incorporate sophisticated process control systems that automate the monitoring and adjustment of key process parameters. These systems provide real-time data on temperature, power, frequency, and other critical variables, enabling operators to optimize the process and ensure consistent quality.
Automation for Consistency and Efficiency
Automated process control systems can significantly improve efficiency by minimizing operator errors and optimizing energy consumption. These systems can also be integrated with other manufacturing processes, creating a seamless and highly efficient production line.
Data Logging and Analysis
Process control systems typically include data logging capabilities, allowing for the collection and analysis of process data over time. This data can be used to identify trends, diagnose problems, and further optimize the process for improved performance and reduced costs.
By implementing these optimization and control strategies, manufacturers can unlock the full potential of induction heating, achieving higher efficiency, improved product quality, and reduced operating costs.
The Experts Behind the Technology: The Roles of Engineers and Personnel
Achieving precise and efficient induction heating is impossible without the right tools. However, understanding its practical applications is equally crucial. This section delves into the factors that affect the efficiency of induction heating, exploring methods for optimizing the process and examining the crucial roles played by the engineers and personnel driving this technology forward. Their expertise ensures both the creation of reliable equipment and its safe and effective operation in various industrial settings.
Engineers at Equipment Manufacturers: Architects of Induction Solutions
Engineers at equipment manufacturers are the cornerstone of the induction heating industry. These professionals are responsible for the design, development, and continuous improvement of induction heating systems. Their expertise spans a variety of engineering disciplines, including electrical, mechanical, and materials science.
Design and Development
The design phase requires a deep understanding of electromagnetic theory, heat transfer principles, and material properties. Engineers utilize simulation software to model and optimize coil designs, ensuring efficient energy transfer and uniform heating patterns. Careful consideration is given to the specific application, material being heated, and desired temperature profile.
They must also select appropriate power supplies, cooling systems, and control mechanisms to meet performance requirements.
Furthermore, engineers must design systems that comply with industry safety standards and regulations.
Manufacturing and Quality Control
During the manufacturing phase, engineers oversee the fabrication, assembly, and testing of induction heating equipment. They ensure that all components meet stringent quality standards and that the final product performs reliably under demanding conditions.
This includes implementing quality control procedures to identify and rectify any defects or malfunctions.
Moreover, engineers provide technical support and training to customers, assisting them with the installation, operation, and maintenance of their equipment.
Research and Innovation
Engineers are also at the forefront of research and innovation in the induction heating industry. They are constantly exploring new materials, coil designs, and control strategies to improve the efficiency, performance, and versatility of induction heating systems.
This includes investigating the use of advanced simulation techniques, developing novel power supply technologies, and exploring new applications for induction heating in emerging industries.
Operators: Ensuring Safe and Effective Operation
The operators of induction heating equipment are responsible for the day-to-day operation, monitoring, and maintenance of the systems. Their role is critical to ensure that the equipment is used safely and effectively to achieve the desired heating results.
System Setup and Operation
Operators are responsible for setting up the induction heating system according to the specific application requirements. This includes selecting the appropriate coil, adjusting the power settings, and configuring the control system.
They must also monitor the heating process closely, making adjustments as needed to maintain the desired temperature profile and prevent overheating or damage to the material being heated.
Safety Protocols and Maintenance
Adherence to safety protocols is paramount. Operators must be thoroughly trained in the safe operation of induction heating equipment and follow established safety procedures to prevent accidents and injuries.
This includes wearing appropriate personal protective equipment, maintaining a clean and organized work environment, and promptly reporting any equipment malfunctions or safety hazards.
Routine maintenance is also essential to ensure the reliable operation of induction heating equipment. Operators are responsible for performing routine inspections, cleaning components, and replacing worn parts as needed.
Collaboration and Continuous Improvement
Operators often collaborate closely with engineers and other technical personnel to troubleshoot problems, optimize the heating process, and identify opportunities for improvement.
Their practical experience and feedback are invaluable in refining the design and operation of induction heating systems. They are integral to the continuous improvement cycle that drives innovation and ensures the ongoing success of the industry.
The Future of Heat: Innovations and Emerging Trends in Induction Heating
As we reach the culmination of our exploration into induction heating, it's essential to look toward the horizon and consider the future trajectory of this dynamic technology. Innovation is the lifeblood of any engineering field, and induction heating is no exception. Let's examine some of the emerging trends and potential future applications that promise to reshape the landscape.
New Materials and Their Application
The development and integration of new materials stand as a critical area of advancement. Materials with enhanced magnetic properties or unique thermal characteristics offer opportunities to improve heating efficiency and expand the range of applications.
For example, the exploration of amorphous alloys with superior magnetic permeability could lead to more efficient induction coils, reducing energy consumption and enhancing performance. Composites tailored for specific heating profiles could also enable highly localized heat treatment in advanced manufacturing processes.
Advanced Coil Designs for Specialized Applications
Induction coil design is constantly evolving to meet the demands of increasingly complex applications. Customized coil geometries and configurations are becoming essential for achieving precise heating patterns and maximizing energy transfer efficiency.
Conformal Coils
One area of focus is the development of conformal coils that closely match the shape of the workpiece, enabling uniform heating of intricate geometries. Additive manufacturing techniques, such as 3D printing, are facilitating the creation of these complex coil structures.
Multi-Frequency Coils
Another trend is the use of multi-frequency coils, which can simultaneously deliver energy at different frequencies to achieve tailored heating profiles. This approach allows for precise control over the depth and distribution of heat within the material.
Integration with Industry 4.0 and IoT
The integration of induction heating systems with Industry 4.0 principles and the Internet of Things (IoT) is poised to revolutionize process control and automation. Real-time data acquisition, advanced analytics, and predictive modeling are enabling operators to optimize heating parameters, minimize downtime, and improve overall system performance.
Remote Monitoring and Control
IoT sensors can monitor critical parameters, such as temperature, power consumption, and coil impedance, providing valuable insights into the heating process. This data can be used to remotely adjust system settings, identify potential issues, and schedule maintenance, ultimately maximizing productivity and minimizing costs.
Predictive Maintenance
Predictive maintenance algorithms can analyze historical data to forecast equipment failures and optimize maintenance schedules. This proactive approach helps to prevent unexpected downtime and extend the lifespan of induction heating systems.
The Rise of AI-Powered Induction Heating
Artificial intelligence (AI) is quickly emerging as a transformative force in the field of induction heating. AI algorithms can analyze vast amounts of data from sensors and simulations to optimize process parameters in real-time, leading to improved energy efficiency and reduced scrap rates.
Automated Process Optimization
AI-powered control systems can automatically adjust frequency, power, and coil positioning to achieve desired heating profiles, even in the presence of varying material properties or complex geometries. This level of automation significantly reduces the need for manual intervention and allows for consistent, high-quality results.
Defect Detection and Prediction
AI can also be used to analyze thermal images and other sensor data to detect defects in the heated material. By identifying anomalies early in the process, manufacturers can prevent costly errors and improve product quality.
The Greening of Induction Heating
As sustainability becomes an increasingly important concern, the focus on energy efficiency and reduced environmental impact is driving further innovation in induction heating. New power electronics and control strategies are being developed to minimize energy consumption and reduce carbon emissions.
Renewable Energy Integration
Integrating induction heating systems with renewable energy sources, such as solar and wind power, is another promising avenue for reducing the environmental footprint of manufacturing processes. Smart grid technologies can optimize energy usage and ensure a reliable supply of power to induction heating equipment.
Video: Induction Helps Heat Tran: Efficiency Guide
FAQs: Induction Helps Heat Transfer: Efficiency Guide
How does induction cooking improve heat transfer efficiency?
Induction cooking directly heats the cookware itself using electromagnetic fields. Because induction helps in heat tran, this eliminates the intermediate heating of a burner surface, resulting in faster heating times and less wasted energy.
What cookware works best with induction for optimal heat transfer?
Cookware must be made of a ferromagnetic material to work with induction cooktops. Cast iron and many stainless-steel pots are good choices. Check for the induction-compatible symbol on the bottom of your pots. This ensures optimal induction helps in heat tran.
Does consistent contact between cookware and the cooktop impact efficiency?
Yes, a flat-bottomed pan provides maximum contact with the cooktop surface, leading to the best heat transfer. Warped or uneven cookware reduces contact, increasing heating time and wasting energy. Better contact means induction helps in heat tran better.
Can the size of the pan affect the efficiency of induction cooking?
Yes. Using a pan that is too small for the induction element can lead to energy loss as the magnetic field is not fully utilized. Matching the pan size to the element size ensures induction helps in heat tran most effectively.
So, there you have it! Hopefully, this guide sheds some light on how induction helps in heat tran and boosts efficiency. Give induction cooking a try – you might just be surprised at how much you love it (and how much energy you save!). Happy cooking!