High Temp Metals: The Ultimate Guide You Need to Read
High temp metals represent a class of materials essential to industries ranging from aerospace, where companies like Boeing rely on their performance, to nuclear energy, a sector demanding utmost safety. These advanced materials are often studied under the methodologies outlined in Metallurgy, a critical area of materials science. The superior strength and resistance to creep exhibited by these high temp metals allows for operations in demanding environments, thus highlighting their critical role in both technological advancement and industrial efficiency.
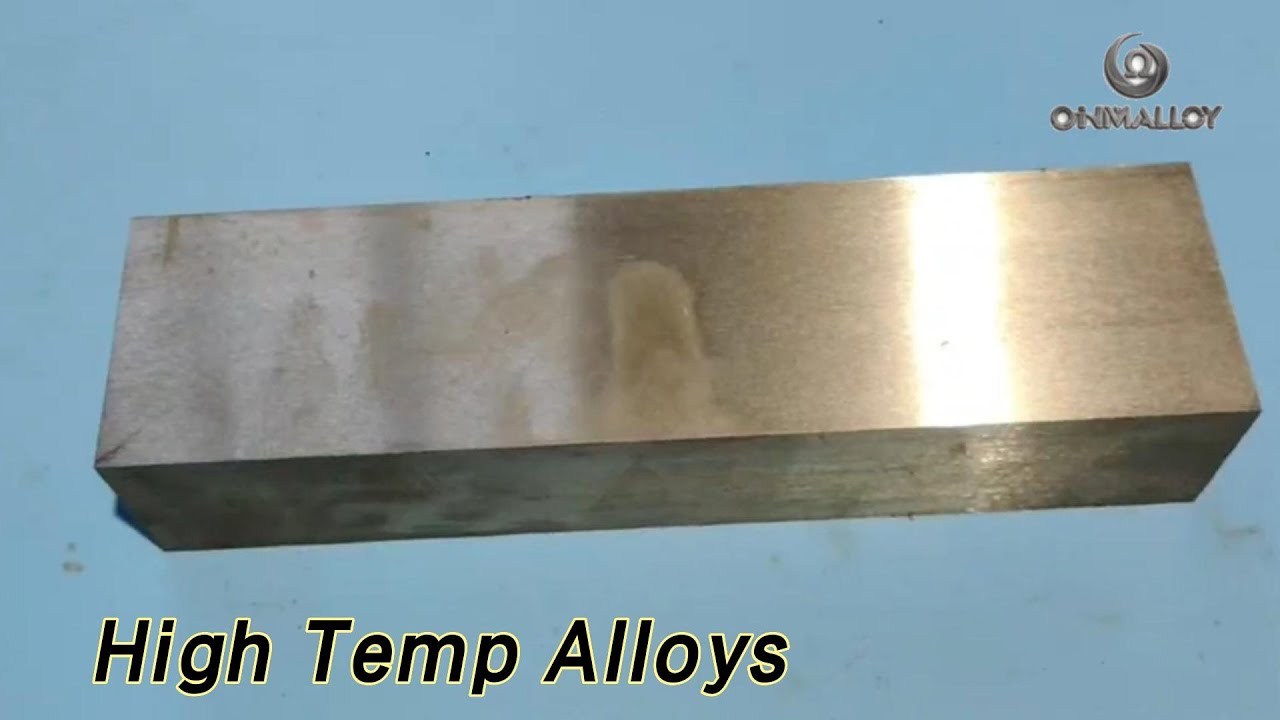
Image taken from the YouTube channel China Factories , from the video titled Nickel Based High Temp Alloys Rod / Bar Bright Hot Forging High Strength .
High-temperature metals are the unsung heroes of modern technology.
They operate behind the scenes in some of the most demanding environments imaginable.
These materials are not merely heat-resistant; they are engineered to maintain their structural integrity and functionality under extreme thermal stress.
Their unique properties make possible countless advancements across diverse industries.
The Indispensable Role of High-Temperature Metals
The ability of high-temperature metals to withstand extreme operating conditions makes them indispensable in various critical sectors.
Consider the aerospace industry, where jet engines endure searing temperatures.
Or the power generation sector, where turbines operate under immense heat and pressure to efficiently generate energy.
Without these specialized materials, many of our most crucial technologies would simply not be viable.
Critical Applications in Extreme Environments
The applications of high-temperature metals are diverse, yet united by a common thread: extreme operating conditions.
In jet engines, high-temperature alloys enable higher combustion temperatures.
This translates directly into improved fuel efficiency and thrust.
In power plants, superalloys are essential for withstanding the high-temperature, high-pressure steam that drives turbines.
The chemical processing industry relies on these metals to contain corrosive reactions at elevated temperatures.
Nuclear reactors depend on them to maintain safety and efficiency under intense radiation and heat.
Even the automotive industry utilizes high-temperature metals in exhaust systems to manage emissions and improve performance.
Setting the Stage: A Comprehensive Exploration
This article embarks on an in-depth exploration of the fascinating world of high-temperature metals.
We will delve into the different types of high-temperature metals.
This includes their unique properties, and their diverse applications.
From superalloys to refractory metals, we will uncover the characteristics that make these materials so crucial.
We will also examine the mechanical, thermal, and chemical properties that govern their performance under extreme conditions.
Finally, we will highlight the various industries that rely on these metals to drive innovation and progress.
High-temperature metals are indispensable for pushing the boundaries of engineering and technology.
But before we delve deeper into specific types and applications, it's crucial to establish a clear understanding of what exactly defines a "high-temperature" metal.
What Defines a High-Temperature Metal?
The term "high-temperature metal" isn't simply a casual descriptor. It denotes a specific class of materials engineered to excel in environments where ordinary metals would fail.
The defining characteristics revolve around their ability to maintain structural integrity and resist degradation under intense heat.
Defining the Temperature Threshold
So, what temperature range officially classifies a metal as "high-temperature?" The answer isn't a single, universally accepted number.
Instead, the classification depends heavily on the intended application and the performance requirements.
Generally, a metal is considered high-temperature if it can retain useful mechanical properties above 500°C (932°F).
Some alloys may qualify at even lower temperatures if they offer superior resistance to creep or oxidation compared to standard materials.
It's important to note that the absolute melting point of a metal isn't the sole determinant. A metal with a high melting point might still be unsuitable for high-temperature applications if it loses its strength or corrodes rapidly at elevated temperatures.
Key Distinguishing Characteristics
Several key characteristics distinguish high-temperature metals from their standard counterparts:
-
High Melting Point: While not the only factor, a high melting point is a prerequisite. This allows the metal to physically withstand extreme heat without undergoing phase change.
-
Excellent Creep Resistance: Creep is the slow, permanent deformation of a material under sustained stress at high temperatures. High-temperature metals are formulated to resist creep, maintaining their shape and dimensional stability over long periods.
-
Superior Oxidation Resistance: At high temperatures, many metals react rapidly with oxygen in the atmosphere, forming oxides that can weaken the material. High-temperature metals possess exceptional oxidation resistance, either through inherent properties or protective surface coatings.
-
High-Temperature Strength: Ordinary metals tend to lose their strength dramatically as temperature increases. High-temperature metals are designed to retain a significant portion of their strength, stiffness, and hardness even at elevated temperatures.
-
Fatigue Resistance: Many high-temperature components are subject to cyclic loading (repeated stress). High-temperature metals should exhibit high fatigue resistance. This allows them to withstand these stresses without premature failure.
The Importance of Creep Resistance
Creep resistance is arguably the most critical property for high-temperature applications.
Imagine a turbine blade inside a jet engine. It's constantly subjected to immense centrifugal forces at temperatures exceeding 1000°C.
If the blade material isn't highly creep-resistant, it will slowly elongate and deform over time.
Eventually, it would collide with the engine casing, leading to catastrophic failure.
Creep resistance is achieved through careful alloy design, often involving the addition of elements that impede the movement of dislocations within the metal's crystal structure.
Combating Oxidation: The Key to Longevity
Oxidation is another major concern in high-temperature environments.
The formation of oxide scales on the metal's surface can lead to several problems, including:
-
Loss of material: As the metal oxidizes, it effectively "rusts" away, reducing the component's thickness and strength.
-
Embrittlement: Oxide scales can be brittle and prone to cracking, creating pathways for further oxidation and weakening the underlying metal.
-
Changes in Dimensions: The formation of oxide scales can alter the component's dimensions, potentially affecting its performance.
High-temperature metals combat oxidation through various mechanisms.
Some alloys contain elements like chromium or aluminum that form a protective oxide layer that adheres tightly to the surface, preventing further oxidation.
Others rely on specialized coatings to shield the metal from the environment.
Exploring the Different Types of High-Temperature Metals
Having established the defining characteristics of high-temperature metals, it’s time to survey the landscape of these remarkable materials. Each class of high-temperature metal brings its own unique blend of properties to the table, making them suitable for specific niches where performance is paramount. From the extreme heat of jet engines to the corrosive environments of chemical processing plants, the right high-temperature metal can make all the difference.
Superalloys: The Powerhouses of Extreme Heat
Superalloys represent the gold standard in high-temperature performance. These alloys, often based on nickel or cobalt, are designed to retain exceptional strength and resist creep and oxidation at temperatures that would melt ordinary metals.
But what makes superalloys so special?
It's their carefully crafted composition, often involving a dozen or more elements, each playing a vital role in enhancing specific properties.
Their ability to maintain structural integrity at temperatures exceeding 1000°C (1832°F) makes them indispensable in demanding applications like gas turbines in jet engines and power plants.
Nickel-Based Superalloys: The Workhorses
Nickel-based superalloys are the most widely used type of superalloy.
Their strength lies in the ability of nickel to form a stable, protective oxide layer that resists further oxidation at high temperatures.
Common alloying elements include chromium, aluminum, and titanium, which contribute to strength, creep resistance, and environmental resistance.
These alloys find extensive use in aircraft turbine blades, rocket engines, and other high-stress, high-temperature components.
Cobalt-Based Superalloys: The Niche Specialists
Cobalt-based superalloys offer superior weldability and resistance to hot corrosion compared to their nickel counterparts.
However, they generally exhibit lower strength at very high temperatures.
Their excellent wear resistance and resistance to sulfidation make them ideal for applications in chemical processing and marine environments.
Nickel vs. Cobalt: A Comparative Glance
The choice between nickel-based and cobalt-based superalloys hinges on the specific application.
Nickel alloys dominate where high strength and creep resistance are paramount, while cobalt alloys excel in corrosive or wear-prone environments.
The cost and availability of raw materials also play a significant role in material selection.
Refractory Metals: Withstanding the Most Extreme Temperatures
When temperatures soar beyond the capabilities of even superalloys, refractory metals step in.
This group includes tungsten, molybdenum, tantalum, and niobium, all characterized by exceptionally high melting points (above 2000°C / 3632°F) and excellent high-temperature strength.
These metals are essential for applications operating at the very edge of what's physically possible.
Unique Properties and Limitations
Refractory metals exhibit remarkable high-temperature strength and stiffness.
However, they are also known for their high density, poor oxidation resistance at elevated temperatures (requiring protective coatings), and challenging machinability.
Applications in Extreme Environments
Refractory metals find niche applications in extreme high-temperature environments, such as:
- Rocket nozzles
- Furnace components
- Heating elements
- X-ray targets
Their ability to withstand intense heat fluxes makes them irreplaceable in these demanding roles.
High-Temperature Stainless Steels and Other Specialized Alloys
While superalloys and refractory metals command attention for their extreme capabilities, specialized grades of stainless steel and other alloys offer cost-effective solutions for moderately high-temperature applications.
These materials bridge the gap between standard alloys and the more exotic high-temperature metals.
High-Temperature Stainless Steels
Certain grades of stainless steel, such as austenitic stainless steels (e.g., 304, 316, 347) and ferritic stainless steels containing chromium and aluminum, are engineered for elevated temperatures.
These alloys offer a good balance of strength, oxidation resistance, and corrosion resistance, making them suitable for applications like:
- Exhaust manifolds
- Heat exchangers
- Furnace components
High-Temperature Titanium Alloys
Titanium alloys, known for their high strength-to-weight ratio and excellent corrosion resistance, also have high-temperature variants.
Alloying elements like aluminum, vanadium, and molybdenum enhance their high-temperature performance.
Applications include:
- Aerospace components (compressor blades)
- Engine parts requiring lightweight materials
High-Temperature Iron-Based Alloys
Beyond stainless steels, other iron-based alloys, like those containing additions of nickel, chromium, and molybdenum, can provide good high-temperature strength and creep resistance.
These alloys find use in applications such as:
- Turbine rotors
- Fasteners
- Structural components
Ceramic Matrix Composites (CMCs): An Emerging Class
Ceramic Matrix Composites (CMCs) represent an emerging class of high-temperature materials, combining the high-temperature capabilities of ceramics with the improved toughness and damage tolerance of composite materials.
They are made by reinforcing a ceramic matrix (e.g., silicon carbide) with ceramic fibers.
Exploring the Applications of CMCs
CMCs offer significant advantages over traditional metals in certain high-temperature applications.
Their key benefits include:
- Low density
- High strength at elevated temperatures
- Excellent thermal shock resistance
However, CMCs also have limitations, including:
- High manufacturing costs
- Susceptibility to oxidation in certain environments
Applications for CMCs are expanding, particularly in the aerospace industry, where they are being used in:
- Turbine blades
- Combustor liners
- Heat shields
As manufacturing costs decrease and material properties improve, CMCs are poised to play an increasingly important role in high-temperature applications.
Key Properties: How High-Temperature Metals Perform
The true measure of a high-temperature metal isn't just its ability to survive extreme heat, but how well it performs under those conditions. This performance is defined by a delicate interplay of mechanical, thermal, and chemical properties, each crucial for ensuring the reliability and longevity of components operating in demanding environments. Let's delve into these critical characteristics that determine the suitability of these specialized metals.
Mechanical Properties at High Temperatures
At elevated temperatures, metals behave very differently than they do at room temperature. The forces at play change, and the material's response to stress is significantly altered. Three key mechanical properties become paramount: tensile strength, creep resistance, and fatigue resistance.
Tensile Strength at High Temperatures
Tensile strength, at its core, measures a material's ability to withstand pulling forces before it starts to deform or break. At high temperatures, however, a metal's tensile strength typically decreases. The atomic bonds weaken, allowing atoms to move more freely and the material to stretch more easily under load.
Therefore, selecting a high-temperature metal with sufficient tensile strength at the operating temperature is critical to prevent catastrophic failure.
Creep Resistance
Creep is the slow, permanent deformation of a material under a constant stress, below its yield strength. This is particularly significant at high temperatures, where atomic diffusion is accelerated. Over time, even a relatively small constant load can cause a component to gradually stretch and distort, ultimately leading to failure.
Creep resistance is therefore a vital property for high-temperature metals, indicating their ability to withstand prolonged stress without deforming excessively. Alloys designed for high-temperature applications often incorporate elements that impede atomic diffusion, thus enhancing creep resistance.
Fatigue Resistance
Components operating in high-temperature environments are often subjected to cyclic loading, where stress levels fluctuate repeatedly. This can lead to fatigue failure, even if the peak stress is well below the metal's tensile strength.
High-temperature fatigue resistance is complex. It depends on factors like temperature, stress range, frequency of cycling, and the presence of any corrosive environment. Selecting alloys with high fatigue resistance and implementing appropriate design strategies are crucial for ensuring the long-term reliability of components exposed to cyclic loading at high temperatures.
Thermal Properties: Managing Heat
High-temperature environments inherently involve significant heat transfer and temperature gradients. Understanding and managing the thermal properties of metals is therefore essential to prevent thermal stress and ensure component integrity. Key thermal properties include thermal conductivity and thermal expansion.
Thermal Conductivity
Thermal conductivity refers to a material's ability to conduct heat. A high thermal conductivity allows heat to dissipate rapidly, preventing localized hot spots and reducing thermal stress.
However, in some applications, low thermal conductivity may be desirable to insulate components from extreme heat.
The ideal thermal conductivity depends on the specific application and the heat management strategy employed.
Thermal Expansion
All materials expand when heated, and metals are no exception. The extent of this expansion is quantified by the coefficient of thermal expansion.
Significant thermal expansion can lead to dimensional changes, which in turn can induce stress, particularly when components are constrained or made from dissimilar materials.
Impact of Thermal Stress
Thermal stress arises from temperature gradients or constrained thermal expansion/contraction within a material or assembly.
These stresses can be substantial and, if not properly managed, can lead to cracking, distortion, or even catastrophic failure.
Careful material selection, optimized component design, and the use of expansion joints can help mitigate the risks associated with thermal stress.
Chemical Properties: Resistance to Degradation
High-temperature environments are often chemically reactive, with the potential to cause significant degradation of metallic components. Oxidation and high-temperature corrosion are the primary concerns, and selecting materials with robust chemical resistance is paramount.
Oxidation Resistance
At elevated temperatures, metals react with oxygen in the atmosphere, forming oxides on their surfaces. While some oxides can be protective, preventing further oxidation, others are porous and non-adherent, leading to continuous degradation of the metal.
Oxidation resistance is thus a crucial property for high-temperature metals. This resistance is often achieved by alloying the metal with elements like chromium, aluminum, or silicon, which form stable, protective oxide layers.
Resistance to Other Forms of High-Temperature Corrosion
In addition to oxidation, high-temperature metals can be susceptible to other forms of corrosion, such as sulfidation, carburization, and attack by molten salts. These corrosion mechanisms can be particularly aggressive, leading to rapid material degradation.
Selecting alloys that are resistant to these specific corrosive environments is essential for ensuring long-term reliability. This may involve choosing materials with specific alloying elements or applying protective coatings to the metal surface.
Creep resistance, thermal conductivity, and oxidation resistance are essential for metals in high-temperature environments, but understanding the fundamentals only paints half the picture. To truly appreciate the significance of these specialized materials, it’s crucial to examine where they’re put to work.
Industry Applications: Where High-Temperature Metals Excel
High-temperature metals are not just laboratory curiosities; they are the unsung heroes driving innovation across numerous industries. Their unique ability to maintain strength and resist degradation at extreme temperatures makes them indispensable in applications where conventional materials would simply fail. From the skies above to the depths of power plants, these alloys are critical to the functionality and reliability of complex systems.
This section will showcase the diverse applications of high-temperature metals in sectors such as aerospace, power generation, chemical processing, nuclear reactors, and automotive. By examining specific requirements and the alloys used in each sector, we can gain a deeper understanding of their practical importance and the challenges they overcome.
Aerospace Industry: The Skies Demand Excellence
The aerospace industry represents perhaps the most demanding application for high-temperature metals. In jet engines and turbine blades, materials are subjected to a relentless barrage of extreme heat, intense pressure, and corrosive gases. The margin for error is virtually nonexistent; failure can have catastrophic consequences.
High-temperature metals are critical for the safe and efficient operation of these aircraft.
Turbine Blades: A Crucible of Extreme Conditions
Turbine blades within a jet engine face some of the harshest conditions imaginable. They spin at incredibly high speeds while enduring temperatures that can exceed the melting point of many conventional metals. To survive in this environment, these blades are crafted from advanced superalloys, often nickel-based or cobalt-based, that offer exceptional high-temperature strength, creep resistance, and oxidation resistance.
Commonly used alloys include Inconel (a nickel-chromium-based superalloy) and René alloys (known for their superior high-temperature strength). These materials are not only strong, but also carefully designed with intricate internal cooling systems to further mitigate the effects of extreme heat.
The specific alloys used and their heat treatments are precisely tailored to meet stringent performance requirements, ensuring the engine's reliability and efficiency. These superalloys are often single-crystal, meaning they lack grain boundaries that can weaken the material at high temperatures.
Power Generation: Reliable Energy Under Pressure
The power generation industry, like aerospace, relies heavily on high-temperature metals to produce electricity efficiently and reliably. Gas turbines and steam turbines, the workhorses of power plants, operate at high temperatures to maximize thermodynamic efficiency.
Gas Turbines: Powering the Grid
Gas turbines, used in both traditional power plants and combined-cycle systems, require materials that can withstand high temperatures and corrosive combustion gases. High-temperature metals are used in the turbine blades, combustion chambers, and other critical components.
Nickel-based superalloys are particularly favored for gas turbine applications due to their excellent high-temperature strength and resistance to oxidation and hot corrosion. These alloys enable turbines to operate at higher temperatures, boosting efficiency and reducing emissions.
Steam Turbines: Harnessing Thermal Energy
Steam turbines, another cornerstone of power generation, also benefit from high-temperature metals. Although steam turbines generally operate at lower temperatures than gas turbines, the steam itself can be highly corrosive, especially under high pressure.
High-temperature stainless steels and nickel-based alloys are employed in steam turbine blades and other components to resist corrosion and maintain strength over extended periods. The selection of appropriate alloys is critical to ensure the long-term reliability and efficiency of steam power plants.
Other Industries: A Wide Range of Applications
Beyond aerospace and power generation, high-temperature metals play vital roles in a diverse array of industries, each with unique demands and challenges.
Chemical Processing: Resisting Corrosion at High Temperatures
The chemical processing industry often involves highly corrosive environments at elevated temperatures. Reactors, heat exchangers, and piping systems must be constructed from materials that can withstand these harsh conditions.
Specialized stainless steels, nickel-based alloys, and even refractory metals like tantalum are used to resist corrosion and maintain structural integrity in these demanding applications. The choice of material depends on the specific chemicals involved and the operating temperature.
Nuclear Reactors: Safety and Reliability
Nuclear reactors demand exceptional safety and reliability. High-temperature metals are used in reactor components such as fuel cladding, control rods, and structural supports.
Zirconium alloys are commonly used as fuel cladding due to their low neutron absorption cross-section and resistance to high-temperature water and steam. Stainless steels and nickel-based alloys are also used in other reactor components to ensure structural integrity and prevent corrosion.
Automotive Industry: Managing Exhaust Heat
Even in the automotive industry, high-temperature metals find important applications. Exhaust systems, particularly in high-performance vehicles, can reach extreme temperatures.
Stainless steels and nickel-based alloys are used in exhaust manifolds, catalytic converters, and turbocharger components to resist oxidation and maintain structural integrity. These materials help to reduce emissions and improve engine performance.
In conclusion, the diverse applications of high-temperature metals underscore their critical role in modern technology. From enabling air travel to generating electricity and facilitating chemical processing, these specialized alloys are essential for industries that demand performance and reliability under extreme conditions. As technology advances and operating temperatures continue to rise, the importance of high-temperature metals will only increase.
Industry relies on the robust performance of high-temperature metals in demanding applications. However, the journey from raw material to finished high-performance component is far from straightforward. It involves a complex interplay of manufacturing processes, each with its own set of challenges and advantages. The following section will delve into the traditional and modern manufacturing techniques employed to shape these exceptional materials, exploring the intricacies involved in creating components capable of withstanding extreme conditions.
Manufacturing and Processing: From Raw Material to Finished Product
The creation of high-temperature metal components is a specialized field, demanding precise control and deep understanding of material behavior. Both traditional and cutting-edge manufacturing methods play a vital role in producing the parts that enable advanced technologies.
Traditional Manufacturing Methods: Tried and True
For decades, methods like casting, forging, and powder metallurgy have been the workhorses of metal manufacturing. While newer techniques emerge, these traditional approaches remain essential for producing high-temperature metal components, often at scale.
Casting
Casting involves pouring molten metal into a mold, allowing it to solidify into the desired shape. This method is particularly useful for creating complex geometries, but presents unique challenges with high-temperature alloys.
The high melting points of these metals require specialized mold materials and precise temperature control to prevent defects such as porosity or segregation. Investment casting and vacuum casting are often employed to achieve the necessary precision and minimize unwanted reactions.
Forging
Forging involves shaping metal using compressive forces, either through hammering or pressing. This process enhances the material's strength and toughness by aligning its grain structure.
However, forging high-temperature metals requires significant force and specialized tooling due to their inherent resistance to deformation. Hot forging, where the metal is heated to high temperatures, is commonly used to reduce the required force and improve the material's workability.
Powder Metallurgy
Powder metallurgy involves compacting and sintering fine metal powders to create a solid component. This method is particularly well-suited for producing complex shapes and controlling the material's microstructure.
With high-temperature metals, powder metallurgy offers the advantage of creating near-net-shape components, minimizing the need for extensive machining. However, achieving full density and avoiding contamination are critical challenges that require careful control of powder characteristics, compaction pressure, and sintering parameters. Hot isostatic pressing (HIP) is often used as a post-sintering step to eliminate residual porosity.
Modern Manufacturing Techniques: Innovation in Metalworking
While traditional methods continue to be refined, modern manufacturing techniques are opening new possibilities for high-temperature metal components. Additive manufacturing and advanced heat treatments are at the forefront of this innovation.
Additive Manufacturing (3D Printing)
Additive manufacturing, also known as 3D printing, builds components layer by layer from a digital design. This technology offers unprecedented freedom in creating complex geometries and customized designs.
For high-temperature metals, additive manufacturing techniques like selective laser melting (SLM) and electron beam melting (EBM) are gaining prominence. These methods enable the creation of intricate internal structures and optimized designs that were previously impossible to manufacture.
However, challenges remain in controlling the microstructure, residual stresses, and surface finish of additively manufactured high-temperature metal components. Further research and development are needed to fully realize the potential of this technology.
Heat Treatment
Heat treatment is a crucial step in optimizing the properties of high-temperature metal components, regardless of the manufacturing method used. By carefully controlling the heating and cooling cycles, engineers can tailor the material's microstructure to achieve desired strength, ductility, and creep resistance.
For example, solution annealing followed by aging is a common heat treatment process for superalloys, promoting the precipitation of strengthening phases within the material's microstructure. Understanding the specific heat treatment requirements for each alloy and application is essential for achieving peak performance.
Manufacturing and processing techniques, whether traditional or modern, are only part of the equation. The true test lies in validating that these materials and components can withstand the rigors of their intended applications. Rigorous testing and detailed characterization are essential steps in this validation process, ensuring the reliable performance of high-temperature metals in demanding environments.
Testing and Characterization: Ensuring Peak Performance
The development and application of high-temperature metals hinges on rigorous testing and characterization. These processes are not merely quality control checks, but crucial steps that ensure these materials perform reliably under extreme conditions.
Without thorough testing, even the most advanced alloys and manufacturing processes are essentially gambles. It is through meticulous evaluation that engineers and scientists can confidently deploy high-temperature metals in critical applications.
The Importance of Comprehensive Testing
The stakes are high. Failure of a component in a jet engine, a power plant turbine, or a chemical reactor can have catastrophic consequences, ranging from equipment damage and production downtime to potential safety hazards and environmental disasters.
Comprehensive testing is an investment in reliability, safety, and long-term performance. It provides the data necessary to predict material behavior, identify potential weaknesses, and optimize designs for maximum effectiveness.
Testing enables data-driven decision-making.
Mechanical Testing at Elevated Temperatures
Creep Testing: Measuring Long-Term Deformation
Creep is the slow, time-dependent deformation of a material under constant stress at high temperatures. Creep testing is essential for determining the long-term stability of high-temperature metals.
Dedicated creep testing machines apply a constant load to a specimen while maintaining a precise temperature. The resulting deformation is continuously monitored over extended periods, often thousands of hours.
The data obtained from creep testing is used to predict the lifespan of components under sustained stress at high temperatures and is crucial for safety-critical applications.
Tensile Testing: Assessing Strength and Ductility
Tensile testing measures a material's resistance to being pulled apart. Tensile testing machines with high-temperature furnaces are used to evaluate the tensile strength, yield strength, and ductility of high-temperature metals at operating temperatures.
This testing provides critical insights into how these metals behave under stress at extreme temperatures, mimicking real-world conditions.
The results help determine the maximum load a component can withstand before failure and provide essential data for structural design.
Microstructural Analysis and Material Characterization
Beyond mechanical testing, a suite of analytical techniques is employed to characterize the microstructure of high-temperature metals.
Microstructural Evaluation: Understanding Material Structure
Techniques such as optical microscopy, scanning electron microscopy (SEM), and transmission electron microscopy (TEM) reveal the grain size, phase distribution, and presence of any micro-defects within the material.
These observations provide insights into the material's processing history and its relationship to its mechanical properties.
For example, grain size and the presence of precipitates can significantly influence creep resistance and fatigue life.
Compositional Analysis: Ensuring Chemical Integrity
Techniques such as energy-dispersive X-ray spectroscopy (EDS) and X-ray diffraction (XRD) are used to determine the chemical composition and crystallographic structure of the material.
This information is critical for verifying that the alloy meets the specified composition requirements and for identifying any unwanted phases or contaminants that could degrade performance.
Non-Destructive Testing (NDT) Methods
Non-destructive testing methods are used to evaluate the integrity of components without causing damage. These techniques are particularly valuable for inspecting finished parts or components in service.
Ultrasonic Testing
Ultrasonic testing uses high-frequency sound waves to detect internal flaws such as cracks, voids, or inclusions.
Radiography
Radiography uses X-rays or gamma rays to create an image of the component's internal structure, revealing any hidden defects.
Dye Penetrant Inspection
Dye penetrant inspection uses a colored dye to highlight surface cracks or discontinuities.
Advanced Characterization Techniques
As technology advances, new characterization techniques are emerging to provide even deeper insights into the behavior of high-temperature metals.
These include:
- Synchrotron X-ray diffraction: Provides high-resolution structural information.
- Atom probe tomography: Maps the location of individual atoms within a material.
- Advanced modeling and simulation: Predict material behavior under complex conditions.
These advanced techniques, combined with traditional testing methods, are paving the way for the development of even more robust and reliable high-temperature materials for future applications.
Manufacturing and processing techniques, whether traditional or modern, are only part of the equation. The true test lies in validating that these materials and components can withstand the rigors of their intended applications. Rigorous testing and detailed characterization are essential steps in this validation process, ensuring the reliable performance of high-temperature metals in demanding environments. Now, let's shift our focus to the framework that governs the use of these advanced materials – the standards and regulations that dictate their performance and application.
Standards and Regulations: Meeting Industry Benchmarks
The utilization of high-temperature metals is not a free-for-all. Strict standards and regulations, often established by international organizations, ensure that these materials perform reliably and safely in demanding applications.
These benchmarks act as a safeguard, preventing catastrophic failures and ensuring consistency across industries.
The Role of ASTM International
ASTM International stands as a cornerstone in the world of materials engineering, setting the standards that define the properties and performance of countless materials, including high-temperature metals.
Its influence permeates industries ranging from aerospace to power generation, impacting design, manufacturing, and quality control processes.
ASTM standards related to high-temperature metals encompass a wide array of testing methodologies and performance criteria.
These include standards for tensile strength, creep resistance, fatigue life, and oxidation resistance, all critical parameters for ensuring the reliability of components operating at elevated temperatures.
Compliance with ASTM standards is not merely a suggestion, it is often a legal requirement or a prerequisite for obtaining certifications necessary for participation in certain industries.
Superalloys and Stringent Standards
Superalloys, with their exceptional high-temperature strength and corrosion resistance, play a crucial role in meeting the stringent standards set by organizations like ASTM.
These alloys are often the materials of choice for critical components in demanding applications, where failure is not an option.
The standards for superalloys are particularly rigorous, reflecting the high stakes associated with their applications.
For instance, in the aerospace industry, superalloys used in jet engine turbine blades must meet exacting standards for creep resistance and fatigue life to ensure safe and reliable operation.
The development and application of superalloys are inextricably linked to the evolution of testing methodologies and performance standards.
As new alloys are developed and existing ones are refined, testing methods must be adapted and standards updated to accurately reflect their properties and capabilities.
Beyond ASTM: A Landscape of Regulations
While ASTM International holds a prominent position, it is important to recognize that a broader landscape of regulations governs the use of high-temperature metals.
Industry-specific regulations, such as those imposed by the Federal Aviation Administration (FAA) for aerospace applications or by the American Society of Mechanical Engineers (ASME) for pressure vessels, add another layer of oversight.
These regulations often incorporate or reference ASTM standards, but they may also include additional requirements tailored to the specific needs and risks of each industry.
Navigating this complex web of standards and regulations can be challenging, requiring a deep understanding of materials science, engineering principles, and legal requirements.
However, adherence to these benchmarks is essential for ensuring the safe and reliable operation of high-temperature components and systems.
Manufacturing and processing techniques, whether traditional or modern, are only part of the equation. The true test lies in validating that these materials and components can withstand the rigors of their intended applications. Rigorous testing and detailed characterization are essential steps in this validation process, ensuring the reliable performance of high-temperature metals in demanding environments. Now, let's shift our focus to the framework that governs the use of these advanced materials – the standards and regulations that dictate their performance and application.
The Future of High-Temperature Metals: Innovation on the Horizon
The landscape of high-temperature metals is not static; it's a dynamic field driven by ever-increasing demands from industries pushing the boundaries of technology. The future promises exciting advancements in materials science, fueled by ongoing research and the quest for even greater performance. Let's delve into the emerging trends and research that are shaping the next generation of these critical materials.
The Quest for Novel Alloys
The development of new alloys remains a central focus. Researchers are exploring innovative compositions and microstructures.
-
Focus on Intermetallics: These materials, compounds formed between two or more metals, exhibit unique combinations of high-temperature strength and oxidation resistance.
Their inherent order at the atomic level contributes to their stability in extreme environments.
-
High-Entropy Alloys (HEAs): HEAs, also known as multi-principal element alloys, are revolutionizing alloy design. They consist of five or more elements in near-equal proportions.
This unconventional approach often leads to unprecedented properties and performance characteristics.
-
Nanomaterials Integration: Incorporating nanoparticles into metal matrices can significantly enhance their mechanical properties.
This includes creep resistance and fatigue life at elevated temperatures. The challenge lies in achieving uniform dispersion and strong bonding between the nanoparticles and the metal matrix.
Advanced Processing Techniques
Beyond alloy composition, advancements in processing techniques are crucial for realizing the full potential of high-temperature metals.
-
Additive Manufacturing (3D Printing): Additive manufacturing is transforming the way high-temperature metal components are produced.
This technology enables the creation of complex geometries and customized microstructures. It opens doors to optimizing performance and reducing material waste.
-
Severe Plastic Deformation (SPD): SPD techniques, such as equal channel angular pressing (ECAP), can refine the grain structure of metals to the nanoscale.
This leads to significant improvements in strength and creep resistance.
-
Advanced Coating Technologies: Surface coatings play a vital role in protecting high-temperature metals from oxidation and corrosion.
Researchers are developing new coating materials and deposition techniques. This is to extend the lifespan and reliability of components in harsh environments. Examples include thermal barrier coatings (TBCs) and environmental barrier coatings (EBCs).
Driving Demand: Advanced Technologies
The demand for high-temperature metals is being propelled by advancements across numerous industries.
-
Hypersonic Flight: The development of hypersonic aircraft and spacecraft requires materials that can withstand extreme temperatures and aerodynamic stresses.
This is driving research into new high-temperature alloys and ceramic matrix composites.
-
Advanced Nuclear Reactors: Next-generation nuclear reactors, such as molten salt reactors and fusion reactors, operate at much higher temperatures than conventional reactors.
This necessitates the development of high-temperature materials. They must be resistant to radiation damage and corrosion.
-
High-Efficiency Power Generation: Efforts to improve the efficiency of power generation systems, such as gas turbines and combined cycle power plants, are pushing the limits of high-temperature materials.
Higher operating temperatures translate to greater thermodynamic efficiency.
The future of high-temperature metals is bright, with ongoing research and innovation paving the way for new materials and technologies. As industries continue to demand greater performance and reliability in extreme environments, the quest for advanced high-temperature metals will only intensify, driving further progress in this critical field.