Electronic Balance: Find the Right One for You!
An electronic balance, a cornerstone in modern metrology, offers precise mass measurements crucial for various applications ranging from pharmaceutical research conducted in laboratories to quality control processes implemented in manufacturing plants. These balances often incorporate sophisticated load cells which convert force into measurable electrical signals, thereby ensuring accuracy far exceeding that of traditional mechanical balances. Furthermore, compliance with standards set by organizations like the International Organization for Standardization (ISO) dictates the calibration and operation protocols of any electronic balance to maintain traceability and reliability of measurement data.
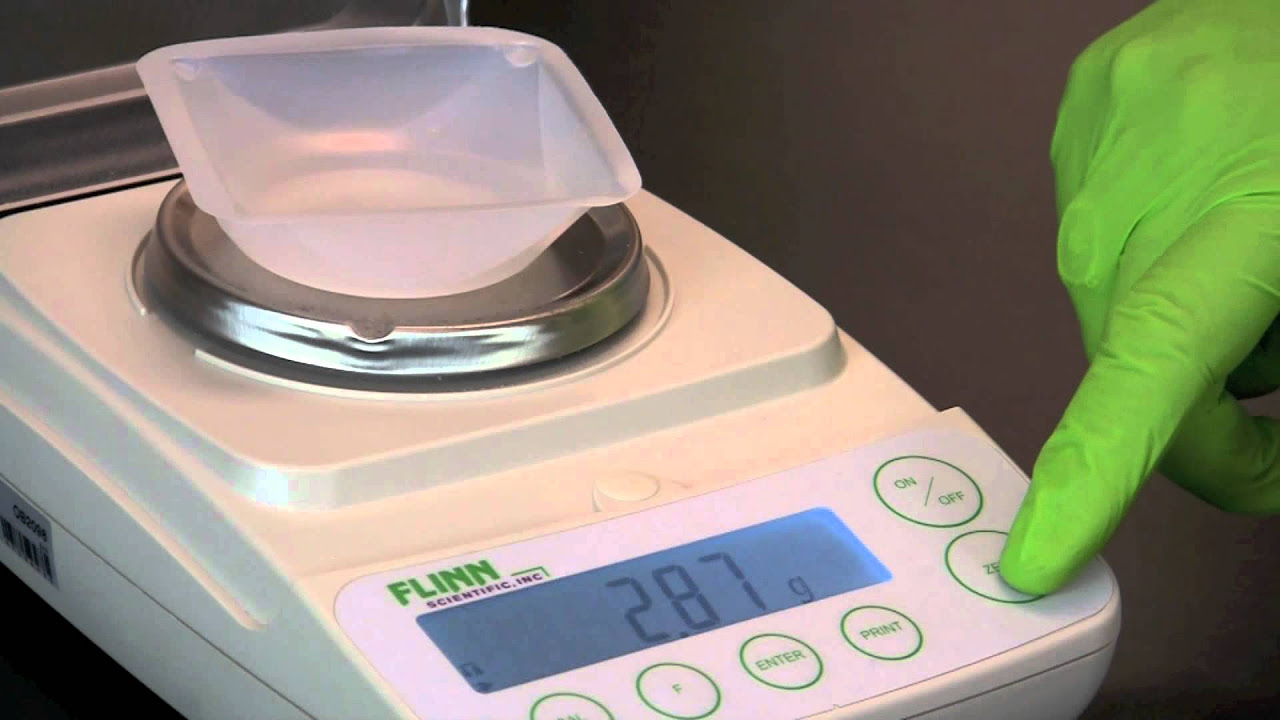
Image taken from the YouTube channel Bio-Rad Laboratories , from the video titled Using an Electronic Balance .
Electronic balances, also known as digital balances, represent a significant advancement in weighing technology. These sophisticated instruments provide highly accurate and precise weight measurements, critical for a multitude of applications across diverse sectors.
But what exactly sets them apart, and why are they so important? This section explores the fundamental aspects of electronic balances, contrasting them with traditional weighing scales and underscoring their vital role in industries demanding the utmost accuracy.
Defining the Electronic Balance
At its core, an electronic balance is a device designed to determine the mass of an object with a high degree of accuracy. It relies on electronic sensors and circuitry to convert the force exerted by an object's weight into an electrical signal, which is then processed and displayed as a digital reading.
Unlike simpler scales, electronic balances are engineered for precision. They incorporate advanced technologies to minimize errors and ensure reliable measurements, making them indispensable tools in various scientific, industrial, and commercial settings.
Electronic Balance vs. Traditional Weighing Scale: A Comparative Look
While both electronic balances and traditional weighing scales serve the purpose of measuring weight, their underlying principles and performance characteristics differ significantly. Traditional scales typically rely on mechanical mechanisms, such as springs or levers, to determine weight. These mechanisms are prone to wear and tear, leading to reduced accuracy over time.
In contrast, electronic balances utilize electronic load cells to measure weight. These cells convert the applied force into an electrical signal, which is then amplified and processed by a microprocessor. This electronic approach offers several advantages:
-
Higher Accuracy: Electronic balances provide significantly more accurate and precise measurements compared to traditional scales.
-
Digital Readout: The digital display eliminates parallax errors associated with reading analog scales.
-
Advanced Features: Many electronic balances offer advanced features such as tare function, multiple weighing units, and data connectivity.
-
Less Susceptible to Wear: Electronic components are generally less susceptible to wear and tear compared to mechanical components, resulting in longer lifespan and consistent performance.
The Critical Importance of Accurate Weighing
The need for precise and accurate weighing is paramount in a wide range of fields.
In the pharmaceutical industry, for example, even slight variations in ingredient quantities can have significant consequences for drug efficacy and safety. Similarly, in scientific research, accurate weighing is essential for obtaining reliable experimental results.
Here are some other highlights:
-
Manufacturing: Precise measurements are critical for quality control, ensuring products meet specified weight requirements.
-
Food Industry: Accurate weighing is crucial for portion control, nutritional labeling, and compliance with food safety regulations.
-
Chemical Industry: Precise measurements are critical for formulation and compound ratios.
From ensuring the quality of pharmaceuticals to maintaining consistency in manufacturing processes, electronic balances play a crucial role in maintaining accuracy, reliability, and safety across diverse sectors. Their ability to provide precise and repeatable measurements makes them indispensable tools in today's increasingly demanding world.
Core Components and Their Functions
Electronic balances, also known as digital balances, represent a significant advancement in weighing technology. These sophisticated instruments provide highly accurate and precise weight measurements, critical for a multitude of applications across diverse sectors. But what exactly sets them apart, and why are they so important? This section explores the key internal components that enable these balances to deliver such reliable results.
Each component plays a crucial role in the overall function of the balance, working in harmony to convert the mass of an object into a precise digital readout. Understanding these components is key to appreciating the technology behind accurate weighing.
The Load Cell: The Heart of the Measurement
The load cell is arguably the most critical component of an electronic balance. It acts as the primary weight-sensing element. Its function is to convert the force of an object's mass into an electrical signal. This signal is then processed to determine the weight. Different types of load cells exist, but strain gauge load cells are the most common in electronic balances.
Strain Gauge Technology
Strain gauges are small, resistive sensors that are bonded to a flexible element within the load cell. When weight is applied, the element deforms, causing the strain gauges to either stretch or compress. This deformation changes the electrical resistance of the strain gauges. This change in resistance is proportional to the applied force, which can then be measured precisely.
The load cell, using strain gauges, provides an analog signal that represents the weight placed on the balance. This signal is then sent to the next critical component for conversion.
Analog-to-Digital Converter (ADC): Bridging the Gap
The Analog-to-Digital Converter (ADC) plays a vital role in translating the analog signal received from the load cell into a digital format that the balance's microprocessor can understand. The ADC samples the continuous analog signal at regular intervals and assigns a discrete digital value to each sample.
This digital representation of the weight allows for precise calculations and processing by the balance's internal computer. The resolution of the ADC directly affects the readability and accuracy of the balance. A higher resolution ADC provides a more precise digital representation of the analog signal, resulting in more accurate weight readings.
Microprocessor: The Brain of the Balance
The microprocessor is the central processing unit of the electronic balance. It acts as the "brain" of the instrument. It receives the digitized signal from the ADC and performs a series of calculations to determine the weight of the object.
The microprocessor also controls other functions of the balance, such as:
- Calibration routines.
- Tare function.
- Unit conversion.
- Display output.
Sophisticated algorithms are used to compensate for environmental factors such as temperature and drift, ensuring optimal accuracy and stability.
Display (LCD, LED): Presenting the Data
The display, whether it be an LCD (Liquid Crystal Display) or an LED (Light Emitting Diode) screen, serves as the primary interface for presenting the weight measurement to the user.
The display provides a clear and easy-to-read readout of the weight in the selected unit of measurement. Advanced balances may also display additional information such as:
- Stability indicators.
- Calibration status.
- Error messages.
The quality and clarity of the display are important for user experience and minimizing reading errors.
Weighing Pan: The Interface for Measurement
The weighing pan is the surface on which the object to be measured is placed. It is designed to be stable and level, ensuring that the weight is evenly distributed across the load cell.
The material and construction of the weighing pan can affect the balance's performance. High-quality pans are typically made of stainless steel. Stainless steel is durable and easy to clean. This minimizes the risk of contamination and ensures accurate measurements.
Tare Function: Zeroing for Accuracy
The tare function is a critical feature that allows the user to zero the balance with a container or packaging on the weighing pan. This function is essential for obtaining accurate net weight measurements.
By pressing the tare button, the balance subtracts the weight of the container from the total weight. Only the weight of the substance within the container is displayed. The tare function significantly improves the efficiency and accuracy of weighing processes in various applications.
Leveling Feet/Bubble Level: Ensuring Stability
Leveling feet and a bubble level are essential for ensuring that the electronic balance is perfectly level. Even slight deviations from a level position can affect the accuracy of the weight readings.
The bubble level provides a visual indication of whether the balance is level. The leveling feet can be adjusted to bring the bubble into the center of the level. Regularly checking and adjusting the leveling is crucial for maintaining the balance's accuracy and reliability.
Key Performance Characteristics Explained
Electronic balances, also known as digital balances, represent a significant advancement in weighing technology. These sophisticated instruments provide highly accurate and precise weight measurements, critical for a multitude of applications across diverse sectors.
But what exactly sets them apart, and why are they indispensable in fields ranging from pharmaceutical research to quality control? The answer lies in understanding their key performance characteristics.
These characteristics define the quality, reliability, and suitability of an electronic balance for specific tasks. Examining these critical metrics helps to ensure that your measurements are dependable.
Let's delve into the core performance characteristics that determine the efficacy of an electronic balance.
Understanding Accuracy
Accuracy is paramount in any measurement instrument, and electronic balances are no exception. It refers to the closeness of a measurement to the true, accepted value of the object being weighed.
A balance with high accuracy will provide readings that are very close to the actual weight of the sample. In simpler terms, if you are weighing a calibrated 100g weight, an accurate balance should display a value very close to 100g.
The smaller the deviation from the true value, the higher the accuracy of the balance. Accuracy is often expressed as a percentage of the full capacity of the balance or as a specific weight unit (e.g., ±0.1 mg).
Linearity: Consistency Across the Weighing Range
Linearity reflects the balance's ability to provide accurate measurements across its entire weighing range. Ideally, an electronic balance should exhibit a linear response, meaning that the accuracy should remain consistent whether you are weighing a light object or a heavy one.
A non-linear balance might be accurate at one end of its weighing range but less accurate at the other. Linearity is typically assessed by weighing multiple calibrated weights across the balance's range and comparing the measured values to the known values.
Any deviation from a straight-line relationship between the applied weight and the displayed reading indicates non-linearity.
Repeatability: Consistency in Repeated Measurements
Repeatability, also known as precision, refers to the balance's ability to provide consistent readings when the same object is weighed multiple times under identical conditions.
A highly repeatable balance will yield nearly identical results each time the same weight is placed on the pan. This characteristic is crucial for applications where consistency is vital.
For example, in pharmaceutical compounding, where minute variations in ingredient weights can affect the efficacy of a medication, high repeatability is essential.
Repeatability is usually quantified by calculating the standard deviation of a series of measurements. A smaller standard deviation indicates better repeatability.
Readability (Resolution): The Smallest Displayed Increment
Readability, also referred to as resolution, is the smallest increment that the balance can display. It essentially determines the level of detail in the weight measurement.
A balance with a readability of 0.1 mg can display weight changes as small as 0.1 mg. Higher readability is necessary for applications requiring very precise measurements, such as analytical chemistry or micro weighing.
It is essential to choose a balance with a readability appropriate for the specific application.
Capacity: The Maximum Weighing Limit
The capacity of an electronic balance is the maximum weight it can accurately measure. Exceeding the capacity can damage the balance and lead to inaccurate readings.
It's crucial to select a balance with a capacity that adequately covers the range of weights you anticipate measuring. Consider the heaviest samples you'll be weighing and choose a balance with a suitable capacity and safety margin.
Stabilization Time: Achieving a Stable Reading Quickly
Stabilization time is the time it takes for the balance to display a stable and accurate reading after a weight is placed on the pan. A shorter stabilization time improves efficiency, especially when performing numerous measurements.
Balances with advanced damping systems and signal processing algorithms generally offer faster stabilization times. Stabilization time can be affected by environmental factors such as vibrations and air currents.
Exploring Different Types of Electronic Balances
Electronic balances, also known as digital balances, represent a significant advancement in weighing technology. These sophisticated instruments provide highly accurate and precise weight measurements, critical for a multitude of applications across diverse sectors.
But what exactly sets them apart, and why are there so many types available? The answer lies in the diverse needs of various industries and the specific weighing requirements they demand. Let's delve into the world of electronic balances, exploring their distinct types, features, and specialized applications.
Analytical Balances: The Pinnacle of Precision
Analytical balances are the gold standard for applications demanding the highest degree of accuracy. These balances, commonly found in research laboratories and quality control settings, offer readability down to 0.0001 grams (0.1 mg) or even finer.
Their sensitivity necessitates a draft shield or enclosure to minimize the impact of air currents on measurements.
Key features of analytical balances include:
- High Resolution: Essential for measuring minute weight differences.
- Draft Shield: Crucial for maintaining a stable weighing environment.
- Internal Calibration: Many analytical balances feature automatic internal calibration for optimal accuracy.
Precision Balances: Versatility and Accuracy
Precision balances strike a balance between high accuracy and practical usability. While not as sensitive as analytical balances, they still offer excellent readability, typically in the range of 0.001 grams (1 mg) to 0.1 grams.
Their robust design and ease of use make them suitable for a wide range of applications.
Precision balances find use in:
- General Lab Work: Preparing solutions, weighing chemicals, and conducting experiments.
- Quality Control: Ensuring product consistency and meeting regulatory standards.
- Education: Providing students with accurate and reliable weighing instruments.
Toploading Balances: A Workhorse for Various Industries
Toploading balances are known for their ease of use and versatility. With the weighing pan located on top of the unit, they accommodate a wide variety of sample sizes and shapes.
These balances are commonly used in:
- Laboratories: General weighing tasks, formulation, and sample preparation.
- Industrial Settings: Weighing components, raw materials, and finished products.
- Food Processing: Portion control and ingredient measurement.
Moisture Analyzers: Determining Moisture Content with Precision
Moisture analyzers combine the functionality of an electronic balance with a built-in heating element. These instruments are specifically designed to determine the moisture content of various materials.
The sample is heated, and the weight loss due to evaporation is continuously monitored.
Moisture Analyzers are crucial for:
- Food Science: Determining the shelf life and quality of food products.
- Pharmaceuticals: Ensuring the stability and efficacy of drugs.
- Material Science: Characterizing the properties of various materials.
Industrial Balances: Ruggedness and High Capacity
Industrial balances are built to withstand the rigors of harsh industrial environments. These balances boast high capacities and durable construction.
They are designed for weighing large objects and handling heavy loads.
Typical applications include:
- Manufacturing: Weighing raw materials, components, and finished goods.
- Shipping and Receiving: Verifying package weights and ensuring accurate inventory management.
- Waste Management: Weighing waste materials for disposal and recycling.
Counting Scales: Efficient Inventory Management
Counting scales streamline inventory management by accurately counting items based on their weight. By weighing a sample of known quantity, the scale calculates the weight of a single item and then counts the total number of items placed on the pan.
They significantly improve accuracy and efficiency compared to manual counting methods.
These scales are beneficial for:
- Parts Manufacturing: Counting small components and fasteners.
- Retail: Inventory control and order fulfillment.
- Warehousing: Streamlining inventory management processes.
Bench Scales: Versatile and Robust Weighing Solutions
Bench scales are versatile weighing solutions designed for a variety of applications. These scales, typically placed on a workbench or tabletop, offer a balance of accuracy, capacity, and durability.
Bench scales find applications in:
- Food Processing: Portion control and batch weighing.
- Manufacturing: Quality control and component weighing.
- Shipping and Receiving: Package weighing and inventory management.
Each type of electronic balance caters to specific needs, ensuring accurate and reliable weighing across a multitude of applications. The right choice depends on the required precision, capacity, environmental factors, and specific functionalities needed for the task at hand.
Calibration and Best Practices for Accuracy
Electronic balances, also known as digital balances, represent a significant advancement in weighing technology. These sophisticated instruments provide highly accurate and precise weight measurements, critical for a multitude of applications across diverse sectors.
But what exactly sets them apart, and how can their accuracy be ensured? This section delves into the critical process of calibration and the significance of employing best practices, such as utilizing a draft shield, to achieve optimal balance performance.
The Paramount Importance of Calibration
Calibration is not merely a procedural step; it is the cornerstone of reliable weighing. An electronic balance, however precise its components, is susceptible to drift over time. Environmental factors, wear and tear, and even subtle shifts in its internal mechanisms can compromise accuracy.
Calibration corrects for these deviations, ensuring that the balance provides readings that are traceable to recognized measurement standards. It involves comparing the balance's output against a known weight and adjusting the instrument to minimize any discrepancies.
Without regular calibration, measurements become suspect, potentially leading to inaccurate results and flawed decision-making across diverse applications. Therefore, implementing a robust calibration schedule is indispensable for maintaining data integrity and operational excellence.
Internal vs. External Calibration: Choosing the Right Method
The world of electronic balances offers two primary calibration methodologies: internal and external. Each approach offers distinct advantages, catering to specific needs and operational contexts.
Internal Calibration: Automation and Convenience
Internal calibration is characterized by its automated and user-friendly nature. Balances equipped with this feature possess an internal calibration weight and motorized mechanism. With the press of a button, the balance initiates a self-calibration process, eliminating the need for manual intervention.
This method excels in environments where frequent calibration is required, such as in dynamic laboratory settings or when fluctuations in temperature are common. The convenience and speed of internal calibration minimize downtime and streamline workflows, maximizing productivity.
External Calibration: Traceability and Precision
External calibration involves using a precisely calibrated external weight, traceable to a national or international metrology institute (like NIST or OIML). This method offers a higher level of traceability and allows for independent verification of the balance's accuracy.
External calibration is particularly advantageous in industries that demand the highest levels of measurement certainty, such as pharmaceutical manufacturing or forensic science. The use of certified external weights ensures that the balance's performance aligns with rigorous regulatory standards.
The choice between internal and external calibration hinges on weighing the trade-offs between automation and traceability. While internal calibration provides convenience and speed, external calibration provides unparalleled confidence in measurement accuracy and traceability.
The Significance of a Draft Shield (Windshield)
Even the most meticulously calibrated electronic balance can be compromised by external influences. Air currents, vibrations, and temperature fluctuations can introduce significant errors into weighing processes.
A draft shield, also known as a windshield, serves as a protective barrier, isolating the weighing pan from these disturbances. Constructed from transparent materials like glass or plastic, draft shields enclose the weighing area, minimizing the impact of environmental factors on measurement stability.
The importance of using a draft shield cannot be overstated, especially when working with highly sensitive analytical balances or when measuring small quantities. By reducing the effects of air currents and other external influences, a draft shield ensures that the balance provides the most accurate and reliable readings possible.
Investing in a quality draft shield and making its use a standard operating procedure demonstrates a commitment to data integrity and precision measurement.
Units of Measurement in Electronic Balances
Electronic balances, also known as digital balances, represent a significant advancement in weighing technology. These sophisticated instruments provide highly accurate and precise weight measurements, critical for a multitude of applications across diverse sectors. A crucial aspect of understanding and utilizing electronic balances effectively lies in comprehending the various units of measurement they employ. These units provide a standardized language for quantifying mass, ensuring consistency and accuracy in scientific, industrial, and commercial settings.
Common Units and Their Applications
Electronic balances are capable of displaying weight in a variety of units, catering to the specific needs of different industries and applications. Understanding these units is crucial for accurate data interpretation and effective communication.
-
Grams (g): The gram is a fundamental unit of mass in the metric system. It is extensively used in scientific research, pharmaceutical compounding, and general laboratory work.
-
Milligrams (mg): Representing one-thousandth of a gram, milligrams are used when extreme precision is required. This is particularly important in pharmaceutical analysis and microchemistry.
-
Ounces (oz): A unit of weight in the imperial system, the ounce is commonly used in the food industry and in commercial transactions where the imperial system is prevalent.
-
Pounds (lbs): Another unit of weight in the imperial system, the pound is frequently used for larger quantities. It is commonly seen in shipping, manufacturing, and other industrial applications.
-
Carats (ct): Specifically used for measuring the mass of gemstones, particularly diamonds, the carat is a standardized unit ensuring fair trade and accurate valuation. One carat is equivalent to 200 milligrams.
Unit Conversion and Its Importance
Electronic balances often allow users to switch between different units of measurement. This feature is incredibly useful for adapting to different standards and requirements. Accurate unit conversion is essential to avoid errors and ensure data integrity.
It's important to note that improper unit conversions can lead to significant discrepancies. This, in turn, affects calculations and ultimately the outcome of experiments or processes.
Therefore, operators must exercise caution. They must double-check conversion factors, and familiarize themselves with the balance's unit conversion functions.
Standards and Best Practices
While electronic balances provide a range of units, it is critical to adhere to industry-specific standards and best practices regarding measurement units. For example, scientific publications typically require data to be reported in metric units (grams, milligrams). Following these conventions ensures consistency and comparability across different studies.
Accurate weighing necessitates a deep understanding of units. Proper unit selection and conversion are critical for achieving reliable results. By understanding these concepts, users can harness the full potential of their balances. This, in turn, provides precise data and enables informed decision-making.
Applications Across Diverse Industries
Electronic balances, also known as digital balances, represent a significant advancement in weighing technology. These sophisticated instruments provide highly accurate and precise weight measurements, critical for a multitude of applications across diverse sectors. A crucial aspect of understanding and utilizing these balances effectively lies in recognizing their extensive applications across diverse industries.
Here's an in-depth look at their use in various fields:
Laboratory Applications: Precision in Scientific Research
Electronic balances are indispensable tools in any laboratory setting. They are critical for preparing solutions, measuring reagents, and accurately weighing samples for analysis. The high precision of analytical balances, in particular, ensures the reliability of experimental results.
Researchers rely on these balances for:
- Quantitative chemical analysis
- Gravimetric analysis
- Preparation of standard solutions
- Material characterization
Accurate measurements are paramount, as even minute errors can significantly impact experimental outcomes and the validity of research findings.
Pharmaceutical Industry: Ensuring Accurate Formulations
In the pharmaceutical industry, precision is not merely a matter of accuracy; it is a matter of patient safety and regulatory compliance. Electronic balances play a crucial role in ensuring the accurate weighing of ingredients used in drug formulations.
This precision is essential for:
- Dosage accuracy
- Quality control of raw materials
- Verification of final product weight
Pharmaceutical companies must adhere to stringent guidelines and regulations, such as those set forth by the FDA, making precise weighing a non-negotiable aspect of their operations. Electronic balances help to uphold the integrity of pharmaceutical products and maintain consumer confidence.
Food Industry: Maintaining Consistency and Quality
The food industry relies heavily on electronic balances for portion control, ingredient measurement, and ensuring consistent product quality. From small-scale bakeries to large-scale food processing plants, these balances are vital for:
- Standardizing recipes
- Monitoring product weight to meet labeling requirements
- Ensuring uniform serving sizes
- Controlling food costs by optimizing ingredient usage
Maintaining consistency is key to customer satisfaction and brand reputation. Electronic balances enable food manufacturers to meet these demands efficiently and accurately.
Manufacturing: Quality Control and Process Optimization
In manufacturing, electronic balances are used extensively for quality control, process optimization, and ensuring products meet specific weight requirements. From automotive parts to electronic components, these balances facilitate:
- Weight verification of individual components
- Batch weighing for production processes
- Monitoring material usage for cost efficiency
- Identifying deviations from specified weight tolerances
By integrating electronic balances into their quality control processes, manufacturers can minimize errors, reduce waste, and ensure the consistent quality of their products.
Jewelry: Weighing Precious Metals with Precision
The jewelry industry demands extremely precise measurements when dealing with precious metals and gemstones. The value of these materials is directly proportional to their weight, making accurate weighing critical for:
- Determining the value of raw materials
- Pricing finished jewelry pieces
- Ensuring fair trade practices
Analytical balances are commonly used in this industry to provide the level of precision required when weighing gold, silver, platinum, and other valuable materials. Even the slightest error can have significant financial implications.
Standards, Compliance, and Regulatory Bodies
Electronic balances, also known as digital balances, represent a significant advancement in weighing technology. These sophisticated instruments provide highly accurate and precise weight measurements, critical for a multitude of applications across diverse sectors. A crucial aspect of understanding and utilizing electronic balances effectively lies in recognizing the vital roles played by standards, compliance, and the regulatory bodies that govern their performance and reliability. These entities ensure that electronic balances meet stringent requirements, guaranteeing accuracy, consistency, and trustworthiness in various applications.
The Role of NIST
The National Institute of Standards and Technology (NIST) plays a pivotal role in establishing and maintaining measurement standards within the United States. As a non-regulatory agency within the U.S. Department of Commerce, NIST's mission is to promote U.S. innovation and industrial competitiveness by advancing measurement science, standards, and technology.
NIST's influence on electronic balances is significant.
The institute develops and disseminates Standard Reference Materials (SRMs), which are certified reference materials used to calibrate and verify the accuracy of weighing instruments.
Manufacturers of electronic balances often rely on NIST standards to ensure their products meet the required levels of precision and accuracy. This reliance helps guarantee that balances used across various industries provide consistent and reliable measurements.
OIML and Global Harmonization
The International Organization of Legal Metrology (OIML) is an intergovernmental organization that aims to harmonize legal metrology procedures worldwide. OIML develops model regulations, standards, and related documents to promote uniformity in legal metrology.
OIML's work is essential for facilitating international trade and ensuring fair competition.
By harmonizing measurement standards, OIML helps eliminate technical barriers to trade that may arise from differing national regulations.
For electronic balances, OIML standards provide a framework for manufacturers to design and produce instruments that meet globally recognized requirements for accuracy and performance. This standardization promotes consistency and reliability in weighing operations across different countries and regions.
USP and Pharmaceutical Standards
The United States Pharmacopeia (USP) is a scientific nonprofit organization that sets standards for the identity, strength, quality, and purity of medicines, food ingredients, and dietary supplements manufactured, distributed, and consumed worldwide. USP standards are recognized and enforced in the United States by the Food and Drug Administration (FDA).
In the pharmaceutical industry, accurate weighing is paramount to ensure the safety and efficacy of drug products.
USP provides detailed guidelines for the use and calibration of balances in pharmaceutical manufacturing and quality control.
These guidelines specify the requirements for balance accuracy, repeatability, and linearity. They also outline procedures for balance qualification, calibration, and maintenance. Compliance with USP standards is essential for pharmaceutical companies to meet regulatory requirements and ensure the quality of their products.
GLP/GMP Compliance
Good Laboratory Practice (GLP) and Good Manufacturing Practice (GMP) are quality assurance systems designed to ensure the reliability and integrity of data generated in laboratories and the quality of products manufactured in industrial settings. Compliance with GLP and GMP is critical in industries such as pharmaceuticals, biotechnology, and food processing.
Electronic balances play a vital role in GLP/GMP-compliant operations.
To meet GLP/GMP requirements, balances must be properly qualified, calibrated, and maintained. Detailed records of balance performance, calibration, and maintenance must be kept to demonstrate compliance. Regular audits and inspections are conducted to verify that GLP/GMP requirements are being met.
Compliance with GLP/GMP helps ensure the accuracy and reliability of weighing data, which is essential for making informed decisions and maintaining product quality.
Key Features, Considerations, and Purchasing Factors
Electronic balances, also known as digital balances, represent a significant advancement in weighing technology. These sophisticated instruments provide highly accurate and precise weight measurements, critical for a multitude of applications across diverse sectors. A crucial aspect of understanding and selecting an electronic balance involves considering the key features, factors, and considerations that align with specific needs and applications. When purchasing, navigating the choices and options necessitates a careful evaluation.
Essential Features to Evaluate
Selecting the appropriate electronic balance requires a thorough understanding of the features that dictate its suitability for a given task.
These features range from fundamental capabilities to subtle nuances that can significantly impact usability and performance.
Units of Measurement: Tailoring the Balance to Your Needs
The units of measurement supported by an electronic balance are a primary consideration. Ensure that the balance provides the necessary units for your application, whether it's grams (g), milligrams (mg), ounces (oz), pounds (lbs), carats (ct), or more specialized units.
Durability: Withstanding the Rigors of the Environment
Durability is paramount, particularly in industrial or harsh environments.
The balance should be constructed from robust materials capable of withstanding the intended environment, including resistance to dust, moisture, and physical impacts.
Navigating Cost and Value
While budget constraints are always a factor, prioritizing the long-term value and reliability of an electronic balance is crucial.
Price: Balancing Budget and Performance
A thorough cost analysis is essential, comparing features and benefits across different models. However, the lowest price doesn’t always equal the best value.
Consider the total cost of ownership, including potential maintenance, calibration, and replacement costs.
Critical Technical Considerations
Beyond the basic features, several technical aspects significantly influence the accuracy and usability of an electronic balance.
Calibration Method: Ensuring Accuracy over Time
The calibration method, whether internal or external, is a key consideration. Internal calibration offers convenience, while external calibration may be necessary for applications requiring the highest levels of accuracy and traceability.
Choosing the right calibration method depends on the specific requirements of your application and the level of precision needed.
Support and Longevity
The long-term value of an electronic balance depends not only on its initial quality but also on the support and warranty provided by the manufacturer.
Warranty: Protecting Your Investment
Always check the warranty coverage details carefully. A comprehensive warranty can provide peace of mind and protect against unexpected repairs or replacements.
Customer Support: Ensuring Ongoing Assistance
Evaluate the availability of technical assistance and support from the manufacturer. Reliable customer support can be invaluable in resolving issues, providing training, and ensuring the ongoing performance of the balance.
Video: Electronic Balance: Find the Right One for You!
Frequently Asked Questions: Electronic Balances
What's the key difference between precision and analytical electronic balances?
Precision electronic balances offer high accuracy with more capacity, typically measuring to 0.01g or 0.001g. Analytical electronic balances are ultra-precise, reading to 0.0001g or even better, but often have lower capacity. The choice depends on your required accuracy and sample size.
What factors affect the accuracy of an electronic balance?
Several things affect accuracy: calibration, environmental conditions (temperature, vibrations, air currents), proper leveling, and sample placement. Always ensure your electronic balance is calibrated regularly and used in a stable environment for best results.
How do I choose the right capacity for my electronic balance?
Select a capacity that comfortably exceeds the weight of your heaviest sample. Consider potential future needs too. Exceeding an electronic balance's capacity can damage it and void the warranty.
What are some common applications for electronic balances?
Electronic balances are used in many fields: laboratories (research, quality control), pharmacies (compounding), jewelry stores (weighing precious metals), and manufacturing (portion control, material verification). Different applications require different levels of accuracy from the electronic balance.
So, there you have it! Finding the right electronic balance might seem daunting, but with a little research and some clear understanding of your needs, you'll be weighing like a pro in no time. Happy balancing!